Condensate technology for turbo compressors
Industry: | Metal, steel |
Customer/Location/Year: | ThyssenKrupp Steel Europe, Duisburg, (Germany), 2011 |
Use of compressed air: | In production |
Installed products: | BEKOMAT |
The compressed-air system at the central Duisburg site of ThyssenKrupp Steel Europe AG extends over more than 10 kilometers. A complex network which needs to be ventilated reliably and powerfully. High-capacity turbo compressors which are supervised with diligence take care of this.
Nothing is small here. Those who dive into the spacious Duisburg smelting plant area of ThyssenKrupp Steel Europe AG must prepare themselves for huge impressions in every respect. The traditional site of the steel producer had a period of 120 years to reach its present-day dimensions and significance. Currently, it is the biggest site of the corporate group in Germany in terms of workforce numbers.
ThyssenKrupp Steel Europe focuses on the fast-growing segment of high-quality flat steel. The range of services extends from material solutions, product-specific processing and comprehensive services to finished elements and units made of steel. By concentrating metallurgy and most of the hot strip production in Duisburg, a site concept has been created on the Rhine which is unique in Europe. It is topped off by high-capacity coldrolling and coating activities.
As is the case in nearly all industrial processes, compressed air belongs to the important energy carriers here. Simultaneously, it is the central element of process safety at ThyssenKrupp Steel Europe AG. The attention paid to com-pressed air and its processing is correspondingly great.
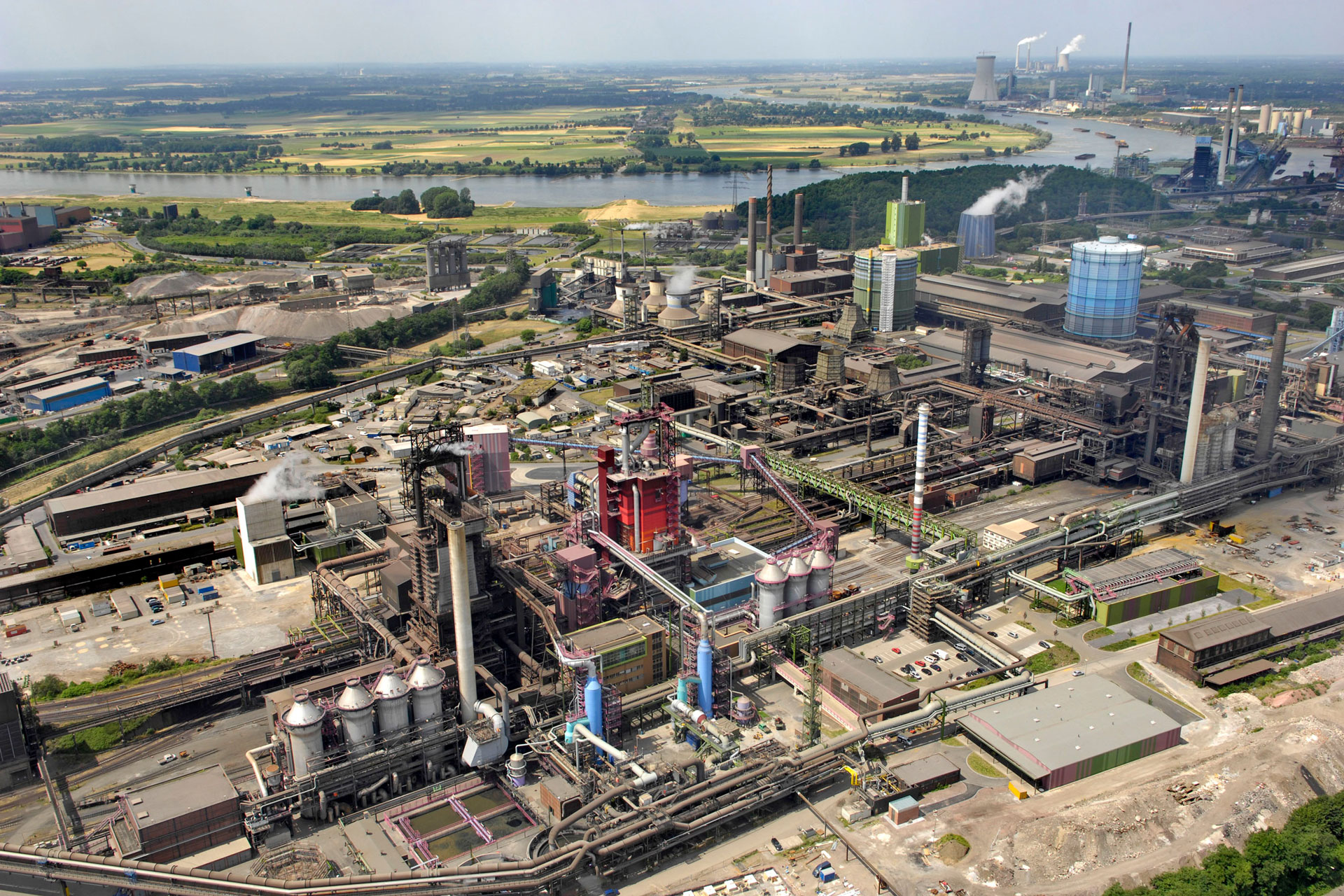
No small matter
A large compressor hall in the core of the factory accommodates part of the aggregates for the generation and processing of compressed air. Among them three turbo compressors with a compressor capacity of 25,000 m³ per hour each. This volume of 75,000 m³ all in all contributes to ensuring the functioning of countless systems everywhere in the production structure. For example, for the triggering of valves in the rolling mill, to mention only one possible field. It is easy to understand how far-reaching the consequences of malfunctions or even breakdowns in such plant sections could be for the entire manufacturing process. If one of the compressors goes out of service, this may lead to difficulties.
Until mid-2010, it could have been not only difficult but truly problematic in one specific case: in the separation of condensate. Here, the high-capacity turbo compressors make special demands: each of the four compressor stages of an aggregate requires internal condensate drainage. Until then, condensate drainage was implemented via a manually adjusted drainage which was supervised by manual and visual checks.
The mechanical condensate separators employed at the turbo compressors could not be integrated into the electronic monitoring system of the com-pressed-air processing. Therefore, connection with the central control room was impossible. In view of the demanding quality assurance concept at ThyssenKrupp Steel Europe AG, this situation was no longer acceptable. The failure of a separator at only one of the four compressor stages could lead to a temporary breakdown of the compressor. No compressed-air technology provider seemed to be able to equip such potent compressing plants with capacitive, electronically supervisable condensate separators in a process-reliable manner.
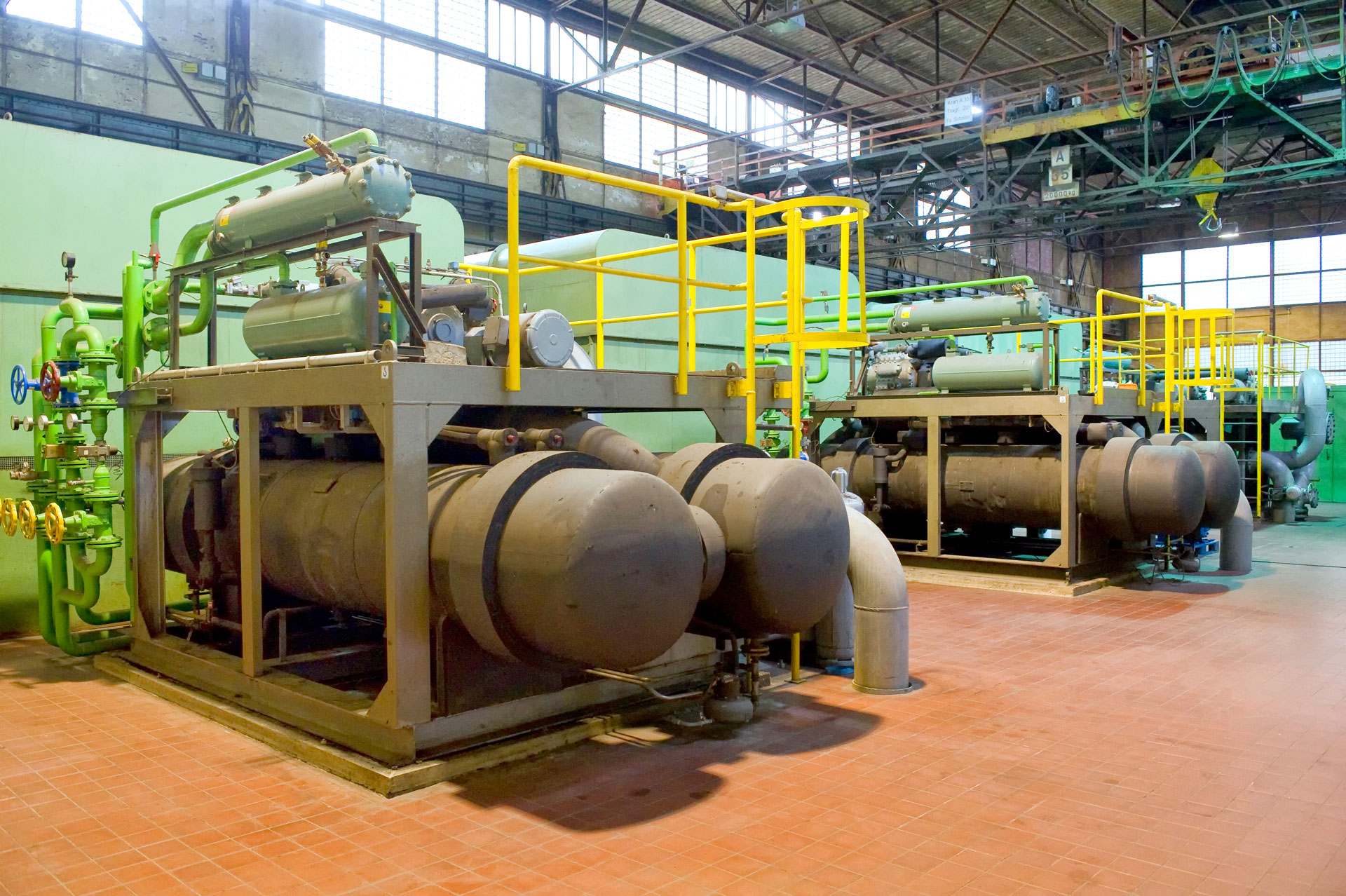
Electronically level-controlled separation
Finally, the discussion with the compressed-air system provider who, in 1982, brought the electronically level-controlled condensate drain to the market, the German BEKO TECHNOLOGIES GmbH with its headquarters in Neuss on the Rhine, brought relief to this pressing situation. Over many years at the beginning, the company concentrated on only this product, the BEKOMAT, and brought it to perfection also for difficult application purposes.
Until the launch of the BEKOMAT, only two main types of construction were known: the mechanical condensate float drain and the electric solenoid valve condensate drain. In the past as well as in the present, these functions according to the same principle. And with the same difficulties conditional on the technology.
A mechanical float drain, for example, must always be specifically adjusted to the composition of the accumulating condensate. This often constitutes a hindrance to a flexible use of the compressed-air plant. In addition, it requires very high maintenance efforts and is susceptible to faults when the condensate is contaminated, clotted or resinified.
Time-controlled solenoid valves are far more operationally reliable than float drains. This does, however, not mean that they are also automatically more efficient because, in simple terms, expensive energy is first invested in the compressor to generate compressed air. Afterwards, several holes are opened at regular intervals (time-controlled) within the line system and air is blown off, only to discharge a little bit of condensate. The valve opens no matter whether condensate has accumulated. A counterproductive behavior from the economic point of view.
The electronically level-controlled condensate drain avoids these disadvantages of current techniques, and simultaneously offers a better performance and helps to achieve higher profitability in compressed-air processing.
The operating principle
In principle, a BEKOMAT acts in a level-controlled manner like a float but without a mobile element susceptible to faults in the condensate receiver. This task is performed by a capacitive sensor. It reacts to any type of condensate and is dirt-resistant.
This capacitive level detection ensures discharge adjusted to the actual condensate accumulation without compressed-air losses. Energy is saved and no emulsion is produced. Drainage cross-sections with large dimensions guarantee safe drainage even of strongly contaminated condensates.
But the intelligent control unit does not only ensure the condensate drainage. At the same time, it serves to fully automatically monitor the condition of the device. Failures are indicated via LEDs by the drain and can also be transmitted as a fault indication to a central control point via a potentialfree contact.
With these characteristics, the BEKOMAT condensate drains corresponded exactly to the requirement profile of ThyssenKrupp Steel Europe AG in Duisburg. Above all, the unproblematic integration into the existing automatic monitoring and control system was convincing.
Only five weeks
In early summer 2010, the specialists from BEKO TECHNOLOGIES installed the first four BEKOMAT devices with different sizes at one of the turbo compressors in close cooperation with the technology team from ThyssenKrupp Steel Europe. Only when this configuration functioned perfectly in every detail were the other two aggregates included.
But this did not take a lot of time: within less than five weeks between the first prototype configuration and the complete "restart", the entire condensate separation was process-reliably modernized. Further electronically level-controlled BEKOMAT devices are installed at different refrigeration dryers of the compressed-air system.
With the process reliability increased in this manner, another module is added to the strict safety concept at ThyssenKrupp Steel Europe and future developments in the compressed-air system should no longer be a worry to the persons in charge.
All variants of the BEKOMAT are adjusted over and again to the performance specifications of the commercial compressors and dryers. These change continuously and follow the performance requirements of industrial compressed-air processing.
Future-proof technology
At BEKO TECHNOLOGIES, optimum profitability has obviously been achieved with the recently introduced fifth generation of the series, models 31 and 32. These devices boast a completely new construction principle for electronically level-controlled condensate drains, which has considerable advantages regarding maintenance.
They are subdivided into only two modules: the service unit, which unites all non-wearing and maintenance-free components in its extremely corrosion-resistant aluminum housing, and the electronic control and sensor unit, which only needs to be installed once. Both units are coupled via a practical quick connector.
This construction allows the simple replacement of all maintenance and utilization-relevant parts through the fast exchange of the service unit alone. No tools are required to separate and connect both modules – a simple hand movement suffices.
Even if this solution is currently not employed in plants with the immense com-pressed-air volume required at ThyssenKrupp Steel Europe AG, it is good evidence for the Duisburg company of the innovative spirit of its system provider.
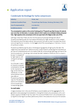