Trattamento dell’aria compressa come concept di catena di processo
Settore: | tecnologia di azionamento |
Cliente/luogo/anno: | Flender, Mussum (Germania), 2009 |
Uso dell’aria compressa: | Aria di processo, aria di tenuta, tecnologia della condensa |
Prodotti installati: | BEKOSPLIT, CLEARPOINT, DRYPOINT RA |
Laddove deve essere soddisfatta una serie di requisiti, le soluzioni singole raramente portano a risultati soddisfacenti. L’azienda A. Friedr. Flender AG, uno dei principali fornitori mondiali di tecnologie di azionamento meccaniche ed elettriche, si affida a un concetto dinamico con catena di processo. Ciò vale anche per il trattamento dell'aria compressa in cui vengono affrontate sia sfide tecniche che qualitative e ambientali.
Nel sito produttivo Flender a Mussum, il secondo sito al mondo per grandezza di giunti industriali per momenti torcenti da 10 a 10.000.000 Nm, su tre turni e per 365 giorni all’anno vengono prodotti giunti altamente elastici, giunti resistenti alla torsione - ovvero giunti dentati e giunti a disco in acciaio - nonché giunti speciali per turbine eoliche e il settore ferroviario. Una gamma veramente sorprendente a cui si dedicano circa 350 dipendenti dei complessivi 6.300 di tutto il gruppo aziendale Flender.
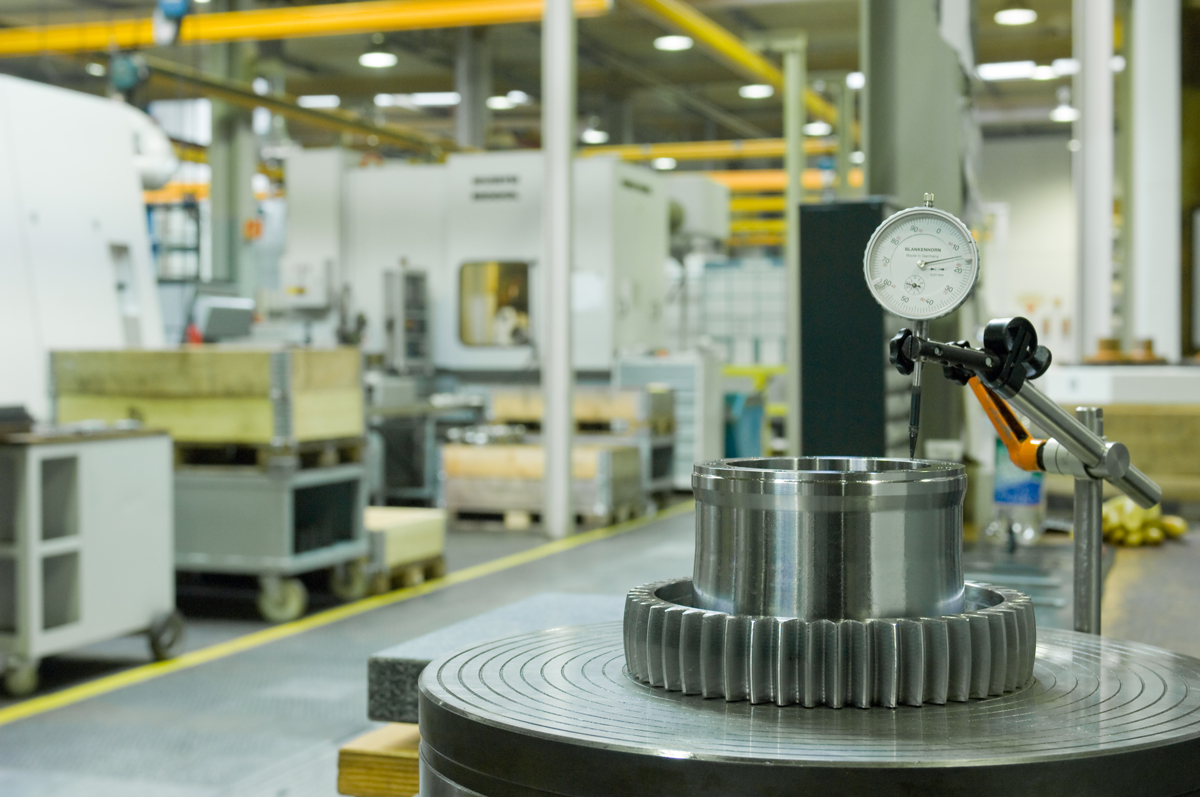
Ripartizione degli incarichi e responsabilità totale
Mussum, come stabilimento di produzione di giunti, rappresenta in pratica un modulo del gruppo “propulsore” Flender, in cui le attività sono strettamente collegate a quelle dello stabilimento principale a Bocholt nonché di quello per il montaggio di ingranaggi a Voerde-Friedrichsfeld. Gli stabilimenti lavorano secondo un concept globale armonioso, poiché tutte le aree e le attività del gruppo vengono considerate e svolte in modo orientato all’obiettivo. Il tutto con grande successo, come dimostra la lunga storia aziendale. Non a caso nel 2005 Siemens AG ha rilevato Flender Holding e completato la sua attività entrando nel settore della tecnologia di azionamento industriale.
Presso Siemens AG e da Flender Holding AG, si pianifica e si agisce all’interno di una catena di processi coerente. Ciò non è solamente importante per il risultato, bensì anche per ciò che accade prima e come. Si tratta di un processo efficiente, logico, mirato? Ma soprattutto: per cosa ci si assume la responsabilità? Si è responsabili dal punto di vista degli aspetti relativi alla qualità, alle riflessioni economiche e ovviamente per l’importanza giuridico-etica - per esempio per ciò che concerne la tutela dell’ambiente e delle risorse naturali.
Buoni propositi e risultati concreti
Come dimostrano gli esempi concreti presso gli stabilimenti produttivi tedeschi della Flender AG, non si tratta solamente di un modo di dire. Un esempio estremamente chiaro è proprio il trattamento dell'aria compressa presso lo stabilimento di produzione di giunti a Mussum.
Qui, la maggior parte dell'aria compressa è necessaria per alimentare gli apparecchi di misura delle coordinate presso i macchinari di produzione con aria di pilotaggio. A questo segue immediatamente il caricamento dei motori di azionamento diretto, che quindi sono protetti dalla penetrazione di umidità. Un ulteriore elevato fabbisogno di pressione si origina per l’impiego dei macchinari di sbavatura, presso gli impianti di pulizia per il soffiaggio di semilavorati nonché in corrispondenza di sistemi di spruzzaggio del colore e lo stivaggio automatico nell’area spedizione.
La stessa infrastruttura dello stabilimento di produzione dei giunti punta sulla fonte di energia aria compressa. Per esempio, per l’allestimento di lucernari e botole di aerazione nonché per il comando di sistemi di ventilazione. Mentre alcune di queste applicazioni non pongono alcun requisito particolare in quanto a qualità dell'aria compressa, altre sono molto sensibili da questo punto di vista - in particolare gli apparecchi di misura e i dispositivi di verniciatura. Mentre i primi non vogliono innanzitutto la presenza di olio residuo nell'aria compressa, nel reparto verniciatura è assolutamente vietata la presenza di umidità. Infatti, qui darebbe origine a delle piccole bolle durante la stesura del colore sull’alloggiamento del giunto - un vero “errore estetico”, che nemmeno gli acquirenti di tecniche industriale comprovate amano tollerare.
Complessi requisiti sulla qualità dell’aria compressa
Quindi, è necessaria sia un’aria compressa praticamente priva di oli che assolutamente secca al fine di soddisfare gli elevati standard di qualità nella produzione dei giunti. Tuttavia non è sufficiente. Da Flender, si hanno grandi obiettivi “interni” in relazione agli obblighi imposti. In tale ambito ci si orienta al gruppo madre Siemens, già certificato secondo la nuova norma di gestione ambientale ISO 14001. Vi rientra anche lo smaltimento migliore possibile della condensa originatasi dal trattamento dell'aria compressa.
Ciò di cui si aveva bisogno era un concept personalizzato che comprendesse tutte le sfide e che le risolvesse in modo totale - con competenza sistemica. Dopo un intenso processo di valutazione e selezione, da Flender si è deciso di scegliere un offerte di sistemi che poteva distinguersi già da tempo con i propri prodotti e le soluzioni a Mussum: lo specialista tedesco dell'aria complessa BEKO TECHNOLOGIES da Neuss, sul Reno.
Insieme a un partner locale specializzato sulla tecnologia dei compressori, gli specialisti di BEKO TECHNOLOGIES hanno realizzato un concept globale sorprendente. Dalla compressione all'essiccazione, dal filtraggio al trattamento della condensa fino al controllo dell’olio residuo e alla costruzione delle tubazioni, tutti gli aspetti del trattamento dell’aria compressa sono stati intrecciati in modo coerente.
L'impianto di scissione dell'emulsione protegge l'ambiente
Il "gioiello" della costellazione e allo stesso tempo la prova della serietà di Flender AG riguardo alla protezione dell'ambiente è l'impianto di separazione dell'emulsione BEKOSPLIT. Soddisfa senza sforzo anche i requisiti estremamente elevati della nuova norma di gestione ambientale ISO 14001.
Questo sistema di separazione per i condensati dell'aria compressa, che è il più venduto in Germania, viene utilizzato dove le particelle di olio più piccole sono finemente distribuite nella fase dell'acqua, in modo che la separazione puramente fisica per gravità, per esempio con separatori di liquidi leggeri o separatori a coalescenza, non è sufficiente. Il sistema BEKOSPLIT, d'altra parte, offre una tecnica di trattamento affidabile per le acque reflue industriali emulsionate contenenti olio, rimuovendo i contaminanti organici insolubili in acqua, come gli oli, e le impurità solide dalle acque reflue attraverso l'aggiunta di un minerale naturale di argilla. Allo stesso tempo, i metalli pesanti esistenti e altre particelle di sporco vengono adsorbiti in modo affidabile. L'acqua di scarico rimanente, purificata, può essere scaricata nel sistema fognario senza problemi.
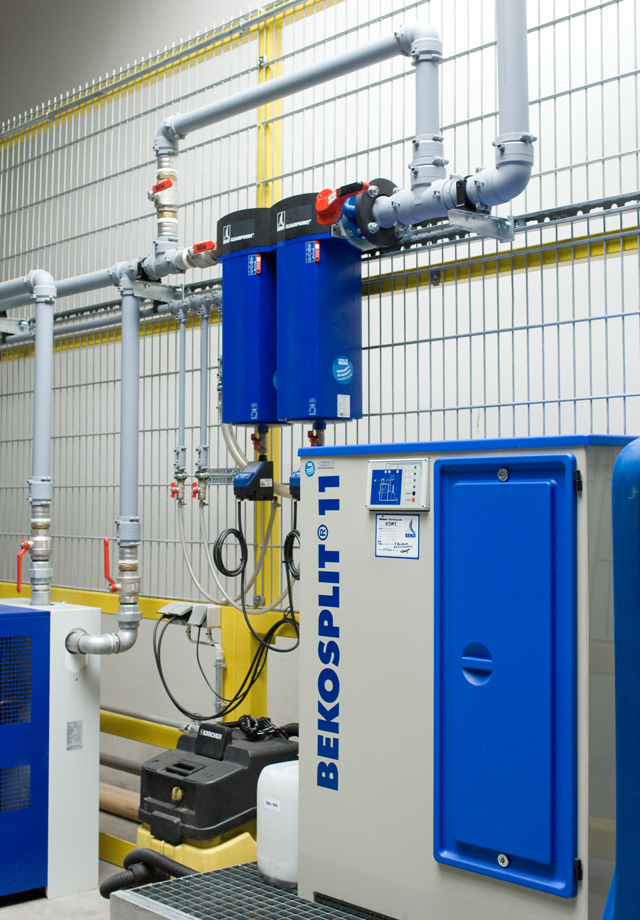
Combinato con il sistema fin dall'inizio
Mentre la procedura BEKOSPLIT è sinonimo di prestazione massima dal punto di vista tecnico dell’aria compressa alla “fine dello smaltimento” della catena di sistema, nella “fase iniziale dello smaltimento” più componenti funzionano insieme. L’aria compressa viene innanzitutto guidata mediante una caldaia da 3000 litri in cui è già stata separata una parte dell’umidità presente.
A essa seguono tre essiccatori a freddo DRYPOINT RA in parallelo di BEKO TECHNOLOGIES. In pratica, rappresentano una triplice soluzione al 50%. Ciascuno dei tre apparecchi è in grado, da solo, di generare la prestazione di essiccazione richiesta dell’impianto Flender. Grazie all’attivazione in parallelo di tutti i tre gli essiccatori a freddo, viene fornita quindi una prestazione al 150%. Ciò ha il vantaggio che, in qualunque momento, dal sistema può essere rimosso un intero dispositivo, magari a scopo di manutenzione, senza compromettere la prestazione di essiccazione necessaria. Persino il guasto totale di un essiccatore non provoca alcuna conseguenza sulla qualità dell’aria compressa.
La condensa originatasi nell’essiccatore viene separata evitando perdite di aria compressa grazie allo scaricatore di condensa BEKOMAT a regolazione di livello e avviata al descritto impianti di piroscissione BEKOSPLIT.
L’aria compressa essiccata viene poi avviata a un filtro aria compressa CLEARPOINT ottimizzato dal punto di vista del flusso. Con questi, BEKO TECHNOLOGIES ha implementato una tecnica di filtraggio particolarmente efficiente dal punto di vista energetico e quindi vantaggioso all’interno del sistema ad aria compressa. L’ultimo punto di verifica prima che l’aria compressa esca dal padiglione dei compressori è un sistema di monitoraggio dell’olio residuo anch’esso installato da BEKO TECHNOLOGIES.
In fin dei conti, Flender, presso i siti di produzione a Mussum, ha installato una catena di processo che si dimostra completamente coerente e perfettamente adattata al trattamento dell’aria compressa.
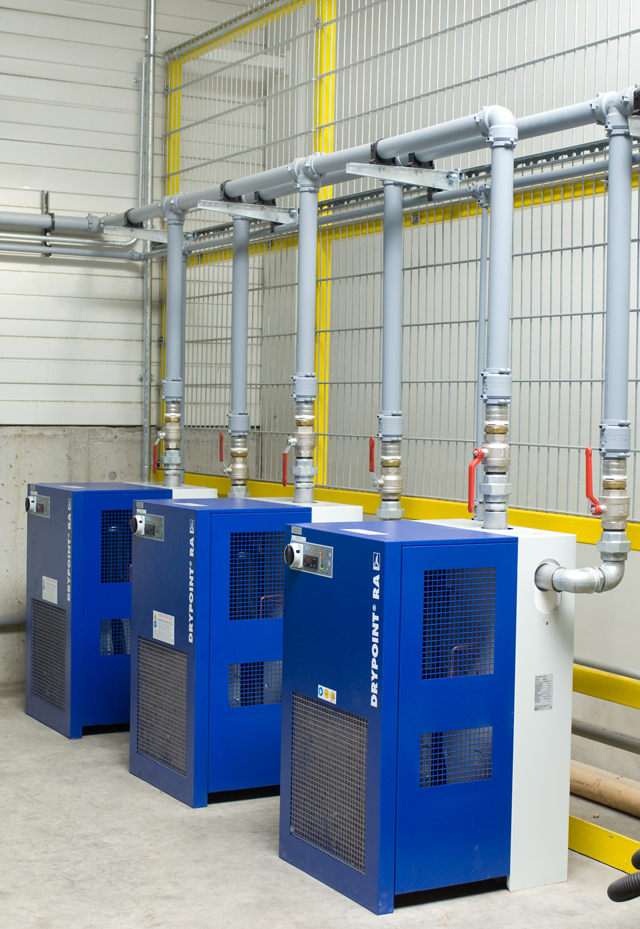
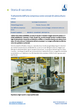