Trattamento dell’aria compressa nella produzione del cristallo
Settore: | produzione di vetro |
Cliente/luogo/anno: | Stölzle Lausitz, Weißwasser (Germania), 2013 |
Uso dell’aria compressa: | In produzione |
Prodotti installati: | DRYPOINT RA, BEKOMAT |
Brillantezza celestiale e fuoco infernale. Solo di rado questi due elementi si vedono così vicini l’uno all’altro, come nel caso del traino del vetro, ovvero la produzione meccanica di pregiato vetro da tavola. Stölzle Lausitz GmbH con sede nella città sassone di Weisswasser è una delle vetrerie leader in Germania. Nei suoi processi di produzione, l'aria compressa secca è la fonte di energia più importante.
Con oltre 1100 gradi Celsius, le fiamme soffiano fuori dagli ugelli delle potenti macchine negli enormi padiglioni dello stabilimento di Stölzle. Ci si immaginano quasi dei draghi divenuti acciaio e quindi, da visitatori, ci si tiene a distanza, con un certo rispetto. Se non fosse per la curiosità di sapere cosa brilla e scintilla dietro le fauci di questi mostri: il vetro cristallino più puro, dall'accecante luminosità. Che dà vita a pregiati bicchieri da vino e prosecco. Una bellezza senza trucco, nata dal fuoco.
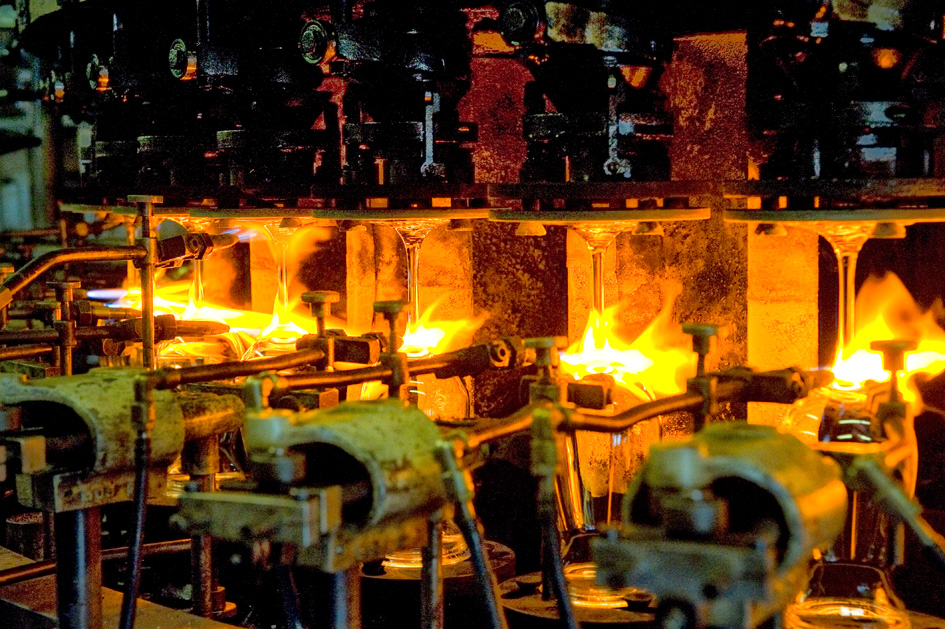
Vista la genesi ricca di fiamme, lo slogan aziendale “born in fire” qui diventa una vera esperienza sensoriale. Grazie alla procedura di traino oppure la tecnica di saldatura utilizzata, presso Stölzle Lausitz, nascono bicchieri che, grazie al loro passaggio continuo, senza interruzioni da manico a calice, e all’eccezionale ripartizione del vetro, somigliano moltissimo al caratteristico vetro soffiato a bocca. Inoltre, in questo caso ci sono i vantaggi della resistenza alla rottura e alla lavastoviglie, quindi un fantastico rapporto qualità-prezzo.
I bicchieri si adattano perfettamente al carattere delle diverse bevande: vino, vino frizzante, super alcolici e cocktail. Gli acquirenti sono soprattutto il settore dell’ospitalità, gastronomia, settore delle bevande nonché viticoltori esigenti. Ogni anno Stölzle Lausitz distribuisce fino a 35 milioni di bicchieri in oltre 45 paesi del mondo.
Ventilazione regolare con aria compresa
L’arte della creazione e della finitura del vetro nella Lusazia è curata e sviluppata da oltre 500 anni. La prima menzione storica di una vetreria risale all'anno 1433. Nel 1930, la Lusazia divenne la regione d’Europa con la maggiore produzione di vetro e la “Glashüttenwerke Weißwasser AG”, antecedente all’attuale Stölzle Lausitz GmbH, la più grande produttrice di calici.
Fondamentale per il processo produttivo è una costante ventilazione dei draghi sputafuoco con aria compressa secca. Infatti, qui l’aria compressa è lo strumento di produzione più importante e fonte di energia principale, poiché viene usata per gestire gli impianti e per innumerevoli cilindri ad aria compressa nonché valvole di regolazione. Decisiva è l’alimentazione costante e affidabilmente essiccata di aria compressa. Un’umidità troppo elevata, in pochissimo tempo causerebbe emulsioni nelle valvole delle macchine - ovvero la ostruzioni, conseguenti nello stato di fermo e in interruzioni della produzione.
Un altro tallone di Achille del trattamento dell'aria compressa da Stölzle: gli essiccatori a freddo. Infatti, c’era da combattere con un particolare problema. Anche in questo caso, erano implicate temperatura straordinariamente elevate.
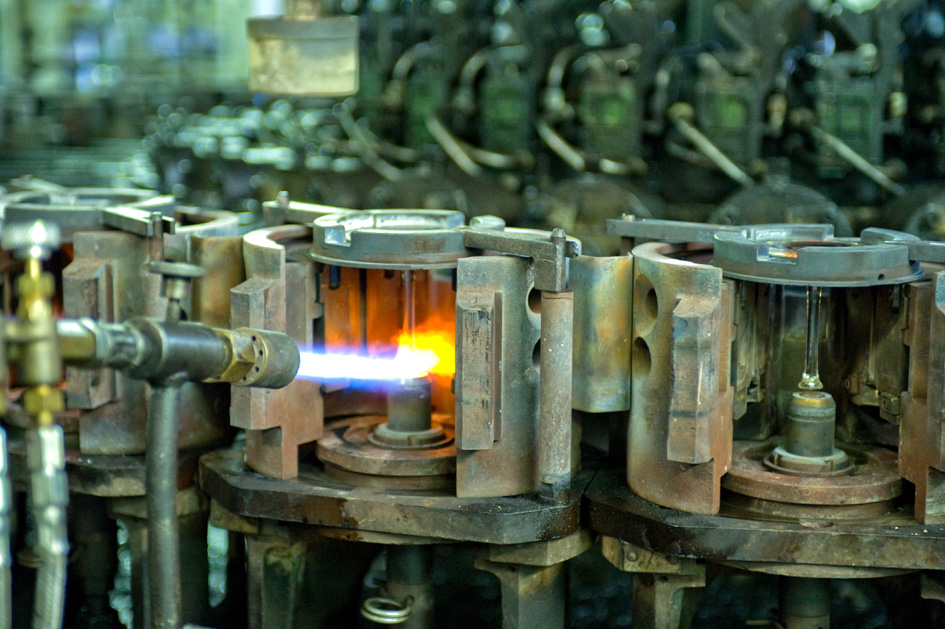
Tallone d’Achille: essiccazione a freddo
Uno dei compressori impiegati nello stabilimento produceva, per via del tipo di costruzione, aria compressa estremamente calda. L’essiccatore a freddo a valle di questo compressore sempre più spesso non riusciva a contrastare l’aria compressa ventilata che spesso arrivava a 63 gradi. Soprattutto i mesi estivi caldi erano sul filo del rasoio. La temperatura di uscita dietro l’essiccatore a freddo sovraccaricato era spesso più elevata rispetto a quanto potesse sostenere l’ulteriore gestione dell’aria compressa.
Essa si caratterizzava con un ampio sistema di prestazione con postazioni con compressori fino ai punti di collaudo nei padiglioni di produzione. Spesso anche mediante ampi percorsi all'esterno e nei padiglioni dello stabilimento attraverso i sotterranei, in cui la rete di linee si ramificava ulteriormente. Dal compressore fino alla destinazione, l’aria compressa attraversa quindi numerose zone di temperatura e quindi percorsi che generano condensa. Il rischio di un’aria compressa che giungesse alla macchine ancora umida aumentava a vista d’occhio.
Allora, quale essiccatore a freddo sarebbe stato in grado di resistere alle elevate temperature dell'aria compressa di questo bollente compressore?
La soluzione dall’esperienza
La vetreria sassone trovò una soluzione con il fornitore tedesco di sistemi d’aria compressa BEKO TECHNOLOGIES GmbH. Con la sua tecnica, presso numerosi punti dello stabilimento già da anni si stavano facendo ottime esperienze. Così, per esempio, con i separatori olio-acqua ÖWAMAT, con filtri per aria compressa CLEARPOINT e scaricatori della condensa BEKOMAT.
Alla bollente situazione dell'essiccazione a freddo presso Stölzle, lo specialista dell’aria compressa di Neuss sul Reno diede una risposta: l’essiccatore di aria compressa a freddo DRYPOINT RA.
Nell’essiccatore a freddo DRYPOINT RA l'essiccazione dell’aria compressa avviene mediante uno scambio di calore ottimale, attraverso un processo di contro flusso per tutto il percorso. L’aria fluisce in un movimento all’ingiù, senza inutili deviazioni. Questo scambiatore di calore in Counter Flow di grandi dimensioni, composto tra l'altro da uno scambiatore di calore aria/aria e uno aria/refrigerante, raffredda l'aria compressa fino a una temperatura di tre, mentre le dimensioni dello scambiatore di calore non solo favoriscono un raffreddamento efficiente, ma riducono al minimo assoluto anche la resistenza al flusso.
Sin dall’inizio, il nuovo sistema di essiccazione fece capire di essere all’altezza senza alcun problema delle elevate temperature di ingresso dell’aria compressa. Persino le calde giornate estive subito dopo l’installazione non posero limite alla prestazione di essiccazione. Tuttavia la prestazione non era tutto, anche l’economicità era decisiva.
Un punto di vista eccezionalmente intelligente sulla cosa. Infatti, non sono solamente i costi dell’investimento a determinare il conto dell’economicità per gli essiccatori a freddo, bensì anche i costi d’esercizio. Per un periodo di funzionamento pari a cinque anni, solamente dal 20 al 30 percento dei costi complessivi ricadono sul solo investimento per acquisto e installazione. Dal 70 all’80 percento, si suddividono al contrario sui costi di esercizio correnti.
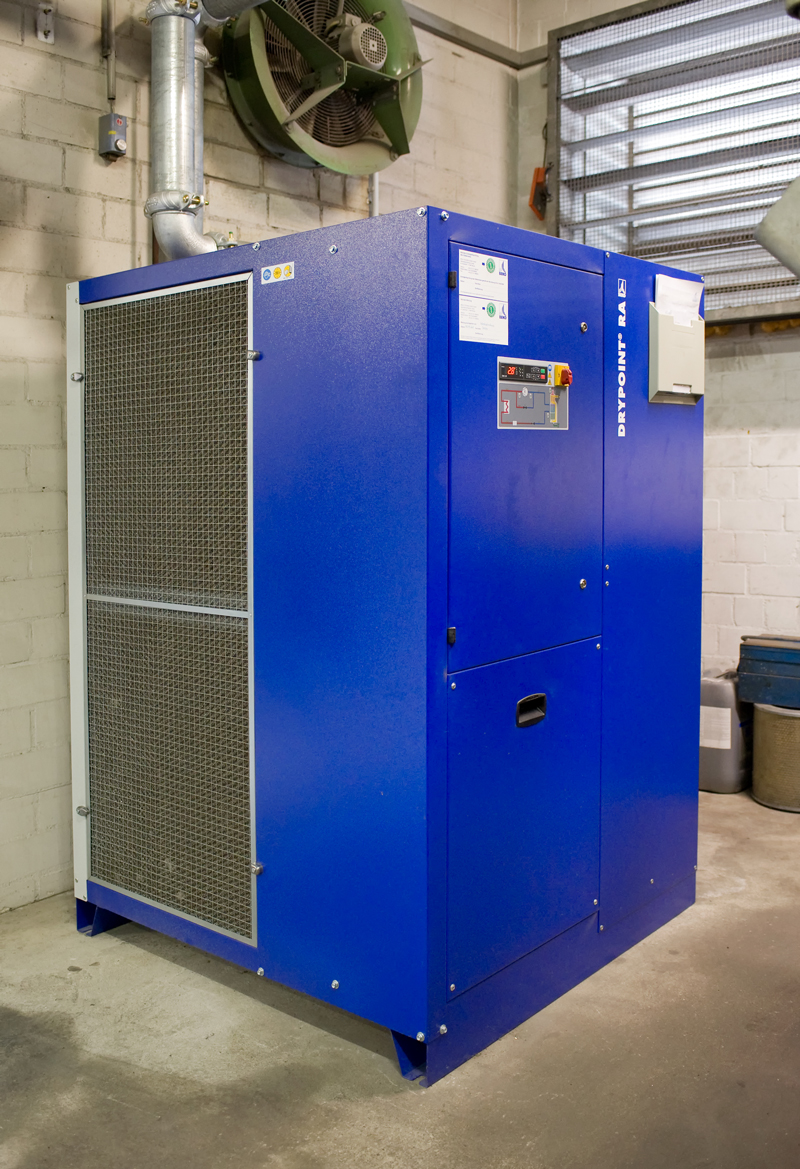
Costi di esercizio ridotti della metà
Nel caso del DRYPOINT RA di BEKO TECHNOLOGIES, questi possono essere ridotti fino a circa la metà. Per Stölzle Lausitz, il conteggio del ROI evidenziava che il nuovo essiccatore a freddo sarebbe stato ammortizzato entro solo circa sei mesi. Un argomento convincente soprattutto per gli esperti in economia aziendale.
Al DRYPOINT RA è riuscita questa combinazione di efficacia ed efficienza grazie a una costruzione particolarmente rifinita. Sostanziali elementi sono la struttura verticale dello scambiatore di calore, che consente un fluire della condensa dall’alto verso il basso, un antiappannante per la sicura separazione e un vano di stabilizzazione di grande volume, che impedisce il trascinamento della condensa. L’apparecchio è particolarmente economico, soprattutto poiché impedisce rinvii controcorrente dell'aria compressa e inutili resistenze al flusso. Un punto di rugiada costantemente più basso, quasi il 99 percento di separazione delle goccioline, nessuna perdita di aria compressa, ridotto impegno di manutenzione e bassi costi di esercizio sono altri temi vantaggiosi.
Inoltre, nell'essiccatore a freddo DRYPOINT è integrato lo scarico della condensa. Esso dispone infatti di serie di uno scaricatore di condensa BEKOMAT. Un comando del sistema, oltre al controllo della funzione dell'essiccatore, si occupa anche di gestire e monitorare lo scaricatore - inclusa la visualizzazione di eventuali messaggi di errore.
Aria compressa e raggi laser
Inoltre, per quanto riguarda il traino dei bicchieri di Stölzle, non c’è solo la fiamma del fuoco, bensì anche altra luce. Per essere precisi, quella del laser. La forza raccolta dei raggi laser viene usata per tagliare esattamente il vetro fino al decimo di millimetro. E anche in questo caso - come in tanti altri punti dello stabilimento - entra in gioco la tecnologia di BEKO TECHNOLOGIES. In questo speciale caso, sotto forma di essiccatori a membrana nonché filtri fine e microfiltri. Questi raffreddano e puliscono l’aria compressa necessaria a raffreddare lo specchio di rinvio del laser.
Prima che venisse usata la potente combinazione di essiccatore e filtri, lo specchio veniva raffreddato con l’azoto fornito. Una procedura estremamente costosa, tanto da raggiungere quasi 700 euro a settimana. Grazie alla nuova tecnica, anche questa voce di costo del trattamento dell'aria compressa presso Stölzle Lausitz è stata depennata del tutto.
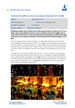