MONIN – BEKO TECHNOLOGIES : une love-story franco-allemande pour un air comprimé de haute qualité !
Secteur d'activité : | Industrie alimentaire |
Client/Lieu/Année : | MONIN , Bourges , 2018 |
Utilisation de l'air comprimé : | Dans la production |
Produits installés : | EVERDRY , METPOINT OCV , CLEARPOINT , BEKOMAT |
En l’espace d’un siècle, MONIN est devenu une référence mondiale pour les particuliers comme pour les professionnels. Son outil industriel est à l’image de ses produits : irréprochable. Logique que l’entreprise de Bourges croise la route de BEKO TECHNOLOGIES pour une qualité d’air comprimé elle aussi irréprochable.
Célèbre pour son Printemps musical qui vient de souffler ses 40 bougies, la ville de Bourges est aussi connue dans le monde entier comme la capitale incontestée du sirop haut de gamme : le sirop de Monin. Créée en 1912 par Georges Monin, transmise ensuite à son fils Paul à la fin de la Seconde Guerre mondiale, l’entreprise est aujourd’hui dirigée par le petit-fils du fondateur, Olivier, à qui l’on doit le développement de la marque à l’international…
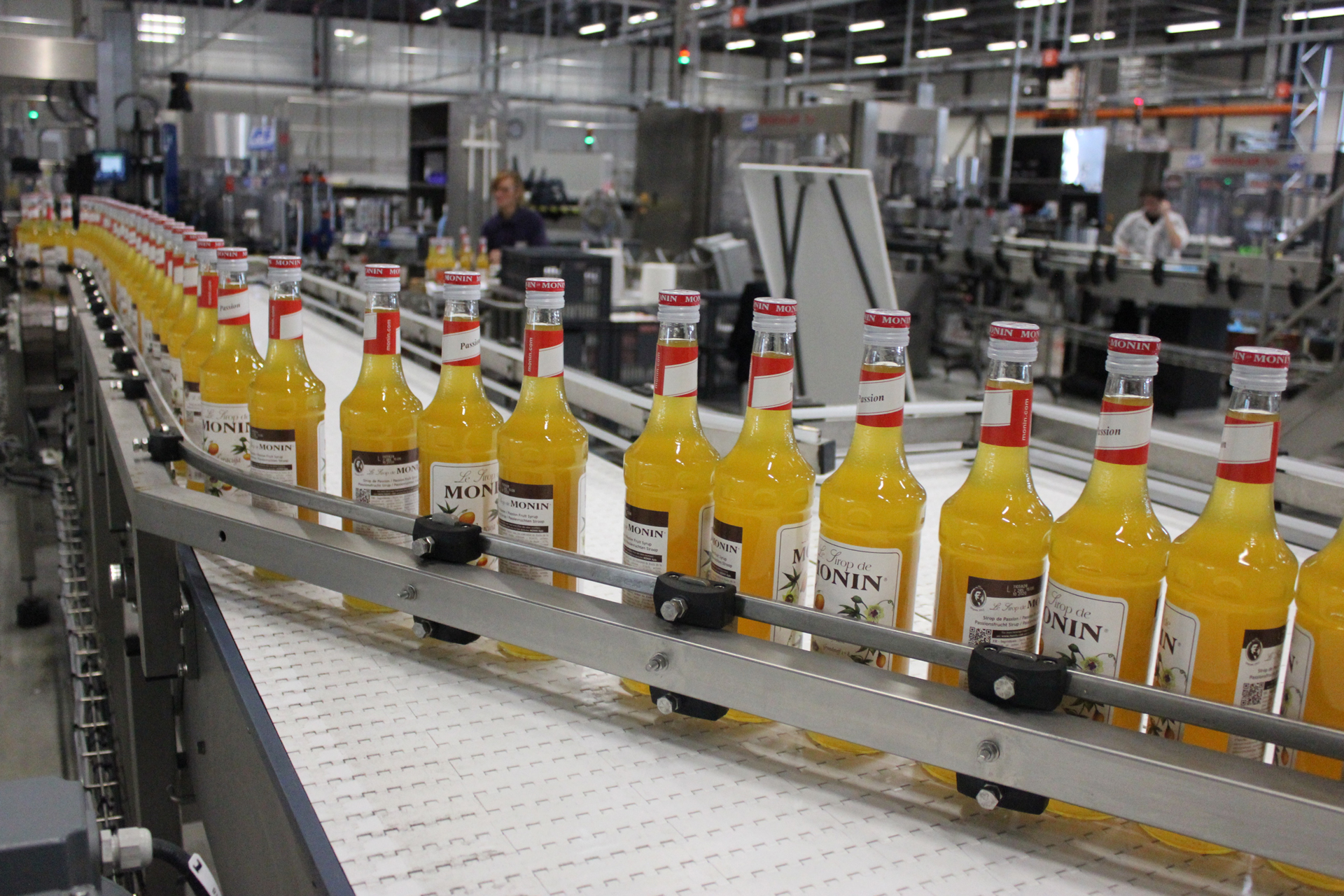
Qui dit développement dit croissance, embauche, contraintes de production, agrandissement/extension du site, et pourquoi pas transfert ?
Devenu exigu et peu pratique pour la logistique, avec un manque de place en termes de stockage, le site historique de MONIN a été transféré dans un local flambant neuf de 20 000 m² … pour l’instant situé en périphérie. Comme l’explique Camille Moreau, responsable maintenance du site, « l’entreprise a déjà planifié l’extension d’une partie des bâtiments actuels, aussi bien pour la production que pour la logistique ». Rien de plus normal pour une marque en plein développement qui réalise des progressions à deux chiffres depuis plusieurs années. « Depuis Bourges, nous alimentons les marchés européen, africain et russe. Le reste du monde est couvert par nos unités de production en Chine, en Malaisie et aux États-Unis. »
Un partenariat de longue date renouvelé
Des six lignes de production sortent chaque jour 150 000 bouteilles, ce qui représente environ 25 millions d’unités à l’année. L’ensemble des outils de production a été récupéré du site historique, la centrale de production d’air comprimé comprise. Contrairement aux différents éléments qui composent les chaînes d’embouteillage, cette station joue désormais les seconds rôles. « Nous avons pris la décision de déménager l’ancienne centrale de traitement d’air comprimé sur le nouveau site pour l’utiliser comme secours », explique Camille Moreau. « Elle était devenue inadaptée en termes de puissance. » Et, pour cause, la régénération du sécheur par adsorption occasionnait de grosses pertes de pression sur le réseau, limitant par conséquent la production au niveau des utilités. Pour la nouvelle station, c’est la société MIB (Maintenance Industrielle du Berry), partenaire historique de l’entreprise depuis 1987 pour toutes les questions liées au traitement de l’air, qui a été logiquement consultée et challengée par rapport à d’autres offres concurrentes. Afin que ce challenge soit une belle réussite, MIB s’est appuyée sur BEKO TECHNOLOGIES pour la partie traitement d’air comprimé.
Le besoin du client clairement défini
Le client connaissait bien son besoin : remplacer l’ancienne unité de traitement d’air comprimé, comportant entre autres un sécheur énergivore, par un nouveau système, et ce pour traiter un débit d’air comprimé maximal de 1 160 m3 /h, à une pression de service minimum de 8 bars effectifs et à une température d’entrée maximum de + 38 °C, afin d’obtenir un PRSP de -40 °C. Étaient incluses dans ses exigences :
- La réduction des coûts d’exploitation.
- La réduction des coûts énergétiques.
- L’obtention d’un air comprimé de qualité en réponse aux exigences réglementaires et normatives du secteur alimentaire avec la possibilité de le surveiller, de le mesurer et de le tracer.
Des exigences accrues ; une solution adaptée à ces dernières
« Dans ce cas précis, nous avons à faire à un client particulièrement exigeant », confie Cédric Girard, directeur de l’agence MIB à Bourges. « Sur son nouveau site, MONIN a tout mis en œuvre pour s’assurer d’une qualité de traitement de l’air au top ! Et ce n’est pas qu’une image. L’entreprise est allée bien au-delà de ce qui est imposé dans le secteur alimentaire. »
Après étude de l’installation existante et pour répondre au mieux aux attentes et besoins formulés par le client, la société MIB et BEKO TECHNOLOGIES ont opté pour une centrale de production et de traitement d’air comprimé customisée. Il se composée d’éléments standards parfaitement adaptés entre eux, à savoir un compresseur à vitesse variable de 110 kW à vis sèche exempt d’huile pour respecter la classe 1 en termes d’hydrocarbures selon la norme 8753-1, fourni par la société MIB et une unité de traitement d’air comprimé fournie par BEKO TECHNOLOGIES et comportant :
- Un ensemble de filtration CLEARPOINT composé d’un filtre dévésiculeur, d’un filtre déshuileur et d’un filtre antipoussière pour éliminer l’eau, l’huile liquide ainsi que les particules solides comme les poussières.
- Un sécheur par adsorption avec régénération par apport de chaleur EVERDRY modèle FRA-Vplus « zéro purge » pour limiter la consommation énergétique liée au séchage.
- Plusieurs purgeurs BEKOMAT pour évacuer les condensats provenant du réseau d’air comprimé.
- Un débitmètre METPOINT FLM pour contrôler le débit et la consommation de l’air comprimé.
- Un analyseur de la présence d’huile METPOINT OCV pour contrôler et mesurer en permanence la teneur en huile résiduelle sur le réseau d’air comprimé du client, avec une précision de l’ordre du millième de mg/m³. Ce dispositif permet également d’attester la qualité et la pureté de son air comprimé process.
« BEKO TECHNOLOGIES étant un partenaire de longue date du groupe MIB, nous nous sommes naturellement orientés vers une installation utilisant ses produits », confirme Cédric Girard. « Le partenariat prenait tout son sens au regard du niveau d’exigence exprimé par le client. »
Qualité, réputation des produits et satisfaction complète du client
Après plus de deux années d’exploitation de la nouvelle installation de traitement d’air comprimé, Camille Moreau, tire un bilan très satisfaisant.
Satisfaction 1 : lors de la consultation, MONIN a toujours mis l’accent sur la qualité et la réputation des produits, qu’il s’agisse du traitement d’air comprimé ou de l’instrumentation pour le contrôle et la mesure de l’air comprimé utilisé pour le process de production.
« Désormais, tout est surveillé et tracé : débit, consommation d’air comprimé, qualité de l’air », confirme Camille Moreau. « Dès qu’un seuil critique est franchi, une alarme se déclenche. Les informations sont remontées en temps réel vers le service maintenance. Cela permet d’engager des actions correctives si besoin. »
L’analyseur de la présence d’huile résiduelle METPOINT OCV a permis au client d’attester la qualité et la pureté de son air comprimé process et surtout de confirmer qu’il dispose d’un air comprimé de classe 1 selon ISO 8573-1.
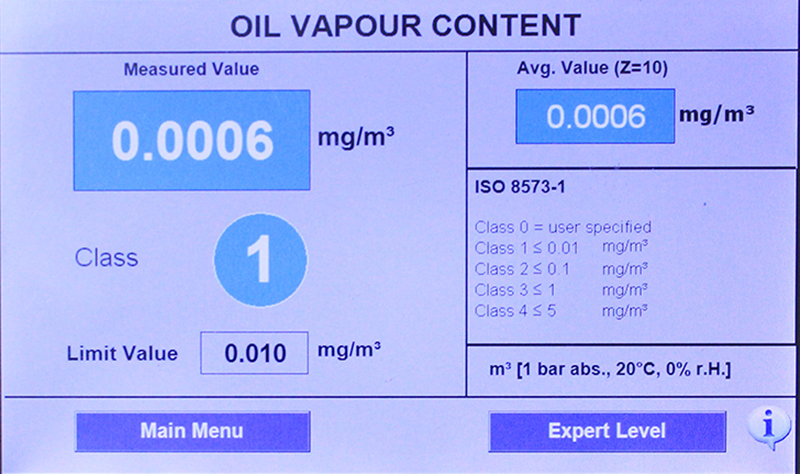
Satisfaction 2 : aujourd’hui, 100 % du débit produit par la station d’air comprimé est un débit utile, et plus aucune baisse de pression ne vient perturber la production. Pour mémoire, la société MONIN avait une exigence particulière : disposer d’une installation d’air comprimé consommant moins d’énergie, tout en délivrant une qualité d’air irréprochable.
Satisfaction 3 : le remplacement de l’ancien sécheur par un sécheur par adsorption avec régénération par apport de chaleur EVERDRY modèle FRA-Vplus « zéro purge » de BEKO TECHNOLOGIES a permis au client d’économiser plus d’1 million de m³ d’air comprimé par an, soit l’équivalent d’environ 15 000 euros par an.
Satisfaction 4 : concernant la qualité de l’air, le client a opté pour un compresseur non lubrifié couplé à un système de filtration spécifique, pour piéger et stopper les hydrocarbures. Afin de s’assurer que l’ensemble de la chaîne de traitement de l’air comprimé ne permettrait aucune migration d’hydrocarbures dans le process, un analyseur de la teneur résiduelle en huile METPOINT OCV a été installé, afin de contrôler et à quantifier la présence d’huile sur le réseau du client. Ce dispositif permet donc au client d’obtenir une traçabilité de la présence ou non des hydrocarbures dans le réseau d’air comprimé départ usine, et ce de manière permanente.
Satisfaction 5 : l’ensemble de la chaîne de traitement de l’air comprimé a permis d’obtenir des résultats bien meilleurs que la classe 1/2/1 selon la norme ISO 8573-1, assurant ainsi l’atteinte des objectifs fixés au niveau du cahier des charges de la société MONIN.
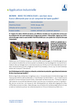