Compressed air processing in crystal glass production
Industry: | Glass production |
Customer/Location/Year: | Stölzle Lausitz, Weißwasser (Germany), 2013 |
Use of compressed air: | In production |
Installed products: | DRYPOINT RA, BEKOMAT |
Heavenly brilliance and hellish fire It is rare that one can see both inter-twined as closely as in glass drawing, the mechanical production of high-quality table glass. Stölzle Lausitz GmbH from Weißwasser in Saxony is recognized as one of the leading glassworks in Germany. Dry compressed air is the most important energy element in their manufacturing processes.
The flames hiss from the nozzles of the powerful-looking machinery in the spacious factory buildings at Stölzle with far more than 1100 degrees Centi-grade. One could almost imagine being faced with dragons made of steel – and one correspondingly keeps a respectful distance when visiting for the first time. But curiosity is always present and one wants to know what glitters and shimmers so auspiciously in the "phantom" within these monsters: purest, impressively brilliant crystal glass. Formed into elegant wine and sparkling wine glasses. Faultless beauty, born in fire
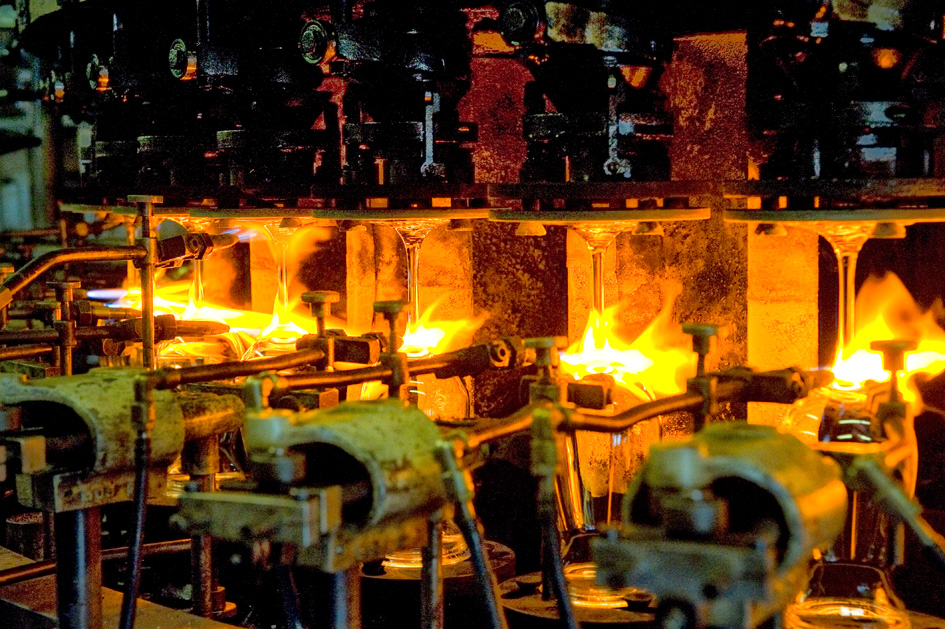
Whilst standing there and considering this flaming genesis, the Stölzle company slogan of "born in fire" becomes a truly sensual experience. Utilizing the drawing process or the also associated welding technique enables Stölzle Lausitz to produce glasses which, due to their smooth, flowing transition from stem to goblet and outstanding glass distribution come very close to the characteristics of mouth-blown glasses. They also have the additional advantage of being break and dishwasher resistant as well as a beneficial price-performance relation.
The glasses are perfectly coordinated for the character of various beverages. Wine, sparkling wine, spirits and cocktails. Recipients are mostly hotel owners, gastronomy, the beverages industry as well as demanding viticulturists. Stölzle Lausitz markets up to 35 million glasses in over 45 countries around the world annually.
Regular aspiration with compressed air
The art of glass manufacturing and refining has been maintained and developed in Lusatia for more than 500 years. The first certified reference about a glasswork dates back as far as 1433. Around 1930, Lusatia became the largest glass producing region in Europe and the "Glashüttenwerke Weißwasser AG" - the predecessor of today's Stölzle Lausitz GmbH - became the largest goblet producing company in Germany.
Most important in the production process is the aspiration of the fire-breathing dragon with dry compressed air. Compressed air is the most important means of production and the most important energy element. It´s used for controlling the systems and in uncountable compressed air cylinders as well as actuating valves.
What is hereby decisive is the induction of constant and reliable dry compressed air. If the moisture level is too high, then emulsions will result in the valves of the machines within a very short time – therefore slime build up and, consequently, standstill.
An Achilles heel of the compressed air processing at Stölzle: the refrigeration dryers. The dryers had to overcome a particular problem. The problem also had something to do with the unusually high temperatures.
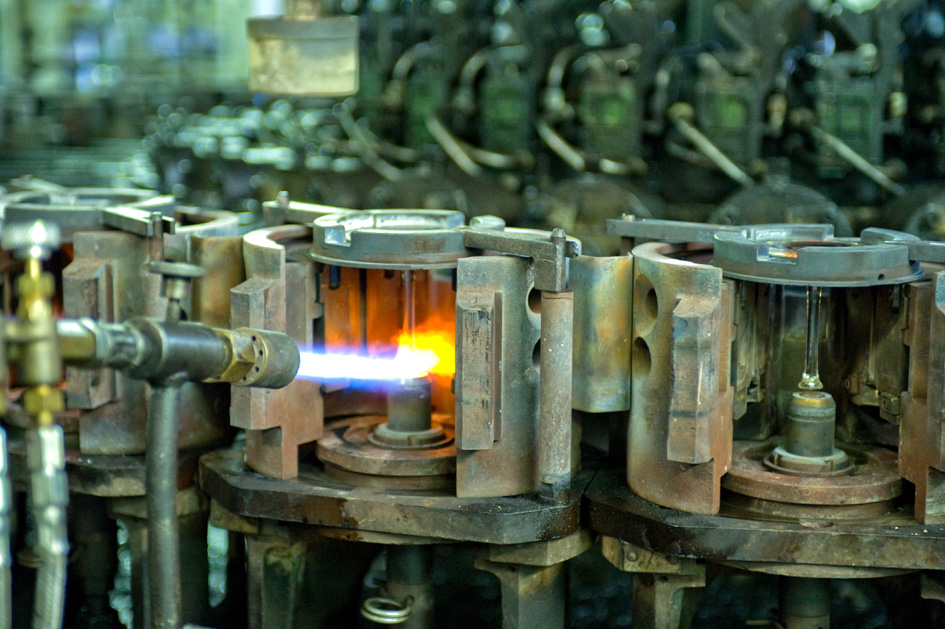
Refrigeration dryer as an Achilles heel
One of the compressors which is utilized in the factory produces exceptionally hot compressed air due to its design. The refrigeration dryer downstream of this compressor could not always counteract the compressed air approaching it, which often reached temperatures up to 63 degrees. This often turned into a balancing act, especially during the hot Summer months. The outlet temperature downstream of the overworked refrigeration dryer was often higher than the subsequent compressed air logistics would have preferred.
This was executed via an extensive pipework system from the compressor stations to the withdrawal positions in the production halls. Often also via longer routes in external areas and through the basement in the factory halls whereby the pipework system additionally branched off. The compressed air therefore had to pass through numerous temperature zones from the compressor to the destination and condensate forming routes. The risk that compressed air with too high humidity levels would arrive at the machinery increased accordingly. Which refrigeration dryer would be able to resist the extremely high compressed air temperatures from the overheated compressors?
Good experience tipped the scales
The Saxony glassworks located a solution by contacting the German compressed air system provider BEKO TECHNOLOGIES GmbH. One had already had rewarding, excellent experience with this technology at numerous other positions in the factory for many years. For example with ÖWAMAT oil-water separating systems, with CLEARPOINT compressed-air filters and BEKOMAT condensate separators.
The compressed air specialist from Neuss on the Rhine should also have an answer for the heated situation with refrigeration drying at Stölzle: compressed air refrigeration dryer DRYPOINT RA.
In the DRYPOINT RA eco refrigeration dryer, the compressed-air drying is executed by a counterflow process via an optimised heat exchange through-out the entire process path, The air flows in a downward aligned movement without any unfavourable diversions. The generously dimensioned counter-flow heat exchanger unit, which comprises an air-air and an air-refrigerant agent heat exchanger cools the compressed air down to a temperature of around three degrees Centigrade, whereby the installation size of the heat ex-changers not only promote a particularly effective cooling, but rather also minimising flow resistance to an absolute minimum.
From the initial startup, the new drying system clearly demonstrated that it could easily cope with the high compressed air inlet temperatures. Even the hot Summer days shortly after installation caused no restrictions in the dryer performance. Performance was however not everything; the aspects of effectiveness and economics were also decisive.
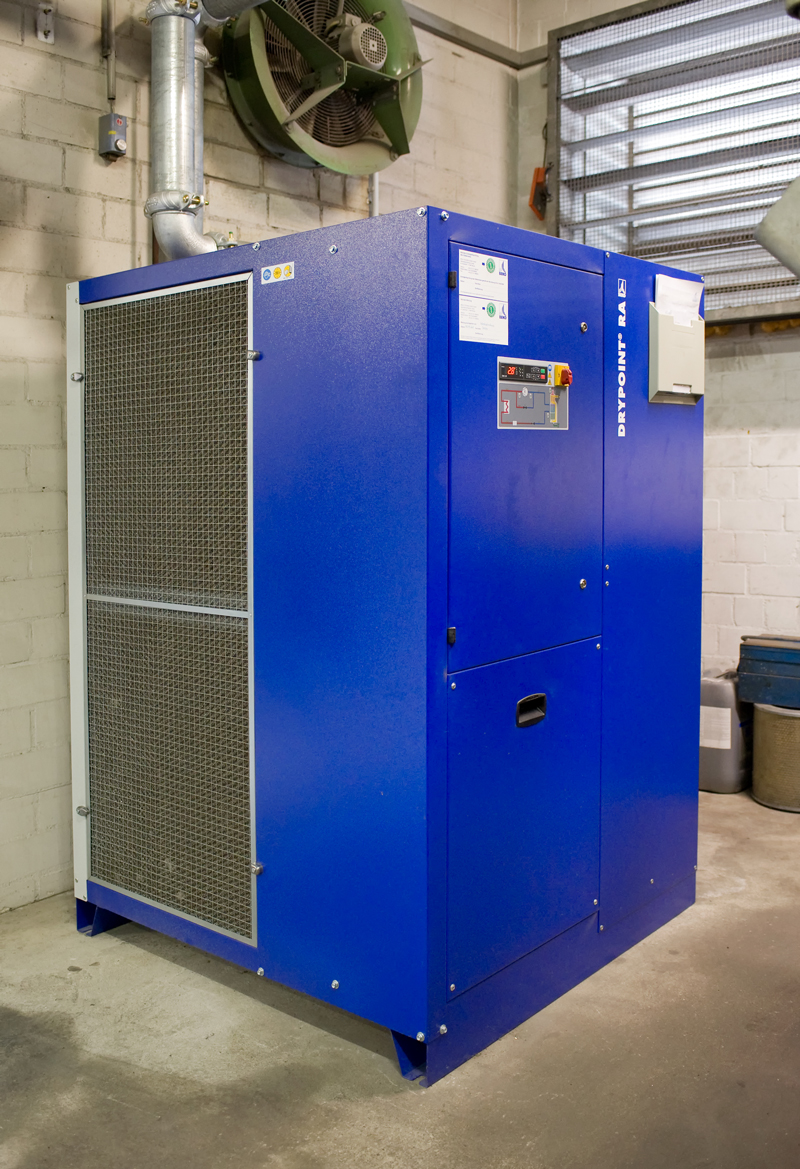
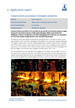