Compressed air treatment at a beverage industry plant
Industry: | Food & Beverage |
Customer/Location/Year: | RheinfelsQuellen, Duisburg-Walsum (Germany), 2013 |
Use of compressed air: | in production |
Installed products: | BEKOKAT, DRYPOINT RA |
Every hour, 150 cubic meters of purest mineral water are produced by the 14 wells of RheinfelsQuellen in Duisburg-Walsum. Enough to fill 883 bathtubs every 60 minutes – or more than 207,000 bottles. To add sparkle to the water, there is only one solution: oil-free compressed air fed to state-of-the art bottling plants and peripheral systems. The company uses an innovative catalytic process for the total oxidation of hydrocarbons in the compressed air system.
H. Hövelmann Getränke- und Brunnenbetriebe, the company behind RheinfelsQuellen, is achieving healthy growth from a healthy product, as its water is extracted from the huge natural reservoir located deep under the nature reserve of Rheinaue.
Water is extracted at an hourly rate of 150 cubic meters from a depth of 380 meters. With a yield of 3.6 million liters per day, the company can fill around 207,000 bottles every hour. Of these, 72,000 are returnable glass bottles, 90,000 are returnable PET bottles and 45,000 are recyclable plastic bottles. In addition, the company sells its water in kegs to customers in the hospitality sector. The mineral water is marketed under various names, including RheinfelsQuelle and Römerwall. The water is also used to produce fizzy drinks of the popular Sinalco brand, which we probably have all enjoyed at some time.
RheinfelsQuellen has for many years been certified according to the International Features Standard IFS Food and even meets the requirements of the latest, even more stringent IFS Food version 6. To maintain its excellence in product quality, the company relies on filling technology that excludes any risk of contamination. With a 24/6 operation, they need technology that stands for 100% process safety. Oil-free compressed air is one of the key elements to ensure this.
Oil-free compressed air for sensitive applications
The eight bottling lines of RheinfelsQuellen are supplied through two separate compressed air systems pressurized by two independent compressor stations. The conventional processing air system includes five screw compressors with capacities of between 90 and 120 kW. A frequency-controlled compressor provides the basic air flow, while the other units are automatically switched on and off as required.
The second, smaller system is pressurized by a 50-kW oil-free compressor and supplies oil-free compressed air to dedicated consumption points. Compressed air of this high quality is required in sensitive sections of the bottling plant. De-pending on the application, the oil-free compressed air needs to be sterile, for instance at fillers where products free of CO2 are transferred into containers or tanks, and the carbon dioxide at the top of is to be replaced with sterile air. Oil-free compressed air is also required in date printers at filling stations to prevent the ink from blocking the minute print nozzles. It is equally indispensable for the operation of precision valves used for the highspeed transport of bottles or the labelling of pallets.
By running a single oil-free compressor, they have eliminated all unnecessary redundancy in this small compressed air system. In the event of a compressor failure, there is no need to panic, as their innovative catalysis technology provides a safety net.
The catalysis technology enables Rheinfels Quellen to feed the oil-free compressed system from our five conventional screw compressors without any risk of oil contamination. This is achieved by means of a switchover unit installed between the two compressed air systems. In other words: they can always supply all consumption points with perfectly oil-free compressed air, irrespective of the compressor type.
This is made possible by the BEKOKAT solution developed by BEKO TECHNOLOGIES GmbH, a compressed air system supplier based in Germany. The BEKOKAT is a compact unit that removes hydrocarbons from the compressed air through total oxidation, breaking them up into carbon dioxide and water
Turning hydrocarbons into water and air
To achieve this, the hydrocarbons are eliminated through total oxidation in a separate process after compression. This means that the oil is removed from the compressed air in a single system component and in a process, that is not affected by the actual ambient conditions, the initial oil concentration or the relative humidity of the compressed air.
The BEKOKAT method removes all oil contained in the air – be it in gaseous, vapor or aerosol form – after compression. These substances contained in the air are converted in a catalytic process into carbon dioxide and water, which is drained from the system after condensation in the downstream cooling unit. The method is environmentally friendly, as the condensate does not contain any oil and can thus be safely disposed of through the sewerage system without any further treatment. The BEKOKAT system is the only one in the world that completely removes all oil from compressed air. For RheinfelsQuellen, a company selling a pure natural product, the BEKOKAT is thus the ideal system.
Heterogeneous catalysis in seven steps
In the BEKOKAT, a special granular material serves as the catalyst. This material is heated by heating elements to an operating temperature of around 150° C. The oil molecules are broken down into compounds that only contain a single carbon atom. In the final phase of the catalysis, the oil molecules are oxidized to H2O and CO2.
The entire catalytic process is performed over seven steps. Initially, the sub-stances to be removed, i.e. the oil molecules in the contaminated compressed air, are diffused to the surface of the granules. Subsequently, the reactants are diffused into the pores and absorbed. This process is followed by a surface reaction. In a next step, the reaction products are desorbed and subsequently diffused from the pores. Diffusion into the homogeneous phase concludes the process.
For the process to be effective, the hydrocarbon chains that form the oil molecules must be completely broken up into carbon dioxide and hydrogen. The BEKOKAT has no problems doing this and can break up hydrocarbon chains of any lengths, whether they originate from the ambient air or the compressor lubricants. In the same catalytic process, the BEKOKAT also eliminates polar compounds such as olefins, alcohols, glycols and ketones. The purified compressed air is subsequently cooled to a temperature that is approx. 10 to 15 K below the inlet temperature, and is now ready for use.
The BEKOKAT is the only system in the world ensuring a constant supply of oil-free compressed with a maximum residual oil content of as little as 0.003 milligram per cubic meter. The compressed air treated in the BEKOKAT thus meets the stringent requirements of the medical, pharmaceutical, food processing and packaging industries. The catalytic system is not only highly efficient but also cost-effective, as the special granular material used in the BEKOKAT only needs to be changed every 20,000 operating hours.
Peace of mind
After investing in its first BEKOKAT in 2011, RheinfelsQuellen in Duisburg-Walsum has never looked back. The first BEKOKAT unit was bought to treat the compressed air from the two oil-free compressors in operation at the time. The system always worked to the full satisfaction of RheinfelsQuellen, and when one of the oil-free compressors needed to be replaced, the company decided not to do this. Instead, it invested in two more BEKOKAT units for installation in its second compressed air system fed by screw compressors. Also reassuring are the TÜV certificates for the BEKOKAT, certifying that the unit is suitable for continuous mode operation, providing sterile compressed air with a verified low residual oil content.
Another important issue are of course the running costs. There are huge differences regarding the efficiency of oil-free compressors on the one hand and conventional, oil-lubricated screw compressors with downstream BEKOKAT treatment on the other, which makes the latter a much more costefficient solution. In addition, the BEKOKAT units are relatively cheap, while the com-pressed air treated in such systems is of a constant high quality, irrespective of the air intake conditions. When it comes to maintenance, the costs for systems that combine conventional compressors and BEKOKAT units are lower than those for oil-free compressors.
The BEKOKAT is suitable for retrofitting into existing compressor stations. By installing a BEKOKAT, any station with oil-lubricated compressors can be turned into a supply system for oil-free compressed air, as has been demonstrated by RheinfelsQuellen in Duisburg.
Ideal for combination with refrigeration dryers
At the Duisburg plant of RheinfelsQuellen, a system with oil-lubricated compressors and BEKOKAT units has been combined with DRYPOINT RA refrigeration dryers from BEKO TECHNOLOGIES. These remove any residual moisture from the compressed air that has undergone total oxidation in the BEKOKAT. Given the relatively high temperature of compressed air produced in screw compressors, DRYPOINT RA refrigeration dryers are the perfect solution to cool down the air.
In the DRYPOINT RA, the air is dried in a counter-flow process with optimized heat exchange along the entire process path, whereby the downward flow of the air is not obstructed in any way. The large counter-flow heat exchanger unit that consists of an air-air and an air-refrigerant heat exchanger cools the com-pressed air to a temperature of around 3° C. The size and design of the heat exchangers promote effective cooling while minimizing flow resistance. Every month, around 1.3 million cubic meters of oil-free com-pressed air are generated. By combining catalysis and dryer technology, RheinfelsQuellen achieved a reliable process safety level.
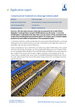