The quality of the activated carbon is decisive
Activated-carbon adsorbers are mainly used for the production of compressed air to ISO 8573 quality class 1. Here, compressed air is cleaned of oil molecules through adsorption. In order to guarantee good oil vapour adsorption, temperatures of < 35°C and sufficient pre-drying – preferably with adsorption dryers – is decisive. However, regular replacement of the activated carbon is also vital. Read on to find out why this replacement is so important and what needs to be taken into account.
In addition, we also take a look at which quality criteria at BEKO TECHNOLOGIES play a role within the context of selection of activated carbon, and which products and services we offer related to the topic of activated-carbon adsorbers.
Why is the replacement of activated carbon so important?
Like a soaked sponge, the surface of activated carbon is only absorbent to a certain degree, and has to be replaced for function to be retained. In the event of unprofessional maintenance, the residual oil vapour content downstream can be higher than before. Indicators that replacement is due include humidity, pressure loss and increased residual oil vapour content in the compressed air.
Our customer service will be happy to help you with the measurement and analysis of the activated carbon you use.
What should you look out for when replacing activated carbon?
1. Always remove used activated carbon fully
During operation, air flows through the activated carbon bed from top to bottom. Oil vapour and oil aerosols are absorbed in the inlet layer initially. Once this is saturated, saturation progresses to the outlet connection. The complete replacement of the activated carbon must take place before the outlet layer is saturated, since otherwise downstream pipes and other treatment components – and thus at the end of the day the product itself – will become contaminated.
The extraction of used activated carbon should start at the inlet connection. Thus the possibility of saturated residual shares falling to the outlet side and contaminating the compressed air again is excluded.
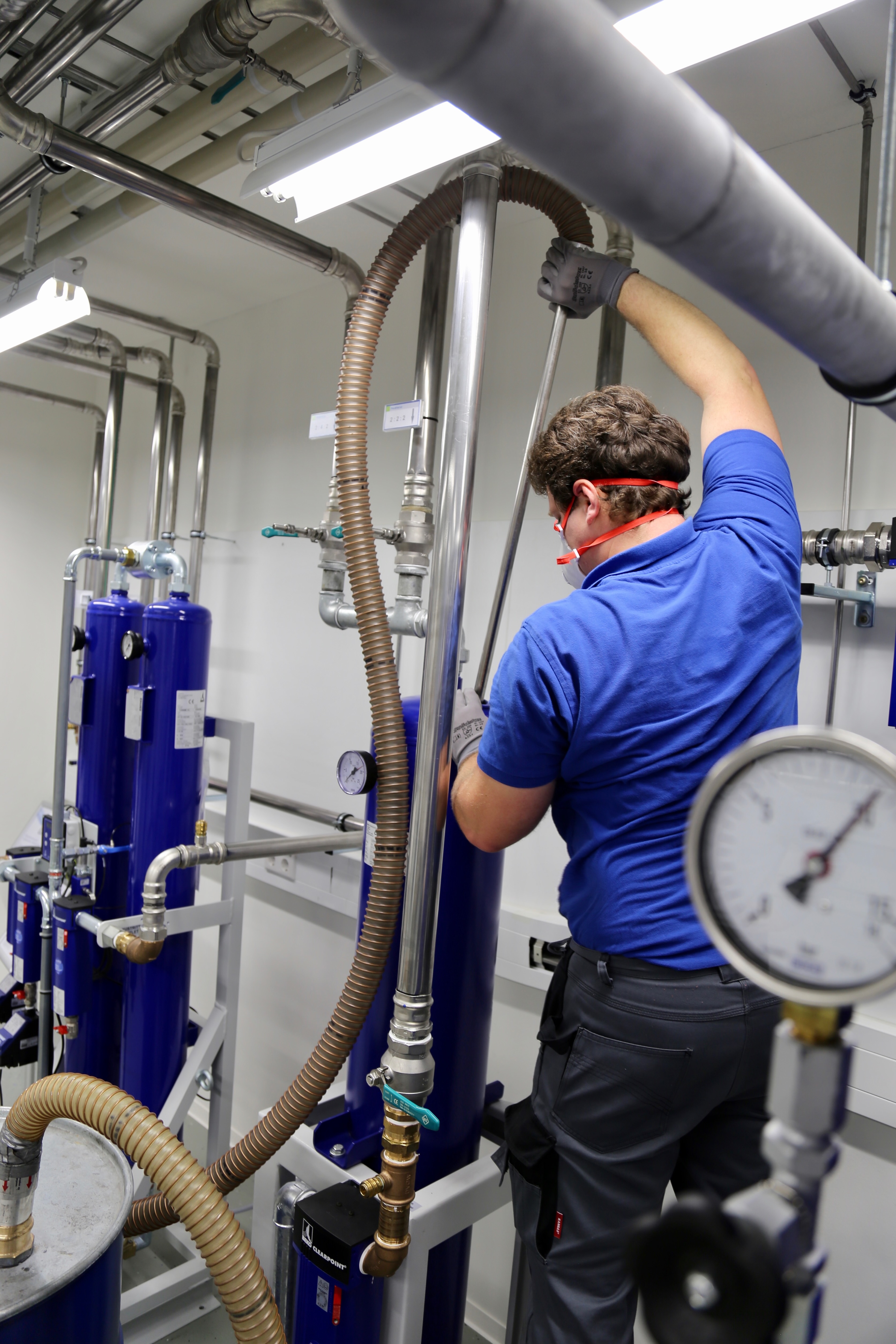
2. Fill with pre-dried activated carbon
Activated carbon is water absorbent. For this reason, it belongs to the group of adsorbents. At a relative humidity of >30% it absorbs more steam. At the same time, its oil absorption capacity falls. Filling with pre-dried activated carbon is essential for a good performance and a residual oil content < 0.01 mg/m³.
a) Pre-dried activated carbon is not only important for low residual oil content, but also when a constant compressed air quality is to be guaranteed. Because not only the residual oil content can vary due to non-pre-dried activated carbon, the humidity content can, too. If the activated carbon is not pre-dried or not pre-dried sufficiently, the dry compressed air flow can contain more humidity through desorption , since the compressed air absorbs humidity from the carbon.
b) It can only be guaranteed with pre-dried carbon that 100% of the activated surface is available right from the start, and that no energy has to be used initially to remove humidity.
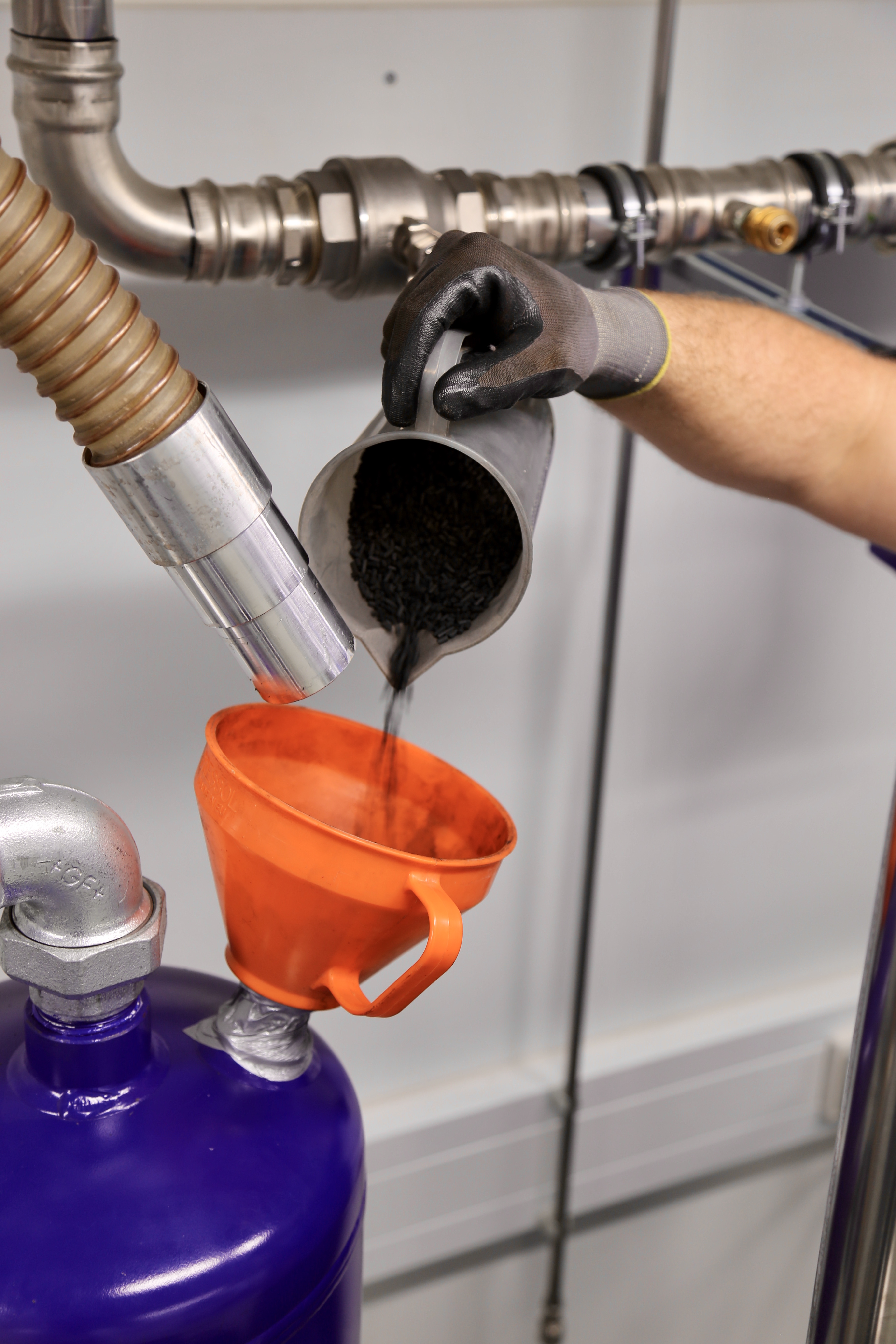
3. Watch out for possible contamination during handling
Care must be taken to maintain maximum cleanness during replacement of the activated carbon. This also includes ensuring that the personnel carrying out the work is wearing gloves that are free of hydrocarbons. In addition, the containers should only be opened just before the adsorber is filled so that the carbon cannot adsorb any humidity from the ambient air.
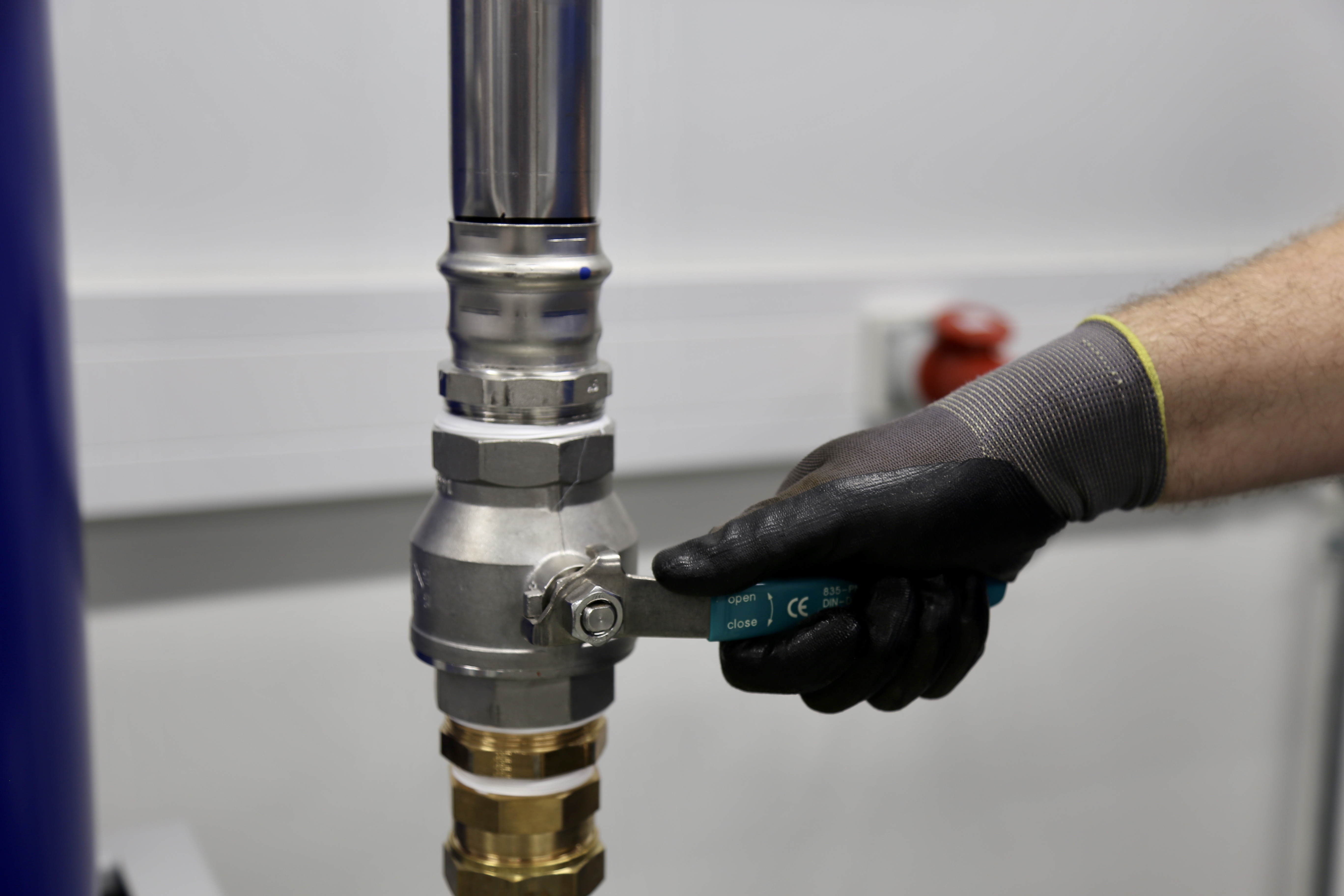
4. Do not use oil-contaminated particle filter elements
Specially cleaned particle filters must be installed downstream from activated-carbon adsorbers. Their installation must take place without the use of lubricants containing hydrocarbons. The same great care must be taken when replacing the filter element. The use of a non-oil-contaminated filter element is necessary, and installation must be oil- and grease-free here, too.
5. Sufficient cleaning of oil-contaminated surfaces
If the activated carbon bed is completely saturated, all the surfaces which come into contact with the compressed air and downstream pipes are contaminated. Alongside complete replacement of the activated carbon all contaminated surfaces must be de-oiled.
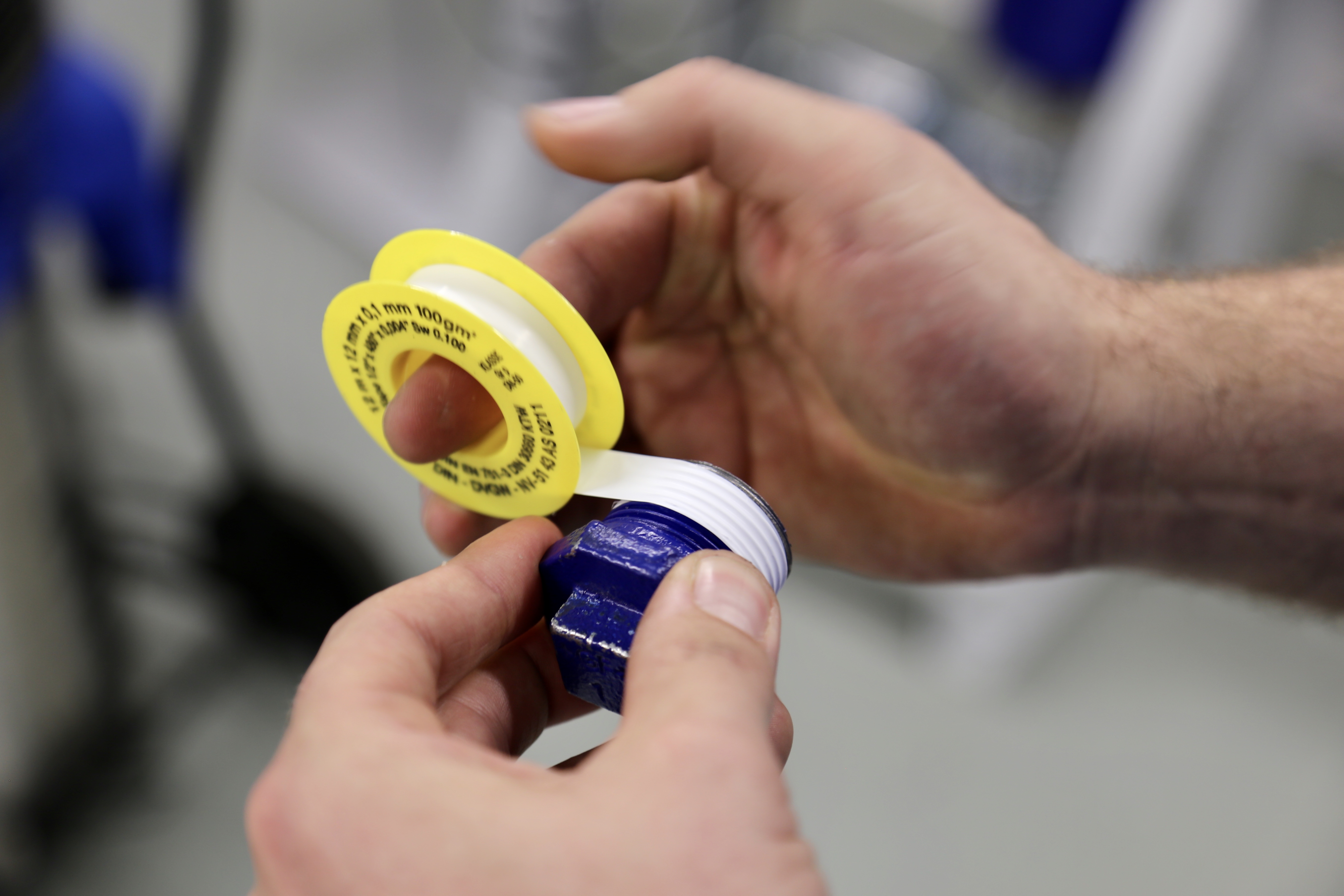
6. Further general conditions for flawless function
- Pressure build-up and pressure drop not greater than 1 bar / minute to avoid load on the activated-carbon pellets.
- Homogeneous pressure build-up/drop in the capillaries of the activated carbon and in the environment of the activated carbon (prevents abrasion, imploding and exploding of activated carbon granules)
- Avoidance of abrasion through laminar (even) flow
- Volume flow over the entire operating time from full load 100% to partial load 50%. This also includes minimum removal, e.g. during the night or at weekends
- Generally speaking, always heed the authorised operating conditions.
Quality criteria for the selection of activated carbon:
BEKO TECHNOLOGIES stands for quality. Thanks to close ties with our suppliers, we can guarantee a consistently high level of product quality. Regular meetings and professional exchange with the manufacturers of our adsorbents is a WIN-WIN situation for all involved – particularly for our customers.
Thanks to continual product development, activated carbon with ideal characteristics has been created:
Properties of the original activated carbon:
Properties of the original activated carbon:
- Outstanding adsorption properties: thanks to the optimised activation process of our activated carbons, these have a particularly large number of functional groups in the pores which can adsorb oil molecules.
- More pore volume: thanks to combined pre-drying and desorption we ensure that up to 100% of the active pore volume is available to you.
- Optimum pore structure, quantity and distribution ensure a large inner surface and better adsorption capacity.
- Homogeneous pellet sizes in cylindrical form lead to a homogeneous filling and thus to low differential pressure and consequently lower operating costs.
- Good mechanical properties and abrasion resistance guarantee low dust formation.
- Low ash and foreign matter content guarantees high product quality and structural strength, since mineral components lead to porous structure.
- Consistently high product quality thanks to stable supplier relations.
And how does the activated carbon adsorb the oil in the compressed air?
Our service for you!
Do you have any special requirements? Just contact us!
We are the only manufacturer to offer the complete portfolio and flexible technologies for the production of oil-free compressed air.
Your advantages at a glance:
- Manufacturer expertise for catalytic converters, activated-carbon adsorbers and suitable oil vapour measuring technology.
- No matter how large the volume flows, temperatures and pressures are, with our “tailor-made engineering” and own project departments we can take your particular requirements into account and offer the best customised solution for you.
- Thanks to our excellent supplier relations we offer a selection of special activated carbon and adsorbents for absorbing further pollutants alongside our standard products.
- We will be happy to provide advice on the topics of activated carbon replacement, compressed air analysis and disposal.
- More than 35 years of manufacturer expertise and special industry know-how for individual consultation on complex challenges.