Compressed-air processing on hybrid locomotives
Industry: | Transport, Locomotives |
Customer/Location/Year: | ALSTOM, Stendal (Germany), 2013 |
Use of compressed air: | Control air, process air |
Installed products: | CLEARPOINT, DRYPOINT M, BEKOMAT, ÖWAMAT |
A trendy concept in automobile engineering, and an already proven technology on rails: the hybrid drive. The combination of a diesel generator and a battery on state-of-the-art locomotives leads to fuel savings of up to 50%. What is always on board is a complex "mobile" compressed-air processing system for the operation of the hydraulic brakes.
If model railroaders could dream themselves to a place, Stendal near Magdeburg would have the best chances to be chosen, since here, on grounds and in halls full of tradition, the steels giants that get the rail traffic rolling have been developed for decades: locomotives from ALSTOM. Amongst other models the shunting locomotive which, at present, is possibly the smartest and most economical of its kind: a hybrid locomotive with a combined diesel generator and a battery.
The globally positioned French ALSTOM group is the worldwide leader in the construction of plants and products for the generation of power, energy transmission, and rail infrastructure. The group constructs the fastest train, the world's highest-capacity automated subway and, in the German city of Stendal, the ground-breaking hybrid locomotive.
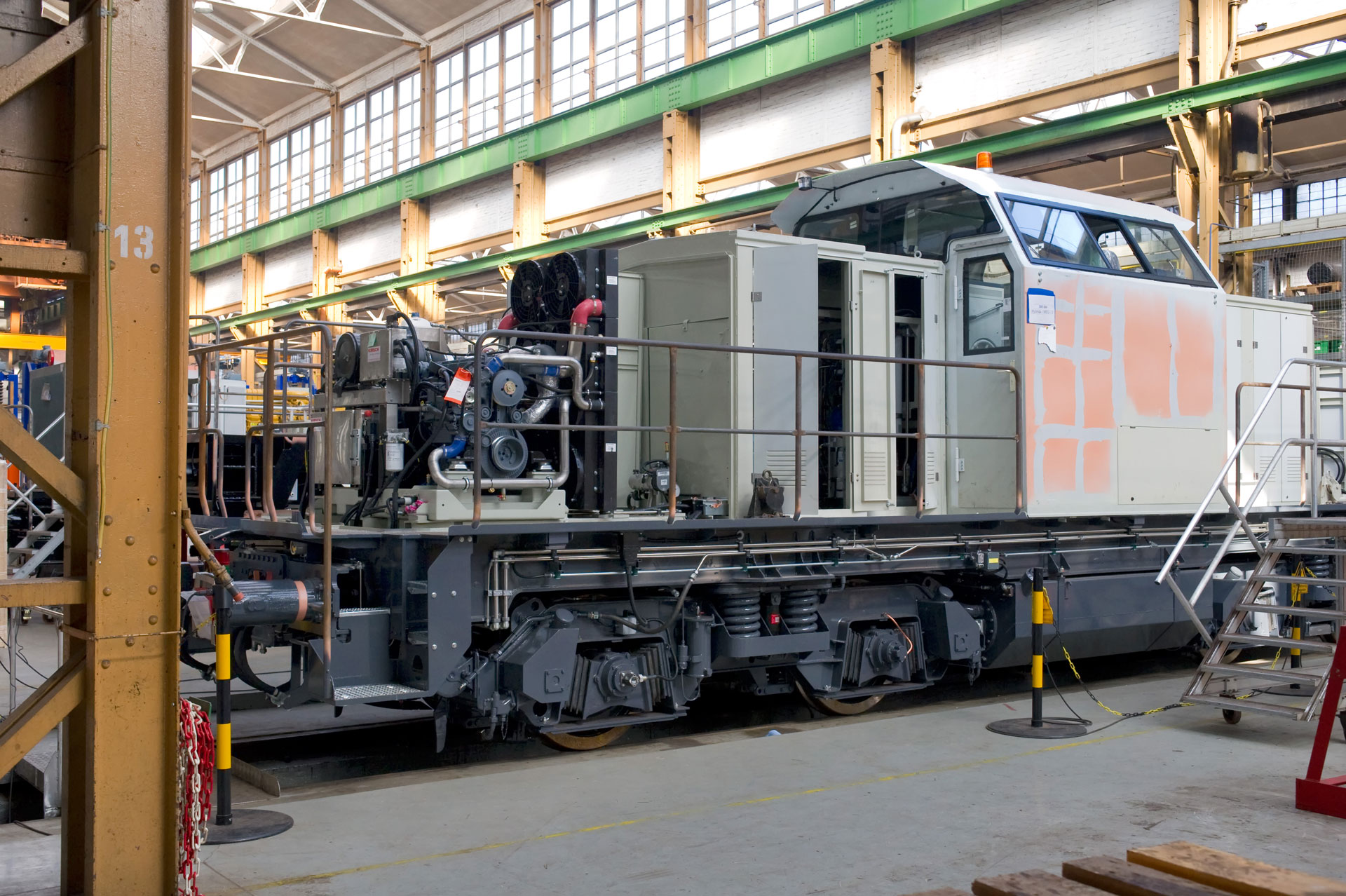
Here, at the site of the ALSTOM Locomotive Service - which is a joint enterprise with the Deutsche Bahn AG – the concept of the combined drive concept took concrete shape already in 2006. In that year, the ALSTOM engineers brought the first operable prototype of the hybrid shunting locomotive onto the rails. It was constructed on the chassis frame of the proven V100 locomotive with its two bogies. In addition to the typical diesel-electric generator, a large battery was installed on board as an energy storage device – as well as a fully newly developed system for the processing of compressed air for the brake systems of the locomotive and of the coupled wagons.
From the prototype to series-production readiness
At ALSTOM in Stendal, they are proud of their "steelhorses" – above all, for their performance and economic efficiency. The principle: The hybrid version of the shunting locomotive is equipped with a 230-kW diesel generator and a battery. With this design, it is particularly suitable for the heavy shunting operation. A very economical and environmentally friendly diesel generator charges the battery and is also capable of directly driving the electric motor for peak loads. In the event of a partial load, the locomotive is operated via battery and saves 30 to 50 per cent of diesel in this variant compared to conventional 700-kW shunting locomotives. The muscular hybrid locomotive with its 220 kN starting tractive effort and up to 60 km/h top speed rolls on four axes.
During the shunting operation with its numerous load alterations and direction changes, the brake system of a locomotive is particularly challenged. Correspondingly, the performance and stability of compressed-air processing was the greatest concern already in the earliest development phase of the hybrids.
Compressed-air processing directly on board
The compressed-air production and processing for the brake system of the machine and the coupled wagons takes place fully independently on board every locomotive, in an internal "mobile" compressed-air station directly behind the driver's cabin. Except for the housing, it is installed "in the open", meaning that it is continuously exposed to weather and climatic conditions, e.g. during the shunting operation, when the temperature falls below zero, and in the scorching heat of summer both during its employment in Nordic regions and in sultry, hot countries of the southern hemisphere or in Asia. Enormous challenges, above all for the technical equipment of compressed-air processing – and no room for uncertain concepts.
Against this background, ALSTOM in Stendal took a specialist for this field on board already during the project planning phase: the German compressed-air system provider BEKO TECHNOLOGIES GmbH from Neuss.
This company sent its engineers from the Rhine to the Elbe to receive one of the most versatile specification documents thus far in the history of project development. It quickly became clear that, in addition to the combination of existing processing components, completely new device versions also had to be developed – above all with a view to oil-water separation.
A comprehensive specification document for the compressed-air engineers
Right from the start, Beko Technologies, accompanied the system development for the ALSTOM hybrid locomotives. Another challenge: During the shunting operation, the locomotives sometimes hold one position over a longer period of time. At temperatures below zero, this involves the risk of freezing condensate in the compressed-air processing system. So BEKO TECHNOLOGIES had to provide all the relevant components and lines with a heating system. In addition, all the installed condensate drains are connected with the control of the compressor. Through this, residual condensate that is still in the system at a possible breakdown or deactivation of the locomotive's electrics, is discharged automatically and in a remote-controlled manner before it can freeze.
Via the BEKOMAT condensate drains, it is directly led into an ÖWAMAT condensate conditioner for an oil-water separation. These devices that are developed by Beko Technologies take into consideration the environmental protection and water conservation concerns and follow the holistic approach of sustainability.
Their cartridge technology is particularly user-friendly. It allows the fast re-placement of the filter and facilitates low-waste disposal. In addition, the filter service lives are by far longer than for conventional activated-carbon filters. Moreover, extended maintenance intervals result from the high product quality – which was one of ALSTOM's central requirements for the "mobile", particularly tough employment on the locomotives. Especially for this, Beko Technologies equips the ÖWAMAT oil-water separators with a corrosion-free and extra robust stainless-steel housing.
A complete system in the narrowest space
The oil-water separator, however, is only the final stage of the compressed-air processing system of the hybrid locomotives which is designed in a form-fit manner. The CLEARPOINT water separator with the first condensate drain is installed directly behind the screw compressor. Every millimeter counts with these restricted space resources on the locomotive. It only occupies the area of a small garden toolshed and is only half as high.
Anyhow, there is enough space for an ultrafine filter with a condensate drain near the compressor and water separator, as well as even for two DRYPOINT M membrane dryers from Beko Technologies. One of them is a "plus" version with an integrated Nano filter. The DRYPOINT M membrane dryers are based upon the "Twist 60" technology which was developed by Beko Technologies: the membrane element consists of intersecting layers of hollow fibres which are arranged around an internal core pipe. This structure allows for the highly efficient utilization of physical mechanisms of action and enables the drying of compressed air at low energy consumption. For the drying process, a portion of compressed air is continuously diverted in the outlet area of the membrane element and is used as re-generation or purge air when atmospherically expanded.
When it all works out smoothly just like on rails
Exactly these strong points of the DRYPOINT M compressed-air membrane dryer are indispensable for the employment on the hybrid locomotive: absolute functional safety, highest reliability, and immediate availability of dry compressed air even in a discontinuous operation mode, and freedom from maintenance and wear, as there are no moving parts. After all, it’s impossible to have a service technician for the compressed-air system on board of every locomotive. The system is due to run and in a robust, faultless manner. Until the present, this is exactly the case on all of ALSTOM´s hybrid locomotives.
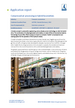