Essiccazione dell'aria compressa nel trattamento del gesso
Settore: | materiali da costruzione |
Cliente/luogo/anno: | Remondis, Lünen (Germania), 2013 |
Uso dell’aria compressa: | In produzione |
Prodotti installati: | EVERDRY |
L’umidità è il grande nemico dei 432 tubi di filtraggio in tessuto del forno a letto fluido 7 della Remondis Production GmbH nello stabilimento Lippe, nella città di Lünen in Vestfalia. Questo forno serve a calcinare il gesso - un materiale eccezionalmente idrofilo per natura. Con un essiccatore ad adsorbimento con generazione a caldo per l’aria compressa di pulizia dei filtri in tessuto si impedisce che acqua e polvere di gesso si accumulino nel tessuto di filtraggio. In tale ambito, si è pensato a una soluzione del tutto diversa.
Remondis è una delle aziende più grandi al mondo per quanto riguarda l’economia delle acque e di ciclo con oltre 500 sedi in 26 paesi su tre continenti. Le competenze chiave del gruppo sono la fornitura di acqua e il suo trattamento, l’acquisizione di materie prime dai rifiuti, lo sviluppo di prodotti riciclati e la messa a disposizione di fonti energetiche alternative. In un altro campo d’attività, il trattamento del gesso avviene dalla pulizia dei gas di scarico e da processi industriali e si trasforma in pregiati leganti in gesso.
A tal proposito, Remondis movimenta enormi quantità di materiale che, come materie grezze secondarie, possono essere riavviate al ciclo economico. Nella sola sede di Remondis a Lünen lavorano ben 1200 dipendenti. Con una superficie di 230 ettari, si tratta del più grande centro di economia di ciclo industriale d’Europa. Al centro, si trova il recupero di materie prime, la produzione di prodotti di base, prodotti speciali e beni industriali nonché la generazione di energia.
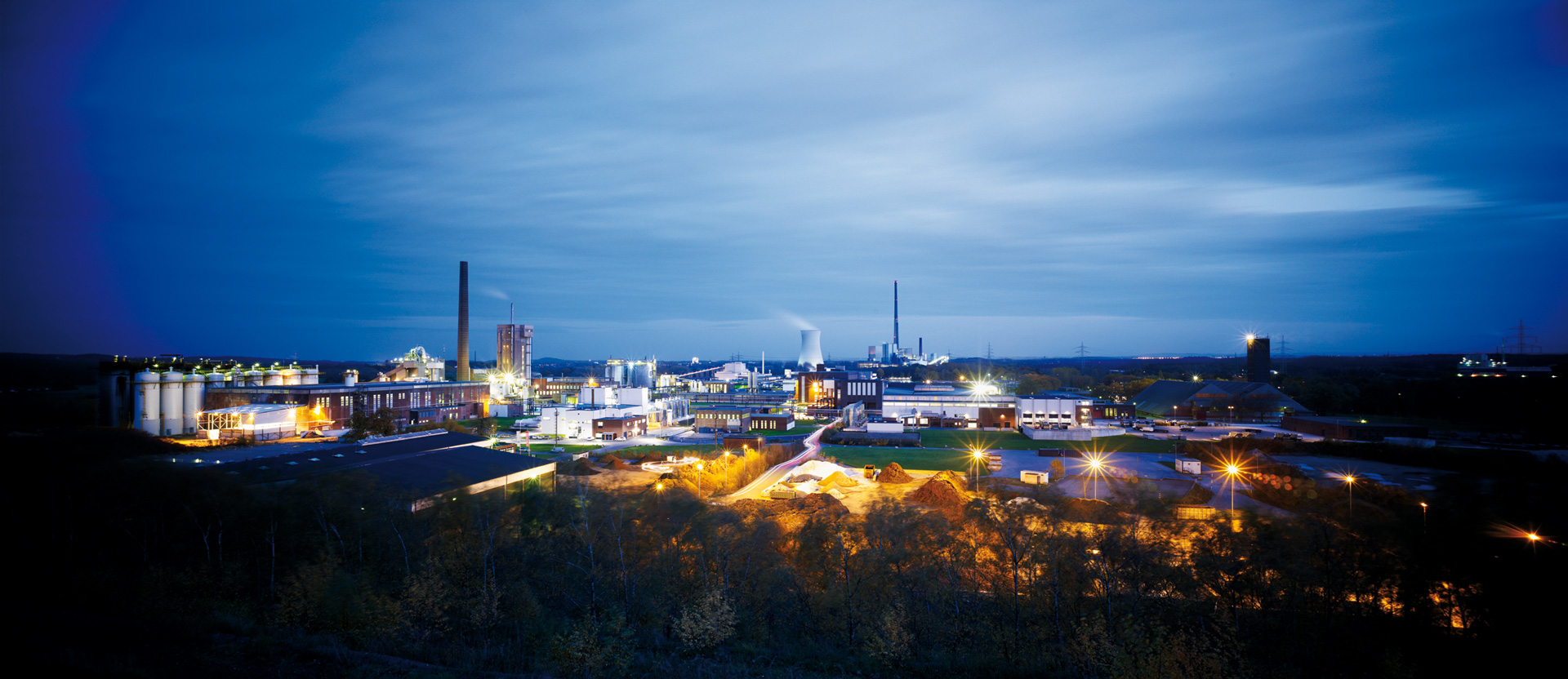
Uno degli incarichi principali è il trattamento annuale di circa 280.000 tonnellate di gesso, che si accumulano nelle centrali a carbone vicine come prodotti secondari. Esse si generano negli impianti di desolforazione dei gas di scarico (REA) delle centrali elettriche, riscaldate con carburanti fossili.
A Lünen, Remondis trasforma questo gesso REA in pregiati additivi e leganti che, di nuovo, con il nome commerciale di RADDiBIN - vengono avviati all’industria del gesso come materie prime per diverse applicazioni. Da questi nascono, per esempio, solette liquide, calcestruzzo poroso, concime, cemento oppure materiali per l’odontoiatria.
Nello stabilimento Lippe, attualmente nascono due tipi di prodotto dal gesso REA trattato. Uno è il semiidrato ALPHA, che presenta una particolare robustezza dopo l’aggiunta di acqua. L’altro è l’anidride. Viene bruciata a temperature molto elevate e si adatta in modo particolare alla produzione di malte per massetti.
Per quanto riguarda la produzione di anidride, questa non sarebbe possibile senza il forno 7. Questo “mostro”, alto oltre 50 metri, è il vero e proprio punto di ignizione del tutto. Al suo interno, quotidianamente circa 1000 tonnellate di gesso REA, a una temperatura di oltre 800 gradi Celsius, vivono la loro metamorfosi in una materia prima pregiata.
Tanta attenzione alla qualità
Il cosiddetto forno di calcinazione funziona secondo il principio del letto fluido circolante. Costruito originariamente per la calcinazione dell’idrossido di alluminio, durante la ristrutturazione dello stabilimento Lippe nel 1989 è stato modificato, e da quel momento si occupa della calcinazione del gesso.
Per quanto riguarda la calcinazione nel letto fluido, il materiale a grana fine viene trasportato in un gas caldo con elevata velocità e, al contempo, disidratato in anidride con l’energia dei gas caldi. Tale processo viene gestito mediante un’esclusiva tecnica impiantistica, tanto che tutte le particelle vengono esposte contemporaneamente allo stesso tempo di ritenzione e alle temperature di processo. In questo modo si riesce a realizzare in grande scala tecnica una qualità che corrisponde alle caratteristiche di una qualità di laboratorio in piccola scala.
Per il forno 7, le oscillazioni di qualità non sono un problema. Infatti, la questione è stata conclusa dal punto di vista della tecnica procedurale. Lo si può ben dire. Infatti, uno dei punti nevralgici di questo gigante di fuoco sono i filtri in tessuto. Se diventano umidi, anche per la produzione e la qualità “si suda freddo”.
L’umidità che preoccupa
Il rischio della penetrazione di umidità nel tessuto si presenta soprattutto durante la pulizia dei filtri in tessuto con aria compressa. In tale ambito, i tessuto vengono soffiati con forti colpi di pressione, per espellere il gesso che aderisce. Se l’aria compressa da usare non è assolutamente secca, per via degli impulsi a pressione nel tessuto viene soffiata anche l’umidità. Il colpo di aria compressa comporta inoltre un raffreddamento repentino con contemporaneo non raggiungimento del punto di rugiada.
L’umidità reagisce con i residui di gesso nel tessuto e distacca il gesso. Di seguito, il tessuto indurisce e infine si rompe. Un processo strisciante, che tuttavia accelera immensamente l’invecchiamento dei tessuti. È proprio qui che Remondis ha visto potenziale di risparmio sui costi d’esercizio. Alla base di un’economicità chiaramente maggiore doveva esserci l’integrazione del trattamento dell’aria compressa con una potente essiccazione di quest’ultima.
La durata utile dei filtri in tessuto puliti con aria compressa non perfettamente secca nel forno 7 era, sino a quel momento, di due anni. Se, invece, si fosse effettuata un'essiccazione, la durata utile dei tessuti si sarebbe allungata fino a circa tre anni, secondo i calcoli. Per i 432 filtri si trattava, al pezzo, di circa 100 euro, quindi un enorme risparmio sui costi. Dopo le approfondite pianificazioni, all’inizio del 2009 Remondis aprì il bando per l’installazione di un essiccatore ad adsorbimento con rigenerazione a freddo nell’impianto d’aria compressa.
I più caldi suggerimenti
Contrariamente all’appalto indetto e a tutti gli altri offerenti, BEKO TECHNOLOGIES GmbH suggerì un essiccatore ad aria compressa con generazione a caldo. Per grosse portate volumetriche, l’essiccazione ad adsorbimento è senza dubbio la procedura industriale più comune per l’essiccazione dell'aria compressa a punti di rugiada di meno 20 gradi Celsius e oltre. La dimensione concreta in questo caso applicativo - da Remondis fino a 1.500 metri cubi all’ora - portò a una decisione sensata dal punto di vista economico tra dispositivo a generazione a freddo e a caldo.
Essiccatori ad adsorbimento con rigenerazione a freddo
Gli essiccatori ad adsorbimento con rigenerazione a freddo funzionano con cicli di caricamento brevi. Grazie al caricamento ridotto del materiale essiccante, la rigenerazione avviene senza aggiuntiva immissione di energia termica. L’umidità viene eliminata mediante un flusso parziale d’aria ventilata fresca depressurizzato.
L'energia elettrica in un essiccatore ad adsorbimento con rigenerazione a freddo è necessaria solamente per la gestione e la commutazione delle valvole. La potenza elettrica assorbita necessaria è quindi affidabilmente ridotta. Tuttavia: i costi di investimento da ridotti a medi si contrappongono ai costi di consumo per circa il 15 percento dell'aria compressa già trattata, in relazione alle condizioni a pieno carico con 7 bar.
I costi dovuti alla perdita di aria di lavaggio si sommano rapidamente in totali inaccettabili. Per Remondis, è stato questo l'argomento decisivo a decidere di acquistare un dispositivo con generazione a caldo.
Essiccatori ad adsorbimento con rigenerazione a caldo
In caso di impianti con desorbimento ad aria ventilata, esistono diverse forme costruttive. Un aspetto comune a tutte le procedure è che, per rimuovere l’umidità adsorbita, non si usa aria di sistema trattata, bensì aria ambiente riscaldata. Le differenze sono tuttavia nei metodi di raffreddamento del materiale essiccante.
Nella versione classica, per raffreddare il materiale essiccante si impiega solamente un flusso parziale depressurizzato di aria compressa trattata. Ovviamente, in questo caso si origina una quantità di preziosa aria compressa per scopi diversi da quelli previsti. Anche se essa si aggira solo, di media, dal due al tre percento, l’aspetto dell’economicità resta tuttavia un problema.
L’alternativa più economica sono gli essiccatori ad adsorbimento “Zero Purge”, che lavorano senza alcun consumo di aria compressa trattata. In questi, il desorbimento avviene, esattamente come nella procedura classica, grazie ad aria ambiente riscaldata, che una ventola conduce attraverso il materiale adsorbente. Il finale raffreddamento del materiale essiccante riscaldato, avviene mediante aria ambiente.
L’economicità intrappolata nel forno
Dopo un'accurata analisi delle condizioni ambientali e di esercizio presso il forno 7, gli specialisti del trattamento e di sistema di BEKO TECHNOLOGIES si sono concentrati sull'essiccatore ad adsorbimento con generazione di calore del tipo EVERDRY FRA-V della vasta gamma di prodotti della casa. Gli impianti della serie FRA-V non necessitano di aria compressa né per il processo di desorbimento, né per il finale raffreddamento del materiale essiccante (Zero Purge).
In fase di desorbimento, il soffiatore di rigenerazione funziona sotto pressione. Mentre in un contenitore di adsorbimento avviene l'essiccazione dell'aria, viene rigenerato il contenitore di adsorbimento prima saturo di umidità. Prima che inizi la rigenerazione, qui ha luogo una delicata depressurizzazione alla pressione atmosferica. Il soffiatore di rigenerazione invia l'aria ambientale al riscaldatore a valle. Segue un riscaldamento fino alla temperatura di desorbimento necessaria.
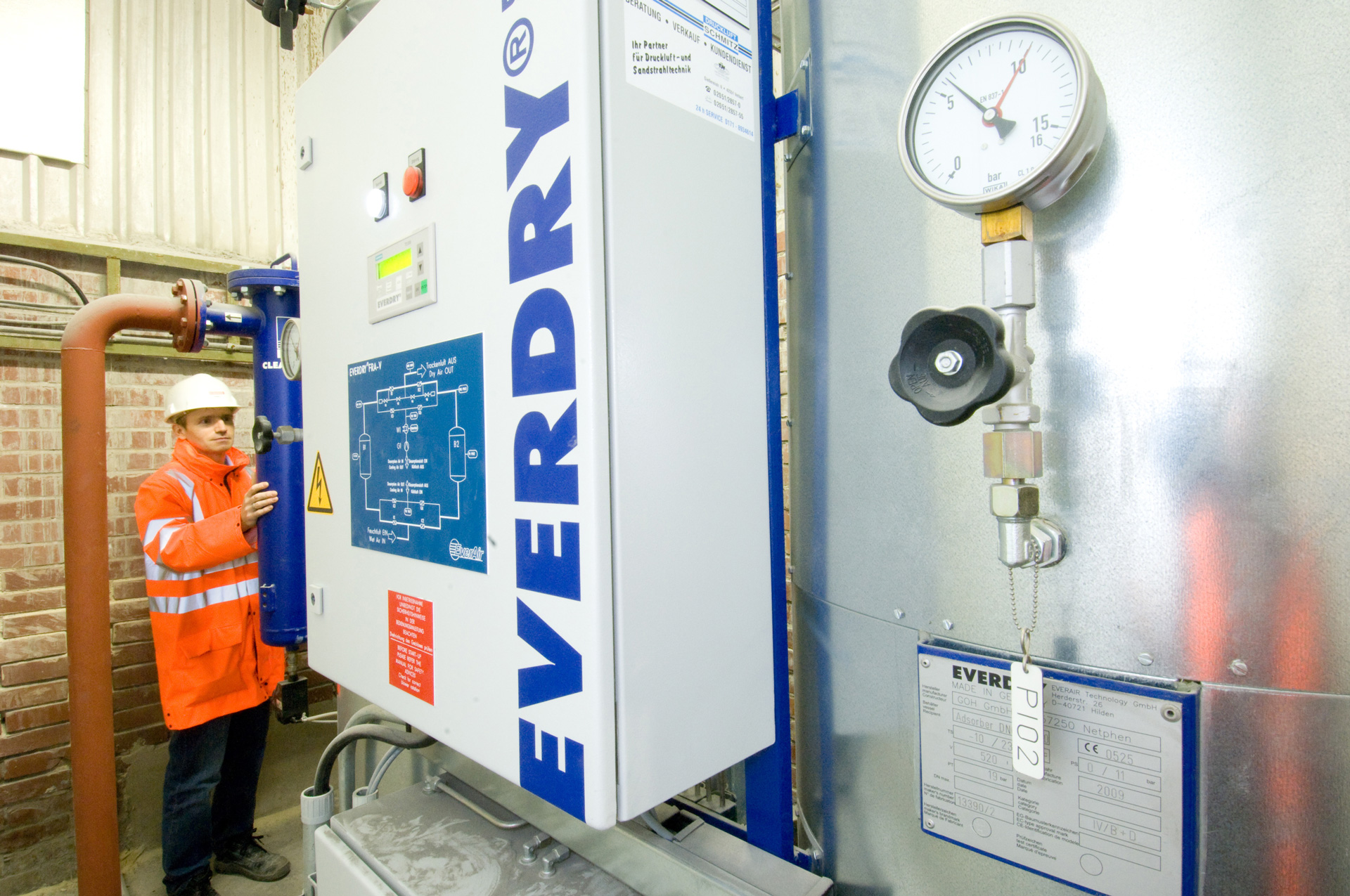
Il soffiatore di rigenerazione nel funzionamento a pressione provoca un aumento della temperatura, con effetto positivo per il fabbisogno energetico del riscaldatore. Il flusso d’aria ventilata vaporizza l’umidità acquisita nel materiale essiccante e infine viene avviato nell'atmosfera insieme al flusso d’aria. Il desorbimento avviene mediante flusso in controcorrente con ottimizzazione energetica.
La fase di raffreddamento avviene in modalità sottovuoto. I picchi di temperatura e punti di rugiada dopo la commutazione vengono evitati, poiché il calore immagazzinato nel materiale essiccante dopo la fase di desorbimento viene tenuto lontano con il flusso freddo d’aria ventilata. Nella fase di raffreddamento, il soffiatore passa in modalità di aspirazione, mediante cui l’aria ambiente fluisce immediatamente nei contenitori di adsorbimento raffreddanti. La sottopressione generata durante l’aspirazione realizza una modifica della bilancia fisica nel materiale essiccante. Mediante la sottopressione, si abbassa la temperatura di desorbimento, e quindi durante la fase di raffreddamento si innesta un ulteriore desorbimento. Attraverso questo ulteriore desorbimento, nel materiale essiccante, dopo la fine della fase di rigenerazione (riscaldamento e raffreddamento) si origina una carica residua ridotta. La carica residua nel materiale essiccante influisce molto sulla qualità della fase di essiccazione.
In meno di un anno, grazie all’efficiente esercizio dell’essiccatore ad adsorbimento con generazione a caldo rispetto a uno a freddo, Ramondis ha realizzato l’ammortamento dei costi di investimento. Tuttavia, con la decisione di scegliere una soluzione di BEKO TECHNOLOGIES GmbH, Remondis non ha goduto solamente di questa prospettiva. Per noi era importante anche la flessibilità e il pensare senza limiti in fase di progettazione e realizzazione. E, ovviamente, Remondis, con un fornitore di sistema come BEKO TECHNOLOGIES, era in ottime mani. Il fatto che a una bellissima teoria seguì anche una pratica di successo, lo dimostra dall’autunno 2009 l’impiego altamente efficiente dell'essiccatore presso il forno 7 nello stabilimento Lippe di Lünen.
Inoltre, l'essiccatore ad adsorbimento EVERDRY non ha solamente portato a termine la questione della pulizia dei filtri. È chiaramente migliorata anche la sicurezza di processo in un altro campo di applicazione dell’aria compressa presso il forno 7: il funzionamento dei sistemi di misura presso l’impianto a combustione. Anche i problemi con l’umidità e l’olio presso gli ugelli di combustione del forno appartengono ormai al passato sin dall’installazione dell'essiccatore.
Essiccazione ad adsorbimento con sistema
La serie di prodotti EVERDRY di BEKO TECHNOLOGIES offre tante possibilità di variazione. La serie standard è disponibili per portate fino a 20 000 m³/h. Dell’offerta fanno parte anche soluzioni speciali oltre i 20 000 m³/h. Gli impianti della serie FRA-V, come essiccatori ad adsorbimento Zero Purge dall’alto livello tecnico, rappresentano la base economica di svariate applicazioni.
Anche per l’uso ad alte temperature d'ingresso in zone climatiche calde e umide, la gamma di prodotti EVERDRY offre soluzioni adatta con un intelligente rapporto costi-vantaggi. L’EVERDRY FRL come essiccatore ad adsorbimento “closed-loop”, con la sua conduzione del freddo in un circuito chiuso si adatta persino all’impiego in condizioni climatiche tropicali.
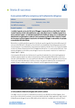