Optimising the compressed air system at Umbria Filler
Industry: | Chemical |
Customer/Location/Year: | Umbria Filler, Nocera Umbra (Italy), 2017 |
Use of compressed air: | process air |
Installed products: | BEKOSPLIT 13, METPOINT BDL, CLEARPOINT 3eco |
Companies in today´s chemical industry are not only under pressure to produce efficiently, they must also fulfil quality requirements and sustainability requirements. By obtaining voluntary seals, stamps and certificates, companies are not only able to score points with their customers and partners, but also often benefit from direct savings themselves. This was also the case at the Italian company Umbria Filler S.r.l., a member of the Moccia Group, which has been producing fillers from natural or coated calcium carbonate for tiles, rubber, plastics, but also for the construction and automotive sectors for over 40 years.
Optimising “quality, health, environment and energy consumption” has always been Umbria Filler's guiding principle and, in recent years, they have implemented several measures for environmentally friendly and energy-efficient production. The Italian branch of the compressed air expert BEKO TECHNOLOGIES from Neuss was the partner and consultant in this matter.
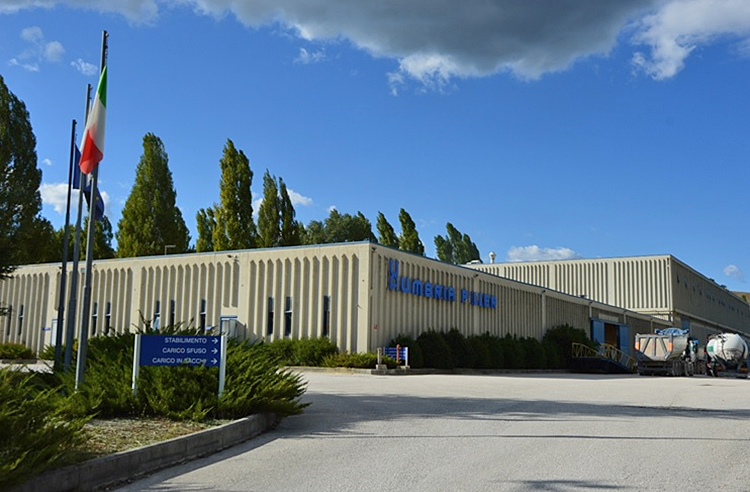
Clean condensate increases environmental friendliness in production
Umbria Filler initially became aware of BEKO TECHNOLOGIES five years ago, when the compressor department was faced with the problem for disposal of condensation water from the compressed air system. The oil-lubricated compressors contaminated the compressed air and condensate. The aqueous emulsions with oils dispersed in water had to be previously disposed of as hazardous waste at considerable cost. BEKO TECHNOLOGIES were able to create a solution for this with the installation of the BEKOSPLIT 13 emulsion splitting plant. Water-insoluble organic contaminants such as oils and solid impurities, which cannot be removed by purely physical gravitational separation alone, are removed in this plant by adding a special reaction release agent. The highly effective agent encapsulates the dirt and oil particles and filters them out of the condensate as macroflakes. The discharged water can subsequently be routed into the wastewater sewer system as uncontaminated.
“Today the quantity of oil and hydrocarbon particles in the condensation water of the compressors remains below the required limits, as shown by the environmental certification process pursuant to ISO 14001, which we regularly have to undergo”, says Luca Frezzini, Managing Director of Umbria Filler.
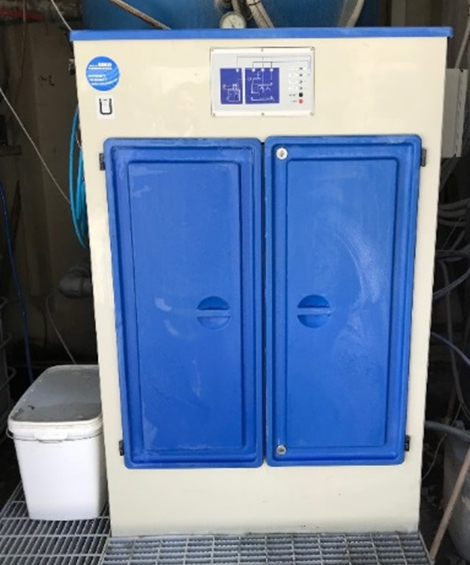
Increasing energy efficiency
When Umbria Filler decided to apply for ISO 50001 energy certification back in 2017, which analyses the energy consumption of every company department, the company was once again faced with a challenge: The energy consumption of the compressor section was disproportionately high in relation to production reality. The total of four compressors utilised, one equipped with inverter technology and three of the older generation, together accounted for twelve percent of Umbria Filler's energy consumption. “Such consumption was no longer tolerable for us. In view of the positive, previous precedents, we once again turned to BEKO TECHNOLOGIES to solve the problem”, reports Frezzini.
In the initial stage, BEKO TECHNOLOGIES analysed the relationship between generated compressed air and power consumption. The analysis indicated that it would be sufficient for production requirements to operate just one compressor with the latest inverter technology in order to cover 80 to 85 percent of the company's requirements. The plant was subsequently modified accordingly so that just one compressor is in operation around the clock today, and a second compressor is integrated for the remaining 15 to 20 percent as and when required. “It is similar to the case for certain new-generation car engines: These only utilise part of the available cylinders, depending on requirements, thereby reducing fuel consumption and environmental pollution”, explains Frezzini.
Comprehensive, gap-free compressed air system monitoring
In order to increase control via the intervention logic of the compressors, BEKO TECHNOLOGIES installed probes for recording pressure and flow through rate in the second stage. The activity of the compressors and the relative demand for compressed air are measured simultaneously in this way. Collected data is then sent to the METPOINT BDL data logger, which measures the values regularly, makes them available in the company network and sends them to the programmable logic controller (PLC). The PLC then controls the switching on and switching off for the compressors to precisely cover the compressed air demand while still keeping energy consumption as low as possible. The additional METPOINT SW 201 software enables the system and plant data to be continuously monitored and processed. Umbria Filler staff therefore have an up-to-date overview and control over the efficiency and work load of the compressed air system at all times.
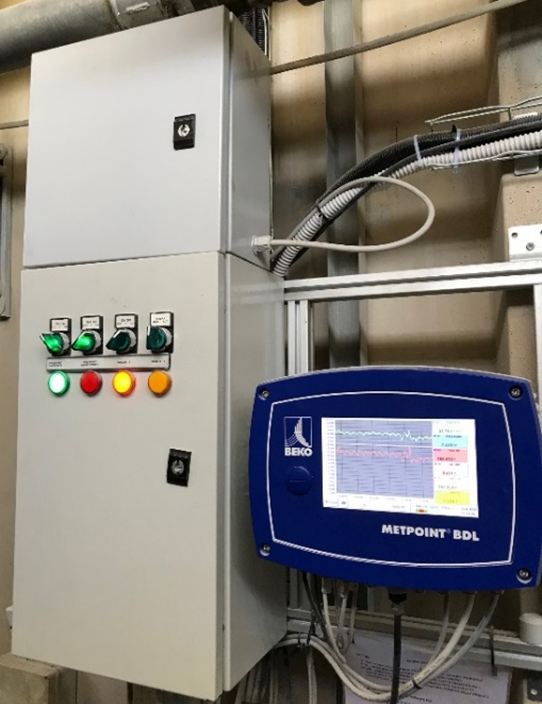
Reduction in differential pressure
Pressure loss in the plant could be simultaneously reduced by approx. one bar by building in the CLEARPOINT 3eco filter. Utilising a special material (mesh) and manufacturing technologies, which are characterised by a combination of a large filter surface and high filter bed depth as well as a flow-optimised, corrosion-protected housing construction, the CLEARPOINT 3eco achieves higher, improved quality compressed air at reduced operating costs. “The significantly lower pressure drop provides us with a much simpler and less energy-intensive working pressure threshold for the motors”, says Frezzini.
The project at a glance:
- Measures: Analysis of the compressed air system by BEKO TECHNOLOGIES and installation of measuring technology and compressed air filters
- Result: Energy certification pursuant to ISO 50001 drastically reduces power consumption
- Amortisation of the investments by means of considerable savings is anticipated in only eight to ten months.
Numerous regular certifications - ISO 9001, which analyses management and quality systems; ISO 14001, which certifies environmental certification, and finally ISO 50001, which certifies the correct procedure for the use of energy - indicate that Umbria Filler is consistently pursuing its objective of achieving the maximum targets in terms of product quality, health in the work environment, environmental protection and energy saving.
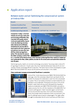