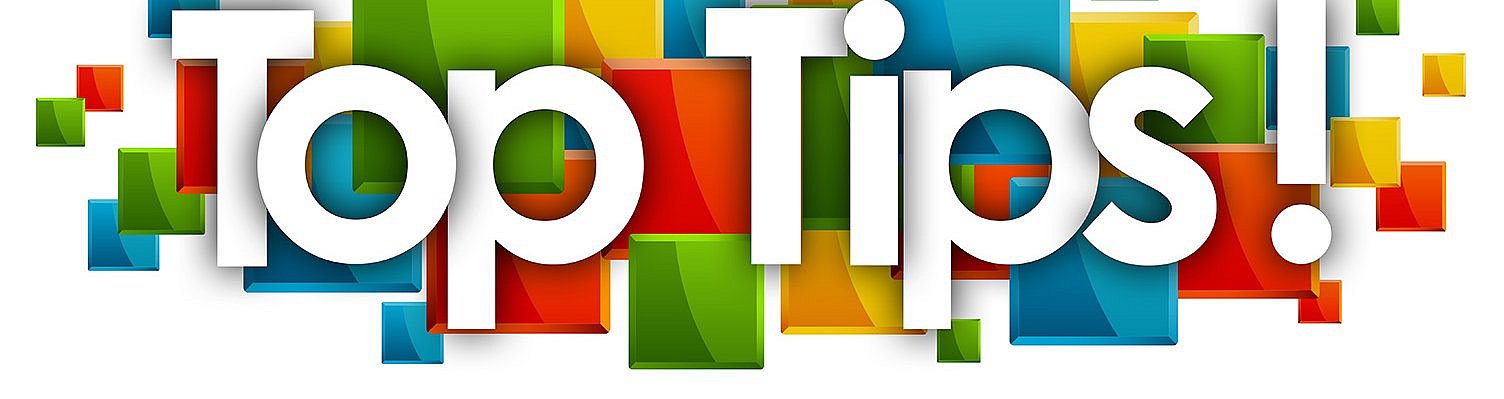
What you should consider when restarting your compressed air system
When the sudden impact of the Covid-19 outbreak hit, many manufacturing companies found the need to reduce or even halt their production. The compressed air system’s that are extensively used in many production processes were also affected by this reduction and shutdown. Most manufacturing facilities forget that when a compressed air system is temporarily shut down or are only used in a reduced capacity, when they are restarted, there could be some unpleasant surprises in store, especially when the compressed air systems are not turned off / decommissioned in the correct manor.
So, what are the risks and what preventative action can be taken.
A lot of these systems will have been shut down abruptly and without any precautions or plan. To make sure the system is fit for full production, there are a number of things that can and should be checked.
We have been releasing a top tip over the past 8 days, please see below our complete top tips for restarting your compressed air system.
"Water hammer" and oil pollution - Eliminate hazards
Temperature fluctuations cause condensation in the compressed air system. In the depressions of the piping and the containers, such as the compressed air tank or the filter, larger quantities of water are deposited as so-called compressed air condensate during longer shutdowns. When the system is restarted, it shoots through the system as "splash water" and such a "water hammer" can lead to considerable problems such as burst filters. In order to prevent this, the system should be closely observed during start-up. Anyone who has installed electronically level-controlled condensate drains is on the safe side in this case.
In addition, during the shutdown phase, oil-containing lubricants can collect on the surface in valves, fittings, etc., which are then carried along by the air flow and lead to contamination and oil contamination.
Bonded filter mats and overloading due to oil foam
Possibly the suction filter mat in the compressor is stuck together with the suction filter mat, which has not been permeated by air for a long time. At present, the situation is exacerbated by the fact that the ambient air is heavily polluted with pollen, which is deposited in front of the intake shafts. The increased flow resistance not only increases energy consumption, but can also lead to a higher oil vapour content in the compressed air. Before commissioning, the filter mats of compressors should therefore be checked and, if necessary, cleaned. The same applies to the surroundings of the intake shafts.
With decreasing load, the switching cycles of the compressors increase. With each load change, the internal pressure in the compressor relaxes, which can cause foam to form in the oil separator. If the switching times are reduced, there is not enough time for the foam to dissolve. This can result in the oil separator element being enveloped by foam, additional oil reaching the clean side and causing the residual oil content to increase significantly. The subsequent treatment can be overloaded to such an extent that the desired compressed air quality is no longer achieved.
Compressed air filtration requires minimum volume flow
In many compressed air systems, a cyclone separator follows directly behind the compressor to separate large quantities of water. A minimum volume flow is a prerequisite for the full functionality of such a unit. If the cyclone separator fails, the other components of the compressed air treatment system are overtaxed with the water separation.
Downtimes cause oil in the filter medium to thicken, and because of the clogged filter pores, the differential pressure can rise so much that cracks appear and the material bursts open. The filter cartridges should be checked and, if necessary, replaced before restarting.
In addition, the filters have significantly less separation efficiency at low loads. If the volume flow is too low, filters of inferior quality may even fail completely. High-quality filters achieve their performance already from 20% of the nominal volume flow.
Longer downtimes of the compressed air system also create ideal conditions for bacteria and germs, which are carried along uncontrollably from the filters during start-up. Here, online sterilisation of the affected plant sections is recommended, for which no removal of components is necessary. Alternatively, contaminated filter elements can be re-sterilized in an autoclave.
Reduced heat exchange in the dryers
Even in compressed air dryers, thickened oil sticks to the surface during longer standstill periods and the heat exchange is impaired. The narrowed flow channels increase the differential pressure, possibly to the point of overloading the compressed air system. Flushing the heat exchangers with oil and grease dissolving cleaning agents provides a remedy.
Adsorption dryers use a granular desiccant and are always dependent on a certain flow velocity. If the flow rate is too low, only partial total adsorption occurs and the compressed air is no longer sufficiently dehumidified. Such undesirable effects can be detected with suitable measuring technology.
Compressed air de-oiling suffers from moisture and lack of flow
Furthermore, a plant shutdown may have an effect on the de-oiling of the compressed air with activated carbon adsorbers. If the activated carbon is saturated by condensation water, it cannot absorb oil when restarted. Surge water (see above) also causes this problem. Before restarting, companies should check the components for moisture and use appropriate measuring equipment.
Activated carbon adsorbers and adsorption dryers contain granules and therefore generally require a minimum flow velocity for reliable deoiling.
Fixed mechanics in steam traps
In steam traps, the mechanics of the float traps can stick in the open or closed position. This leads to reduced performance or permanent discharge and thus to damage to other system components. It is advisable to replace the float traps or, even better, to use so-called zero-loss traps that operate electronically.
Steam traps with time-controlled solenoid valves are frequently shut down during downtimes for energy-saving reasons. When restarting production, their activation must not be forgotten.
The following also applies to these components: If steam traps are not used for a long time, microorganisms form which, in the worst case, are carried along uncontrolled during start-up.
Oil-water separator can overflow
If the condensate remains in the oil-water separator for a longer period of time, slime and blockages will occur. When restarting, the solid oil layers impede the function to the point of overflowing and thus contamination of the entire compressed air system. Before starting, the oil-water separator should therefore be cleaned and, if necessary, the filter should be replaced.
Take measured values seriously in case of partial load
If a compressed air system is initially only partially utilised after shutdown, this poses a risk. It is possible that some components of the treatment system may not work properly because the volume flow is too low, which in turn leads to the overload of other components. In such cases, apparently extreme measured values are obtained, which should not be regarded as errors in the measuring technology under any circumstances. Instead, a functional check of the entire compressed air system must then be carried out.