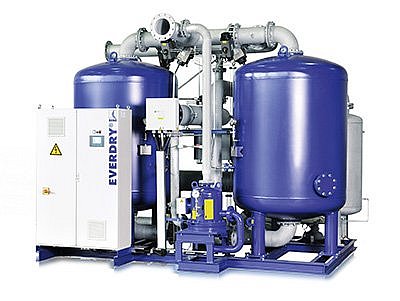
Food grade quality compressed air - Compressed-air drying with heat recovery
Large amounts of heat energy accumulate in hot-regenerating adsorption dryers, which use the compression heat (HOC) from compression for desorption of the desiccant. A dairy has illustrated how this can be meaningfully utilised for production processes in the food industry.
This wholesale dairy concentrates in butter production, butter specialities, convenience products for the end consumer as well as market-oriented products for the catering industry. The dairy is a family owned business and their product comprises of an entire range of modern dairy products: From butter to milk by-products including cheese, everyone will find something to suit their taste.
The dairy is also simultaneously a leading global supplier of lactose for the food and pharmaceutical industries. Functional dry products for the food, pharmaceutical and animal feed industries form the second core element of the company.
Milk processing is already recognised as an energy-intensive business, lactose production makes it even more so. Millions and millions of litres of liquid have to be evaporated for this every year. The Head of Energy Supply for the Dairy is responsible for the provision of steam, heat, electricity and compressed air. A combined gas and steam power plant comprising gas turbine, steam generator, steam turbine and compressor operate to satisfy the constant demand for energy in production. Back-up systems and supply routes ensure the greatest possible production safety. It goes without saying that compressed air is the focus of attention, as it is by far the most expensive energy source at the Dairy.
Decisive for the production processes is the quality of the compressed air utilised, because it has direct contact with the product. Downstream activated carbon filters additionally protect the lactose against contaminants from the intake air to ensure oil-free compression. Another requirement for the compressed air is crucial, it must be dry, and so dry that safe and reliable conveying of the powdered lactose products in silos is possible at all times. Without sticking or lump formation and without encrustations in the pipework. The cycle-shuffle conveyors utilised for this operates with an operating overpressure of 6 bar, otherwise at 3 bar. A guaranteed pressure dew point of -20 °C is therefore mandatory.
Up to now, two conventional adsorption dryers with 1,800 and 5,600 m³ respectively have been used for compressed-air drying at the dairy. However, in order to increase the existing energy-saving potential with the compressed-air drying, they decided to invest an EVERDRY HOC-F 8000 C. The heat-regenerating adsorption dryer guarantees a pressure dew point below -25 °C, operates as fully automatic and is designed for continuous operation.
The EVERDRY desiccant dryer was supplemented with an additional cooling water circuit and heat exchanger. Depending on the operating stage and work load of the desiccant dryer, a heat output of up to 400 kW can be made available from the drying process. The energy gained is utilised to preheat the boiler feed water in the desalination plant and for hot water processing.
BEKO TECHNOLOGIES installed and commissioned the dryers, it guarantees a perfect start of the new equipment. EVERDRY plants are usually completely assembled, fitted with piping and cables and inspected at the factory and then delivered to the customer as a plug-and-play solution. As the EVERDRY desiccant dryer could not exceed a certain height in the plant, the technical service of BEKO TECHNOLOGIES assembled the overhead positioned pipework on site.