Cooling of laser cutting machines with compressed air
Industry: | Laser technology |
Customer/Location/Year: | Horstmann, Verl (Germany), 2008 |
Use of compressed air: | Process air |
Installed products: | BEKOKAT |
Laser cutting belongs to the thermal cutting processes. This is noticeable well before the focal point where the laser beam is incident on the material to be cut. Things already heat up in the beam path in front of it. Here, cooling is asked for. Best and most cost-effectively with compressed air. However, this air must be absolutely oil-free.
The Horstmann GmbH & Co. KG, domiciled in Verl near Gütersloh, Germany. has applied itself to top-quality and superior metal working for well-known customers from numerous industrial sectors, including the automobile and shipbuilding industry, and the machine-, plant- and tool construction branch.
The laser cutting machines which are indefatigably in operation at Horstmann would nevertheless react extremely allergically even to this minimal oil introduction, namely with a noticeable reduction in efficiency and quality. Because their razor-sharp laser beams would literally be reduced to a slack and unsteady old "oil lamp". Different from what one may assume, the compressed air at the Horstmann laser cutting machines is not used for the pneumatics but exclusively for the cooling of the laser beam path.
In principle, a cutting plant with a CO2 laser consists of a laser beam source and movable focussing optics which, in most cases, is a concave mirror or a collecting lens. From the source, the laser beam is led to the processing optics via deflecting mirrors. There, the laser beam is focussed to generate the power density required for cutting. At Horstmann, where primarily stainless-steel plates are cut, this comes up to a beam power of up to six kW. By the way, this is enough to easily penetrate the human body entirely
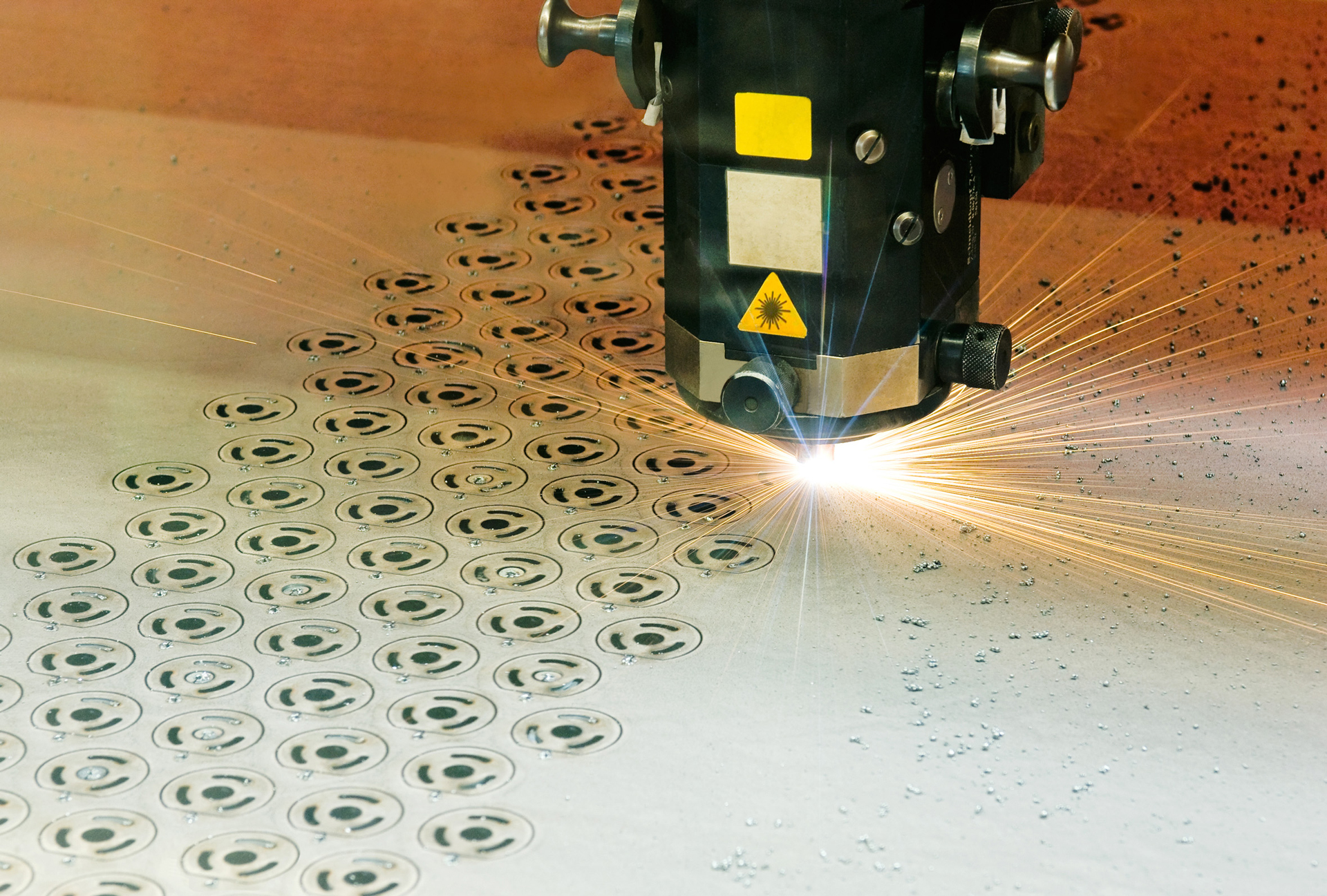
As the movable "cantilevered" optics move over the plates to be treated, their distance to the stationary laser source constantly changes. However, the generated laser beam does not have the required parallelism to transfer it over the sometimes large and varying distances. Therefore, and in order to reduce the thermal stress of the deflecting mirrors, the laser beam is, to some extent, slightly enlarged using a reflecting telescope.
The true beam line between the laser source and the focusing optics proceeds via gold- or molybdenum-coated mirrors which are manufactured mostly either out of pure copper or monocrystalline silicon. Extremely sensitive to oil or aerosols which settle on them, requiring premature and very costly replacement.
In the entire beam path of the laser, considerable temperatures develop by nature. Without cooling, the materials employed here, such as the deflecting mirrors or, even faster, the bellows of the movable optical unit, would suffer severe damage.
This vitally important cooling function is taken over by compressed air which is injected into the beam path. It must be absolutely free from particles and oil, as well as dry in order neither to "disperse" the laser beam by suspended particles nor to contaminate the deflecting mirrors through settlements. Even the smallest fractions of oil or aerosols in the compressed air would quickly have severe consequences for the process reliability and the profitability of the cutting plant.
Both factors, along with an absolute product quality, are however essential constituents of the lasting business success for Heinrich Horstmann GmbH & Co. KG. Therefore, the company gives enormous attention to the compressed-air processing subject-matter.
Previously, Horstmann - like almost all compressed-air users with similar requirements - tried to produce oil-free compressed air by employing relatively complex and often even interconnected compressor-, filter- and dryer-based technologies. In many cases, this can only be achieved partially reliably.
Horstmann also never found a satisfactory solution, in particular not after having acquired new, even more powerful cutting plants. Until the beginning of the year 2008, when they discovered a new catalysis method to produce absolutely oil-free compressed air, developed by the German compressed-air specialist BEKO TECHNOLOGIES GmbH. The method called "BEKOKAT" opens the way towards absolutely oil-free compressed air with a technological approach which is completely different from all previous solutions: by means of catalysis.
Total oxidation of hydrocarbons
Basically, the BEKOKAT system realizes a total oxidation of hydrocarbons and thus absolutely oilfree compressed air. And this in a concentrated, comprehensive process step subsequent to compression. In this manner, the full oil removal from the compressed air is implemented in only one plant component. This component functions independently of the ambient conditions, the oil input concentration and the relative humidity of the compressed air.
BEKOKAT addresses all contaminations in the compressed air supplied by the compressor. These are usually lubricants, oils, sulphur dioxide, carbon monoxide, nitrogen gases etc. They exist in gas-, vapour and aerosol form. With the BEKOKAT method, such air components are fully converted into carbon dioxide and water.
This water can be introduced directly without reservation and without further environmental-protection measures into the wastewater system. Even the condensate accumulating during the cooling-down of the compressed air is absolutely oil-free thanks to the catalysis method, and can also flow into the sewerage system without being processed. Currently, no other method achieves this total oxidation and an absolutely residue-free procedure.
In the BEKOKAT, granular material serves as the catalytic converter, which is heated up to an operating temperature of approx. 150 °C by means of heating elements. In the catalytic converter, the oil molecules are broken down until only one carbon atom remains. In the final catalysis phase, the oil molecules are oxidized down to H2O and CO2.
It is essential that the hydrocarbon chains, meaning the oil molecules, can be "cracked" at any point. They are always broken down until only carbon dioxide and hydrogen remain. Therefore, the hydrocarbon chains from oil-free and oil-lubricated compressors varying in length pose no problem at all to BEKOKAT.
It is not always well-known that the activated carbon filters which are otherwise often employed are not able to adsorb polar compounds such as alkenes, alcohols, glycols or ketones. In contrast, the BEKOKAT system completely removes also these substances from compressed air. In the further course of the BEKOKAT process, the purified compressed air is cooled down in a heat exchanger to approx. 10 to 15 °C above the inlet temperature and is available for the respective application.
With the BEKOKAT method, it is for the first time possible to constantly achieve absolutely oil-free compressed air with a barely measurable maximum residual-oil content of 0.003 milligram per cubic meter of compressed air. This is the quality required in the most demanding fields of medicine, pharmaceutics, food processing and food packaging.
The enormously long service life of the special granular material of the BEKOKAT is also extremely advantageous as far as profitability is concerned: it only needs to be replaced after a good 20,000 hours. Compared to that, the life of an activated carbon filter is already depleted after approximately 500 operating hours, even under perfect operating conditions.
Since early summer 2008, the BEKOKAT system is, without failure, in operation around the clock at the Horstmann metal-processing company. In addition, the company has a clear environmental conscience, because since the employment of the BEKOKAT, they can introduce the condensed water from the compressed-air system without any problems and without expensive processing directly into the sewer.
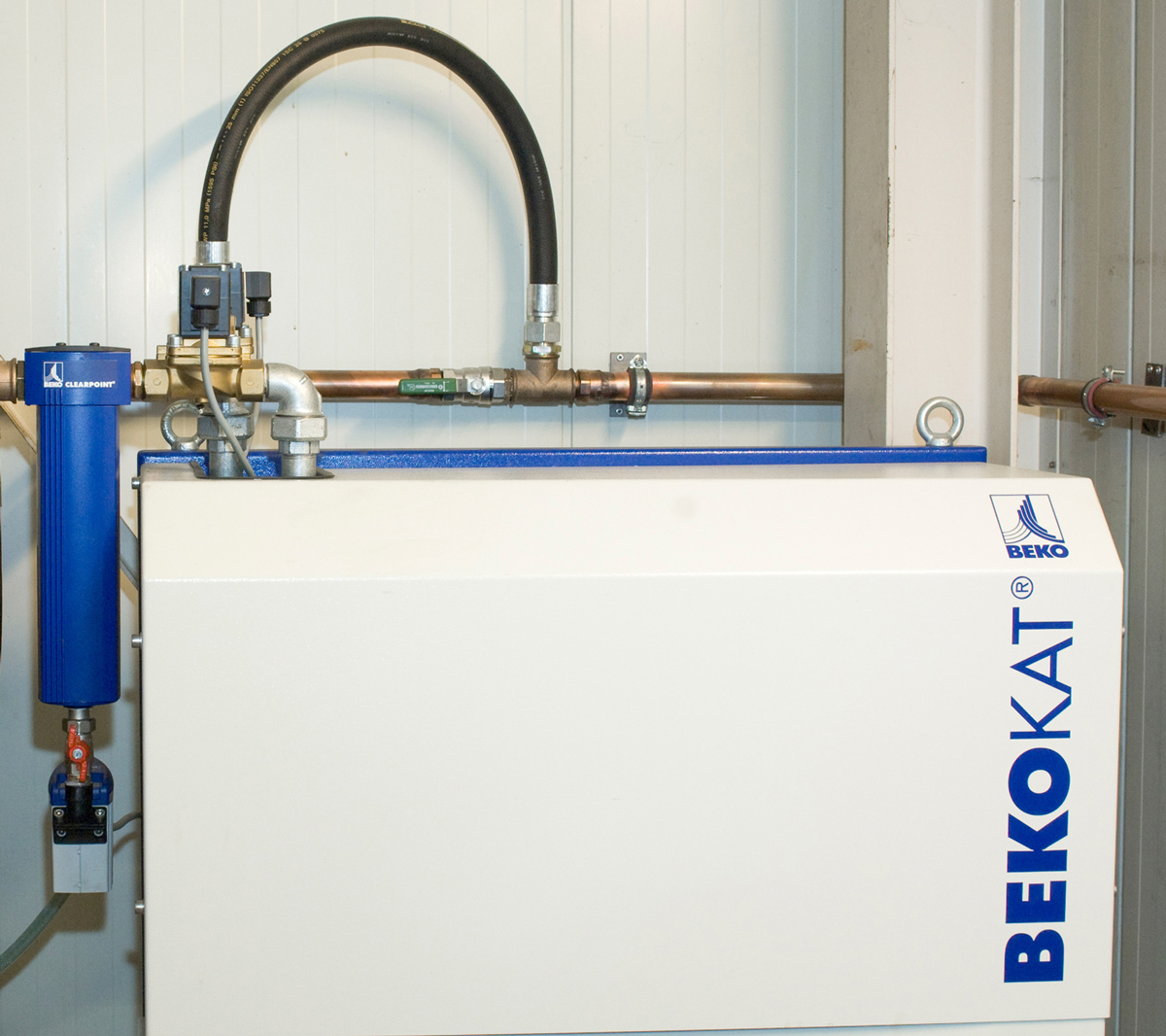
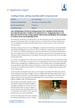