Traitement de l'air comprimé dans l'industrie alimentaire
Secteur d'activité : | Industrie alimentaire |
Client/Lieu/Année : | Nukameel, Weert (Pays-Bas), 2014 |
Utilisation de l'air comprimé : | Air de convoyage, air comprimé process |
Produits installés : | DRYPOINT RA, BEKOMAT |
Environ 150 tonnes de matières premières en poudre pour le lait de substitution doivent être transportées chaque jour par des camions-citernes dans des silos à l'entreprise néerlandaise Nukamel. Un air de comprimé de faible pression est utilisé comme média de transport. S'il contient trop d'humidité, le système est menacé de paralysie : par l'encrassement des flexibles d'alimentation avec de la poudre incrustée. Des conditions inhabituelles sur le site compliquent la tâche.
Comme l'adresse « Industrikade » ne le laisse pas deviner, on se trouve ici dans un paysage idyllique authentiquement néerlandais : Juste devant la porte s'écoule le canal Zuid-Willemsvaart. Sur la rive en face tourne paresseusement un moulin à vent dans la légère brise estivale. Son ombre portée vient rafraîchir le camping à ses pieds. Et dans le voisinage, on entend jouer des enfants dans les jardins des maisons. La vie est belle à Weert près de Roermond - et on entend qu'elle le reste. Le paysage est plaisant, ensoleillé et particulièrement calme.
C'est justement en cela que réside le défi pour les entreprises industrielles qui se trouvent au milieu de cette partie bucolique des Pays-Bas. Elles doivent, malgré tous les atouts économiques du site, composer avec une réglementation antibruit sévère. Et aussi avec l'hygrométrie élevée résultant des zones humides environnantes. Par exemple, Nukamel, le numéro un mondial des laits de substitution pour l'élevage, fondé en 1954. Issue des producteurs laitiers traditionnels que sont les Pays-Bas et la Belgique, l'entreprise Nukamel est maintenant représentée dans plus de 40 pays au niveau mondial.
Sur la terre entière, pour l'élevage, les laits de substitution sont un aliment incontournable pour les premières semaines. Ils servent par exemple à pallier au lait maternel. Ou alors quand il n'y a pas assez de lait cru dans l'alimentation. Les exploitations exclusivement dédiées à l'élevage non par ailleurs souvent pas la possibilité de transformer le lait produit en interne en aliment. Eux aussi doivent faire appel aux laits de substitution longue conservation de Nukamel.
L'immense diversité des besoins en alimentation des différentes espèces d'animaux au cours des différentes phases de leur vie nécessite une connaissance approfondie pour maîtriser la recette appropriée.. Avec plus de 20 marques alignées suivant les différents besoins en nourriture, Nukamel assure la santé et la croissance de veaux, de porcelets, d'agneau, de poussins et de nombreux autres jeunes bêtes. Ici, l'ensemble des recettes est uniquement composé de matières premières naturelles.
Toutes les matières premières ont en commun d'être pulvérulentes, et leur livraison par camion citerne dans l'usine néerlandaise de Nukamel juste à côté du canal de Zuid-Willemsvaart se fait au milieu d'une zone d'habitation.
Environ 150 t de poudre tous les jours
Ce sont environ 150 t de poudre qui parviennent tous les jours à Weert en un à cinq convois de camions-citernes. Et ce n'est pas une destination comme les autres, réglementations antibruit locales oblige. Celles-ci ne permettent en effet pas que le chargement pulvérulent, comme c'est usuellement le cas, soit transporté depuis la citerne dans les silos de Nukamel par air comprimé à l'aide d'un compresseur se trouvant sur le poidslourd. « Trop bruyant », avancent les valeurs de seuil locales.
Chez Nukamel, la production de l'air de convoyage pour la matière première livrée par les poidslourds est donc prise en charge par une installation d'air comprimé dédiée. Celle-ci se compose d'un compresseur basse pression sophistiqué avec une isolation acoustique poussée se trouvant au cœur du bâtiment. Basse pression parce que les cuves des poids-lourds peuvent recevoir au maximum une pression de deux bar. Le flux d'air circule depuis de compresseur à l'aide d'un long flexible jusqu'au poids-lourd, puis de là, chargé de poudre, vers le silo. Sur cette trajectoire apparaît un problème typique de l'air comprimé : sa teneur en eau. Lors d'une belle journée d'été avec une température de l'air de 25°C et une humidité relative de 60%, l'air aspiré par le compresseur contient en gros 13 g d'eau par mètre cube. Pour une consommation d'air de 1000 m³/h, cela correspond tout de même à 13 l/h !
Lors du refroidissement de l'air comprimé humide, du condensat se dépose : à l'intérieur des tuyaux menant vers le camion-citerne, dans la citerne-même et dans les tuyaux du camion-citerne vers le silo.
Par principe, la rencontre entre l'humidité et la matière pulvérulente à convoyer constitue une combinaison précaire pouvant provoquer de nombreuses difficultés, de la dégradation de la qualité par formation de grumeaux jusqu'à une prolifération bactérienne au niveau du produit. De tels problèmes ne sont heureusement jamais survenus chez Nukamel, mais un problème « logistique » significatif était tout de même posé : l'humidité dans les tuyaux affectait l'efficacité du transport de la poudre. En faite, le dépôt continu de la poudre de matières premières sur les parois intérieures des flexibles augmentait le risque d'infarctus du système de transport par « calcification des artères ».
Pour prévenir cet infarctus, la solution était « une opération d'urgence » tous les deux ou trois camions vidés : un nettoyage mécanique des tuyaux démontés par curage, brossage et soufflerie ; une opération qui prenait à chaque fois deux à trois heures.
La situation est devenue précaire mi 2013 à cause d'une augmentation de la fréquence de livraison d'une poudre particulièrement hygroscopique. La fréquence des arrivages de poids-lourds et le travail de nettoyage qui lui était lié devenaient ingérables et hors de prix. La fourchette haute des calculs prévoyait dix à douze heures d'arrêt par semaine, donc en cumulés quatre jours par mois ; ce qui pour Nukamel revenait à 3000 € par mois. Le tout sans mentionner le travail de nettoyage additionnel des poids-lourds, quand bien même celui-ci était pris en charge par les transporteurs.
Il était donc plus qu'urgent d'agir. L'objectif était clair : une mise à disposition d'air de convoyage sec ! Mais le problème était que la compression de l'air de convoyage n'était que de 1,8 bar. Les sécheurs d'air comprimé usuels sont réglés pour des taux de compression sensiblement plus élevés et – cela peut paraître paradoxal – sont totalement débordés par cette demande trop faible.
Les responsables de Nukamel ont rapidement compris que les versions conventionnelles des sécheurs ne permettraient pas de parvenir à une solution satisfaisante.
La solution est finalement venue d'une analyse de l'entreprise partenaire de Nukamel en Belgique qui avait déjà réussi à maîtriser des difficultés similaires à l'aide de la technologie de séchage du fournisseur allemand d'air comprimé BEKO TECHNOLOGIES.
Entre la première réunion de planification et la réalisation les concepteurs et les planificateurs de BEKO TECHNOLOGIES ont eu à peine besoin de 3 mois pour assurer à Nukamel aux Pays-Bas le même soulagement. En l'occurrence, de l'air comprimé absolument sec.
Un sécheur frigorifique pour de l'air faiblement comprimé
C'est un sécheur frigorifique DRYPOINT RA de BEKO TECHNOLOGIES spécialement dimensionnées pour les exigences particulières de l'air faiblement comprimé qui a été installé.
Au sein du DRYPOINT RA, le séchage de l'air comprimé s'effectue par un échange de chaleur optimal à contre-courant sur l'intégralité du tronçon. L'air circule par un déplacement constant orienté vers le bas, sans aucune déviation défavorable. Cet échangeur de chaleur à contre-courant, bien dimensionné et composé entre autres d'un échangeur de chaleur air/air et d'un échangeur air/fluide frigorigène, refroidit l'air comprimé jusqu'à une température de +3°C ; la taille de l'échangeur de chaleur permet non seulement d'obtenir un refroidissement particulièrement efficace, mais aussi d'abaisser la résistance à la circulation de l'air comprimé à un minimum absolu. Cet aspect est une condition essentielle pour une mise en œuvre réussie avec une compression réduite, comme c'est ici le cas chez Nukamel.
L'air comprimé chaud et saturé en humidité est soumis à un refroidissement préliminaire à l'entrée du sécheur frigorifique, au sein de l'échangeur de chaleur air/air. De ce fait, l'énergie frigorifique requise au sein de l'échangeur de chaleur air/fluide frigorigène est réduite et le système gagne en efficacité énergétique.
La gravité favorise la formation de gouttelettes plus importantes et permet ainsi d'atteindre une séparation proche de 99%. Au sein du collecteur de condensat de grandes dimensions, doté en aval d'un conduit de renvoi d'air, la vitesse de circulation est fortement abaissée. Le réentraînement des gouttelettes séparées est empêché, en toute fiabilité.
La purge des condensats, de série
Comme la plupart des sécheurs frigorifiques DRYPOINT RA, le modèle installé chez Nukamel dispose également de série d'un purgeur de condensats à régulation de niveau BEKOMAT. Il est bien plus efficace et bien plus fiable qu'un purgeur temporisé ou un purgeur à flotteur comme cela est souvent installé par la concurrence. Il est par exemple ainsi possible à BEKOMAT de purger du condensat sans aucune perte d'air comprimé, une économie en termes de coût qui est parfois plus élevé que l'ensemble de la consommation électrique du sécheur frigorifique.
Avant de quitter le DRYPOINT RA, l'air comprimé séché et refroidi, est à nouveau réchauffé au sein de l'échangeur de chaleur air/air. L'humidité relative de l'air est considérablement abaissée et environ 60 % de l'énergie frigorifique utilisée est récupérée.
Au niveau de Nukamel, cela signifie concrètement que l'air fourni par le compresseur à une température de 180°C atteint le refroidisseur intermédiaire à environ 60°C et est refroidi au cours du séchage à environ 3°C. À la sortie du DRYPOINT RA et après le réchauffage, la température est à nouveau de 22°C, la température idéale pour de l'air de convoyage. Et l'hygrométrie ? Si à l'entrée du sécheur elle était encore de 100%, après le traitement et n'est plus que de 30%. Ici aussi des conditions idéales.
Des valeurs idéales, qui n'ont pas eu à se stabiliser lentement après l'installation chez Nukamel. Le système DRYPOINT RA livré entièrement « clé en main » assemblé dans un boîtier a en effet fonctionné à plein rendement dès le départ.
De l'air comprimé « propre »
La surveillance du fonctionnement et de l'action du séchage d'air comprimé est également un jeu d'enfant pour Nukamel. C'est le rôle qu'assume l'unité de commande conviviale du système qui se trouve sur le carter de l'appareil.
Outre le contrôle du fonctionnement du sécheur, la commande assure également la surveillance du purgeur de condensats à régulation électronique de niveau, affichage d'éventuelles défaillances compris. Un système de purge évolué (ADS : Advanced Draining System) enregistre les signalisations d'état du purgeur de condensats et déclenche une alerte correspondante le cas échéant. Même la fonction Test du purgeur peut êtré déclenchée de façon centralisée à partir de la commande.
C'est donc un « travail propre » qui se fait au niveau du Industriekade 32 dans le village idyllique de Weert près de Roermond. Et c'est également plus tranquille car non seulement les tuyaux restent absolument secs mais également l'intérieur des citernes des poids-lourds. Et cela signifie moins de travail de nettoyage sur site. Ce dont se réjouissent autant les voisins que les transporteurs.
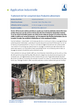