Compressed-air drying in gypsum processing
Industry: | Building material |
Customer/Location/Year: | Remondis, Lünen (Germany), 2013 |
Use of compressed air: | In production |
Installed products: | EVERDRY |
Humidity is the worst enemy of the 432 fabric filter hoses in fluidized-bed kiln 7 of Remondis Production GmbH at the Lippewerk factory in the Westphalian town of Lünen. It serves to calcinate gypsum which, by nature, is an extremely hydrophilic material. With a heat-regenerated adsorption dryer for the compressed cleaning air of the fabric filters, the disastrous bonding of water with gypsum dust in the filter cloth is now prevented. But before, a completely different solution was envisaged.
Remondis is one of the largest water and environmental service enterprises worldwide, with more than 500 branches in 26 countries on three continents. The main strengths of the group are the supply and processing of water, the recovering of raw materials from waste, the development of recycling products and the provision of alternative energy sources. In another business segment, gypsums from flue-gas treatment and industrial processes are processed into top-grade gypsum binders.
For this, Remondis moves huge amounts of substances which can be recirculated as secondary material into the economic cycle. 1,200 employees work at the Remondis headquarters in Lünen alone. With a surface area of 230 hectares, it is the largest center for industrial recycling management in Europe. The focal points are the recovery of raw materials, the production of primary matters, special products and industrial goods, as well as the generation of energy.
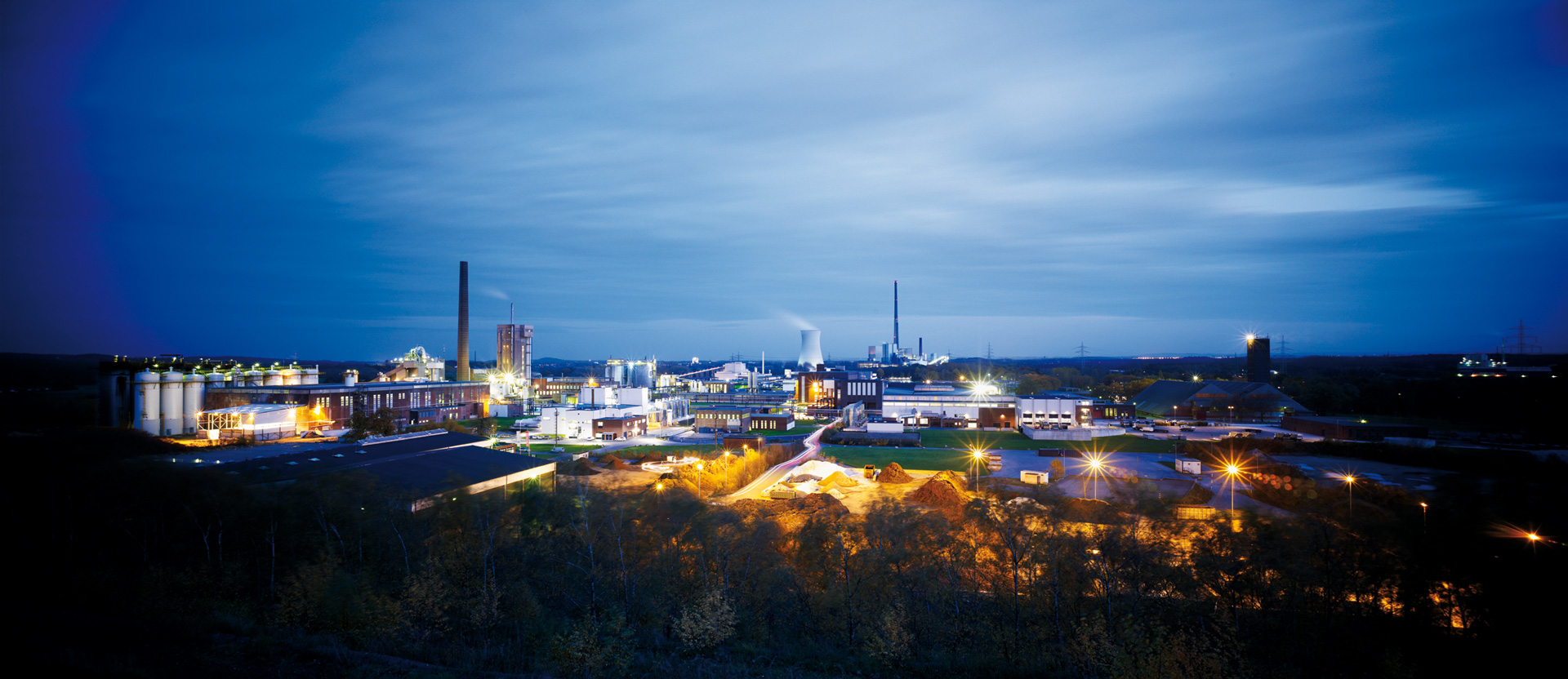
One of the major tasks is the processing of approximately 280,000 tons of gypsums per annum, which accumulate as side products in the coal-fired power stations in the vicinity. These side products are formed in the flue-gas desulphurization plants (FGD) of power stations which are fired with fossil fuels.
In Lünen, Remondis transforms these FGD gypsums into high-quality additives and binders which are then supplied to the gypsum industry under the trade name of "RADDiBIN" as raw material for different applications. They are used, for example, to manufacture jointless floors, cellular concrete, fertilizers, cement, or material for dentistry.
In the Lippewerk factory, two product types are currently based upon the processed FGD gypsums. ALPHA hemihydrate which after the addition of water boasts a particularly high stability, and anhydrite, which is fired at very high temperatures and which is, therefore, particularly suitable for the manufacture of screed materials.
During the anhydrite production, nothing works without kiln 7. This "monster", with a height of over 50 meters, is literally "in the heat of the action". In it, approximately 1,000 tons of FGD gypsums every day experience their metamorphosis into valuable raw material at a temperature of over 800°C.
Much turbulence around quality
The so-called calcining kiln functions according to the principle of the circulating fluidized bed. Initially constructed for the calcination of aluminum hydroxide, it was converted during the restructuring of the Lippewerk factory in 1989 to take on the calcination of gypsum.
During calcination in the fluidized bed, fine-grain material is transported at high rates in hot gas and simultaneously dehydrated to anhydrite through the energy of the hot gases. Through the unique plant technology, this process is controlled in such a manner that all particles are exposed to the same residence time and to identical process temperatures. Through this, quality can be achieved on an industrial scale which corresponds to the properties of laboratory quality on a minimum scale.
For kiln 7, fluctuations in quality are no problem. After all, it has it all cut and dried in terms of process technology. And this can be taken literally. Because one of the trouble spots of the fiery giant is its fabric filters. If they become too humid, productivity and quality also quickly break out in a cold sweat.
Breaking out in sweat because of humidity
The risk of moisture penetration into the fabric lies, above all, in the cleaning of the fabric filters with compressed air. Strong pressure surges hit the fabrics to remove adhering gypsum. In the event that the compressed air used for this process is not absolutely dry, humidity will also be blown into the fabric with the pressure impulses. In addition, the jet of compressed air leads to an abrupt cooling down, with temperatures dipping below the dew point.
The humidity reacts with the gypsum residues in the fabric and hardens the gypsum dust. Consequently, the fabrics will harden and finally break. This is a gradual process which, however, immensely accelerates the ageing of the fabrics. Here, Remondis saw a considerable savings potential regarding the operating costs. The basis of a significantly increased profitability should be the completion of compressed-air processing by powerful compressed-air drying.
Before now, the service life of the fabric filters in kiln 7 cleaned with undried compressed air was approximately 2 years. If drying was implemented, the service life of the fabrics, according to calculations, could be enhanced to approximately three years. With 432 installed fabrics at a unit price of approximately 100 euros, this would mean enormous cost savings.
Subsequent to extensive planning, Remondis invited tenders at the beginning of 2009 for the installation of a cold-regenerated adsorption dryer in the compressed-air system of the kiln.
With warmest recommendations
Contrary to the competitors, BEKO TECHNOLOGIES broke ranks with their suggestion. While all the other providers offered a cold-regenerated dryer, as per the invitation to tender, BEKO TECHNOLOGIES strongly recommended a heat-regenerated model.
For larger volume flows, adsorption drying represents definitely the only industrially commonly used method for the drying of compressed air down to dew points of -20° C and lower. The dimensions of the case of application which, for Remondis, means up to 1,500 cubic meters per hour, ultimately leads to the decision between cold-regenerated and heat-regenerated devices, depending on what seems to be more useful regarding profitability.
Cold-regenerated adsorption dryers
Cold-regenerated adsorption dryers operate with short loading cycles. Due to low loading of the desiccant, regeneration takes place without the additional input of thermal energy. The humidity is discharged via a dry-air partial flow which is expanded to atmospheric pressure.
In the cold-regenerated adsorption dryer, electric energy is required only for the control and the switch over of the valves. The electric power demand is therefore negligible. But: the low to average investment costs stand in contrast to the consumption costs of approximately 15% of the already processed compressed air, based on full-load conditions at 7 bar. The costs caused by purge air losses quickly add up to unacceptable amounts. This was the convincing argument for Remondis to decide in favor of a heat-regenerated device.
Heat-regenerated adsorption dryers
There are different designs for plants with blast air desorption. What all methods have in common is that no processed system air is employed to remove the adsorbed humidity, but heated ambient air instead. However, there are differences regarding the methods used to cool the desiccant.
In the classic model, an expanded partial flow of processed compressed air is simply used for the cooling of the desiccant. This results of course in some of the precious compressed air being used for purposes other than those intended. Even if this only amounts to two or three per cent on average, profitability is affected.
The alternative, which is much more economic, are "Zero Purge" adsorption dryers which function without any consumption of the processed compressed air. In these dryers, desorption is implemented like in the conventional method, through heated ambient air which is led through the adsorbent by means of a blower. Subsequent cooling of the heated desiccant is also implemented using ambient air.
Drawing profitability from the woodwork
Subsequent to an extensive analysis of the ambient and operating conditions at kiln 7, the processing and system specialists from BEKO TECHNOLOGIES focused on the heat-regenerated adsorption dryer of the EVERDRY FRA-V type from the wide range of products of the company. The plants of the FRA-V series do not require compressed air for the desorption process or for subsequent cooling of the heated desiccant (Zero Purge).
During the desorption phase, the regeneration blower works under pressure conditions. While the drying of the compressed air takes place in one of the adsorption containers, the second adsorption container - which has been saturated with moisture beforehand - is regenerated. Prior to the start of regeneration, a gentle pressure relief to atmospheric pressure is implemented. The regeneration blower conveys ambient air to the downstream heater. There, heating to the required desorption temperature takes place.
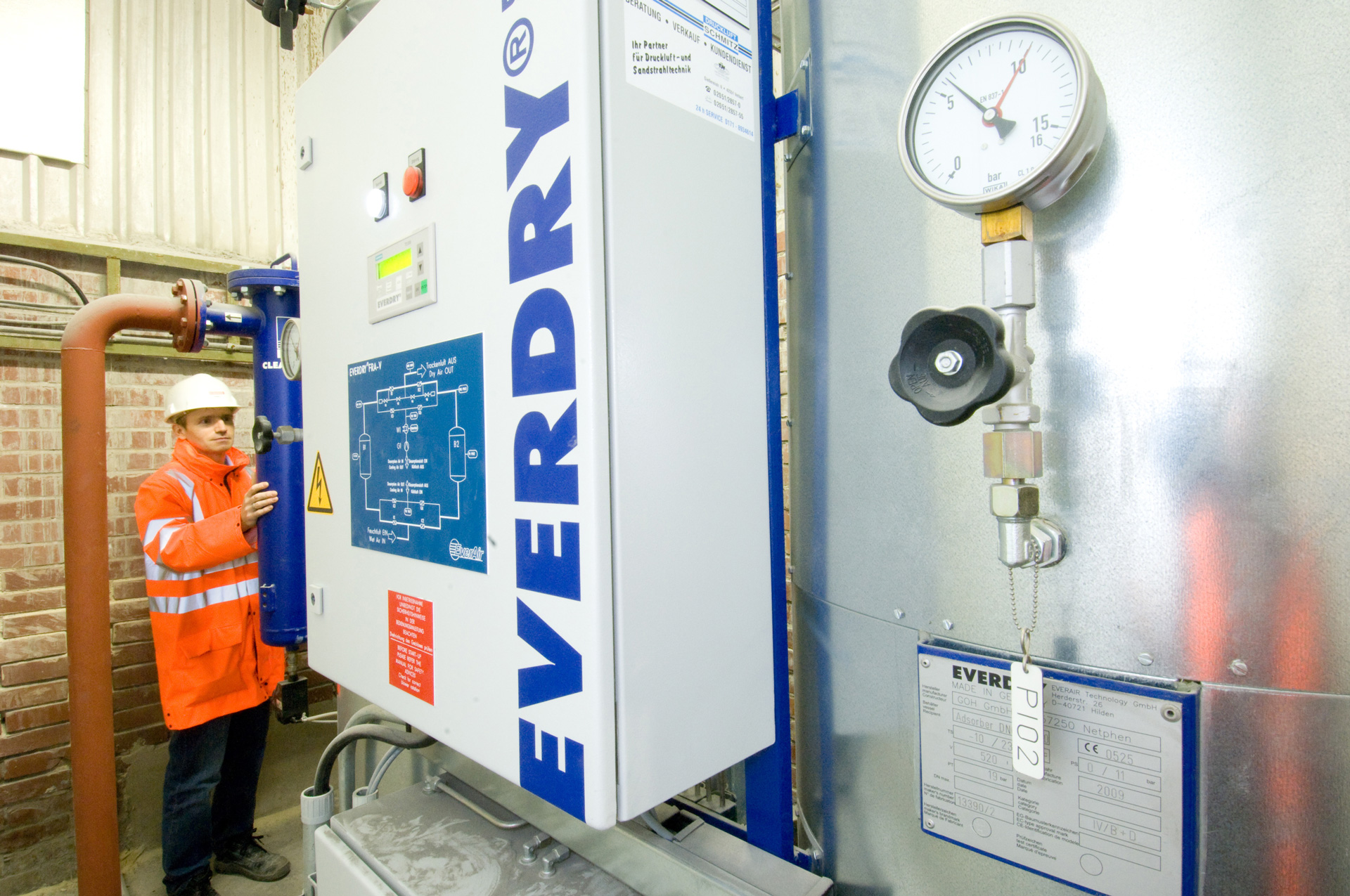
The pressure operation of the regeneration blower results in a temperature increase which has a positive effect on the power consumption of the heater. The heater air flow from the blower vaporizes the moisture taken up by the desiccant. Subsequently, this moisture is discharged into the atmosphere along with the air flow. Desorption takes place in an energetically optimized way using a reverse-current process.
The cooling phase takes place under vacuum conditions. Temperature and dew point peaks subsequent to the switch over are prevented by removing the heat accumulated in the desiccant after the desorption phase, along with the cool air flow from the blower. In the cooling phase, the blower switches to suction operation whereby the ambient air flows directly into the adsorption container to be cooled. The negative pressure produced during the suction operation, causes a change of the "physical balance" in the desiccant. The desorption temperature decreases because of the negative pressure, thus effecting after-desorption during the cooling phase. Due to the after-desorption, there is a lower residual load in the desiccant after the regeneration phase (heating and cooling). The residual load in the desiccant decisively influences the quality of the drying phase.
BEKO TECHNOLOGIES was convinced that through the energy-efficient operation of the heat-regenerated adsorption dryer alone (compared to a cold-regenerated dryer), one can assume pay-off of the investment costs at Remondis in less than one year.
But it was not only this perspective that made Remondis decide in favor of the BEKO TECHNOLOGIES solution. Flexibility and the comprehensive way of thinking during the planning and implementation phase were also important for Remondis. In this respect, they were served in the best way with a system provider like BEKO TECHNOLOGIES.
The highly efficient use of the dryer at kiln 7 in the Lippewerk factory in Lünen since Autumn 2009 proves that this nice theory is followed by the successful practical employment.
By the way, the EVERDRY adsorption dryer does not only have the filter cleaning cut and dried there. The process safety was also significantly improved in another field of application where compressed air is used at kiln 7: the operation of the measuring systems on the burner system. And problems with humidity and oil at the burner nozzles of the kiln are also a thing of the past since the dryer was installed.
Adsorption drying with a concept
The EVERDRY FRA product line from BEKO TECHNOLOGIES offers numerous variation possibilities. The standardized series is available for volume flows up to 20,000 m³/h. The portfolio also includes special solutions for over 20,000 m³/h.
As Zero Purge adsorption dryers, the plants of the FRA-V series offer the economic base for versatile applications on a high technical level.
The EVERDRY range of products also offers suitable solutions for the employment at high inlet temperatures in warm and humid climate zones with an intelligent cost-benefit structure. The EVERDRY FRL, as a "closed-loop" adsorption dryer, is suitable even for the employment under tropical climate conditions with its cooling conduction in a closed circuit.
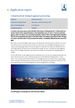