Technique de l'air comprimé dans l'industrie de l'emballage
Secteur d'activité : | Emballage, papier |
Client / Lieu / année : | Delkeskamp, Nortrup (Allemagne), 2008 |
Utilisation de l'air comprimé : | Air de commande, air de processus, technique des condensats |
Produits installés : | EVERDRY, BEKOSPLIT |
Ce secteur industriel n'est pas de la pacotille : Plus de 100 entreprises spécialisées avec environ 19000 employés fabriquent et transforment le carton ondulé en Allemagne. L'air comprimé et son traitement jouent un rôle déterminant dans le processus de production. L'humidité dans l'air comprimé en particulier aurait des conséquences fatales pour les installations, les matières premières et les produits finis.
Avec une production annuelle avoisinant les neuf milliards de mètres carrés de carton ondulé, l'Allemagne est au premier rang en Europe et 4ème rang au niveau international derrière les États-Unis, la Chine et le Japon. Près des deux tiers de toutes les marchandises transportées en Allemagne sont déplacées dans du carton ondulé, et près de 30 % de tous les emballages en carton ondulé remplis traversent les frontières sur le chemin vers le consommateur. Donc un secteur très important qui mobilise beaucoup de monde et qui a une importance correspondante pour toute l'économie nationale allemande.
L'un des pionniers, défricheurs et prestataires de services dans ce secteur industriel est la Delkeskamp Verpackungswerke GmbH, de Nortrup en Basse-Saxe. Fondée dès 1896 comme fabrique de carton, elle produit aujourd'hui, en plus de l'usine-mère de Nortrup, sur différents sites de production à Hanovre ainsi qu'à Odry, en République Tchèque. On produit du papier, du carton et de la mousse pour emballages dans de multiples coloris.
Circuit de production fermé
La matière de départ pour la fabrication est le papier brut pour carton ondulé. L'entreprise Delkeskamp GmbH produit elle-même la plus grande partie du papier brut dont elle a besoin dans l'usine de Nortrup. Ainsi, ce site est le premier maillon d'un circuit de production fermé et il a donc une importance décisive pour la fonctionnalité et la rentabilité de la structure globale de production de Delkeskamp. En plus des avantages techniques purs, la fabrication propre de papier brut pour carton ondulé assure à l'entreprise une indépendance maximale par rapport au marché de l'approvisionnement.
Chez Delkeskamp, on aime bien voler de ses propres ailes. Ainsi, la vapeur nécessaire à la production du papier est produite à Nortrup dans leur propre centrale thermique à l'aide de turbines à gaz modernes. Par ce processus, l'électricité est produite dans une quantité dépassant nettement le besoin propre, et réinjecté dans le réseau public. Ainsi l'entreprise est non seulement son propre fournisseur d'énergie, mais également un fournisseur reconnu en Basse-Saxe.
En plus de la sécurité du processus indispensable dans la fabrication propre, l'entreprise a donc une certaine responsabilité vis-à-vis des habitants de la région. Des attentes que l'on doit satisfaire. L'une des pierres angulaires pour cela est l'alimentation stable et de haute qualité en air comprimé - une source énergétique décisive à plus d'un titre pour la production.
L'air comprimé est une source d'énergie décisive
À Nortrup, trois (en fait quatre) secteurs d'exploitation sont alimentés en air comprimé. Ce sont essentiellement l'usine de papier, la production de carton ondulé et l'usine de mousse. La centrale thermique interne à l'entreprise a également un besoin, même s'il est beaucoup plus faible.
Sans air comprimé, presque rien ne bougerait chez Delkeskamp. Pour comprendre cela, il faut simplement se représenter les séquences de fabrication esquissées dans les trois secteurs de production : dans la première étape de fabrication du carton, le papier brut pour carton ondulé fabriqué à partir de vieux papier dans d'énormes installations ultramodernes est tout d'abord réchauffé et humidifié. Il atteint ainsi l'élasticité nécessaire pour être mis en forme. Dans l'étape suivante, le papier est dirigé sous pression et sous l'effet de la chaleur entre deux cylindres cannelés imbriqués l'un dans l'autre comme des pignons. Ensuite, le papier ondulé est d'abord collé avec la bande de papier intérieure par le dessus, puis avec la bande extérieure par le dessous. Ainsi le carton ondulé peut développer son effet protecteur optimal.
Dans des séquences de travail entièrement automatisées, les formats de carton ondulé sont transformés en caisses pliantes, emballages découpés, emballages intérieurs rembourrés et présentoirs. Tout ceci est piloté ou déplacé par d'innombrables systèmes pneumatiques et par des régulateurs et des coulisseaux commandés par air comprimé. Dès qu'il y a un accroc dans cette séquence de production très bien coordonnée, les conséquences sur le quota de production et surtout sur la qualité de la production sont immédiates.
Le principal : de l'air comprimé sec
Ce dont Delkeskamp a besoin avant tout, en parallèle à un approvisionnement continu, c'est de l'air comprimé sec. Une entrée d'humidité dans l'air comprimé est un pur poison pour les installations pneumatiques et pour les produits.
Mais l'air comprimé humide ne présente pas seulement un risque pour le papier et le carton ondulé. Dans le troisième domaine de production de Delkeskamp, la production de mousse, le caractère sec est également impératif. Ici des formes moulées conçues pour différents emballages sont fabriquées en polystyrène expansé (PSE). Ce qui est couramment appelé polystyrène expansé s'appelle du Denopor chez Delkeskamp, et il complète le concept d'emballage sans lacunes du fabricant.
Dans ce domaine d'exploitation, l'air comprimé est utilisé entre autres pour le fonctionnement des machines de moulage, le déplacement des vérins de réglage et l'activation des vannes. Il sert en plus à l'éjection par soufflage des pièces moulées terminées hors des machines. Étant donné que les pièces en Denopor finies éjectées par soufflage de la machine de moulage sont stockées dans un hall non chauffé, elles doivent être absolument sèches. En effet, ce matériau, qui ne craint habituellement aucune sollicitation, est très sensible aux très basses températures. L'humidité augmente encore naturellement cette sensibilité.
Le caractère sec est donc tout en haut de la liste des priorités de l'alimentation en air comprimé pour Delkeskamp Verpackungswerke GmbH. C'est également le cas dans l'extension devenue nécessaire de l'installation d'air comprimé dans l'usine-mère de Nortrup. Les extensions et les investissements dans l'agrandissement et la modernisation de la production sont considérables depuis 2007.
Besoin accru en air comprimé après l'extension de l'usine
Le poste d'air comprimé utilisé jusqu'ici dans la « cave des compresseurs » n'a pas pu suivre le rythme de cette croissance du point de vue de la puissance. Les cinq compresseurs installés dans ce local et suivis en aval du sécheur par adsorption avaient besoin de renfort en urgence. Et un autre « candidat menacé » présent depuis longtemps devait enfin être mis à la retraite : le séparateur statique huile-eau qui ne fonctionnait plus depuis longtemps comme Delkeskamp le souhaitait.
La recherche d'une solution moderne à ce problème a conduit Delkeskamp, après une étude intensive du marché, à un interlocuteur totalement nouveau pour eux : le fournisseur de systèmes d'air comprimé BEKO TECHNOLOGIES GmbH.
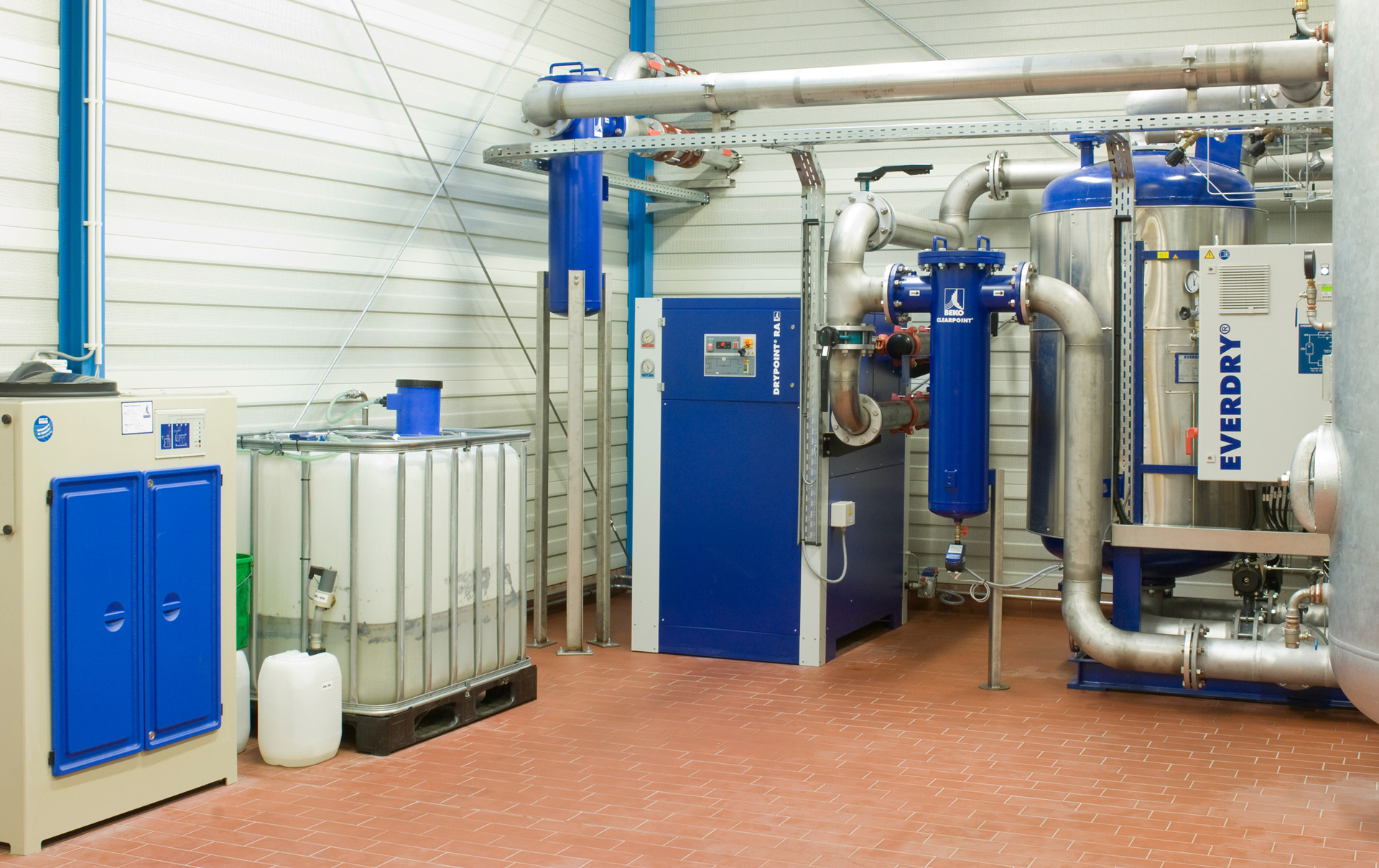
L'entreprise située dans la Neuss rhénane et active dans le monde entier possède dans sa gamme de prestations une technologie de séparation des émulsions huile-eau : BEKOSPLIT. Les installations de séparation purifient les condensats émulsifiés, comme ils apparaissent dans des conditions de sortie défavorables ou dans certaines combinaisons de lubrifiant et de condenseur. Outre le condensat issu des réseaux d'air comprimé, d'autres effluents industriels huileux peuvent être traités. Les impuretés organiques non solubles dans l'eau, comme les huiles, les graisses végétales ou animales, ainsi qu'une multitude d'impuretés solides sont éliminées de l'eau. Par ailleurs, les métaux lourds, la saleté et les particules de peinture éventuellement présents sont adsorbés avec fiabilité.
Ici le principe BEKOSPLIT fonctionne de manière plus efficace qu'une ultrafiltration : aucun produit nettoyant agressif n'est nécessaire et on utilise moins d'énergie. Le besoin en investissement est tout à fait raisonnable et des intervalles d'entretien plus longs favorisent en plus la rentabilité.
Un système fait ses preuves
Mais ce contact avec le spécialiste de l'air comprimé BEKO TECHNOLOGIES devait produire d'autres fruits. Delkeskamp s'est rapidement rendu compte qu'ils avaient trouvé avec BEKO TECHNOLOGIES un partenaire qui fonctionnait comme eux. Qui développait des concepts globaux avec une vision d'ensemble et cohérents. La chose commença à être passionnante.
Surtout quand BEKO TECHNOLOGIES a commencé à reconsidérer le sujet du séchage de l'air comprimé si sensible pour Delkeskamp. Par exemple du point de vue de la rentabilité. Toutefois, alors que l'on allait jusqu'à transférer une bonne partie du traitement, effectué jusqu'ici exclusivement par des sécheurs par adsorption, à des sécheurs frigorifiques, les portes se refermèrent à nouveau.
Pour Delkeskamp, cette proposition fut tout d'abord reçue comme une révolution de palais, ils faisaient confiance uniquement au principe et à la sécurité du séchage par adsorption pour la conception de l'installation. Jusqu'ici il n'y avait eu aucun problème et ils ne voulaient courir aucun risque. D'autre part l'idée du sécheur frigorifique était très attrayante, quand on considère le bilan énergétique largement plus économique de cette méthode par rapport au sécheur par adsorption. Si on pouvait alors combiner les deux...
Exactement le défi qui convient au fournisseur de systèmes BEKO TECHNOLOGIES. En quelques jours, il a développé pour Delkeskamp un concept cohérent pour un système combiné redondant à partir de sécheurs par adsorption et frigorifiques. Ceci est devenu réel en mai 2008.
Ce système permet au fabricant d'emballage, selon l'exigence et les conditions environnementales, par exemple saisonnières, de faire tourner l'ensemble de sécheurs les plus rentables ainsi que les plus sûrs. Soit comme combinaison flexible de deux méthodes, ou bien exclusivement par séchage par adsorption ou frigorifique.
Étant donné que les conduites de distribution de l'air comprimé au sein du site circulent essentiellement à l'extérieur en empruntant des passerelles pour passage de tuyauteries, elles sont naturellement exposées à d'importantes fluctuations de température, en fonction des saisons. Ainsi, il faut par exemple fixer un point de rosée meilleur que moins 40 °C pour la protection contre la condensation ultérieure et le gel en hiver. Pour atteindre la plus haute sécurité de processus, les sécheurs par adsorption EVERDRY installés par BEKO TECHNOLOGIES sont équipés d'unités de mesure du point de rosée et de commande du point de rosée. Jusqu'à présent cela fonctionne parfaitement. L'efficacité du séchage est absolument stable et le bilan énergétique s'est considérablement amélioré.
Actuellement Delkeskamp mise exclusivement sur les appareils de BEKO TECHNOLOGIES pour la préparation modernisée de l'air comprimé. À côté des installations de séparation, des sécheurs par adsorption EVERDRY ainsi que des sécheurs frigorifiques DRYPOINT, les filtres CLEARPOINT remplissent également leur mission.
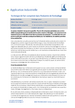