Compressed air treatment XXL at Chempark Uerdingen
Industry: | Chemical |
Customer/Location/Year: | Currenta, Chempark Uerdingen (Germany), 2008 |
Use of compressed air: | Measuring, control, process air, conveyor air |
Installed products: | EVERDRY |
BEKO TECHNOLOGIES has implemented a major project for an adsorption dryer which utilizes the heat from the compression process for regeneration. The plant was handed over to CURRENTA after successfully completing the trial operation.
The plant located in CHEMPARK Krefeld-Uerdingen designed for a compressed air flow rate of 65,000 Nm³/h and supplies several production sites with compressed air on site. The compressed air hereby generated is mainly utilized by the users as MCR air (measure, control, regulate) or as process and/or factory air e.g. for conveying plastic granules
The Concept XXL
Compressed air drying is an integral part of every compressed air station. The permissible residual moisture in the compressed air therefore decisive when selecting the drying method. Adsorption dryers are normally utilized in this case with pressure dew points in minus ranges. The highest economic efficiency is indicated by methods which take account of not only the compressed air generation but also processing and treatment as part of the energy balance and make optimum use of existing energy sources.
This guiding subject was considered during the implementation of the XXL adsorption dryer for the CHEMPARK Krefeld-Uerdingen in accordance with the utilizer’s desire for high-quality, stable compressed air processing and treatment.
A special feature of the XXL adsorption dryer EVERDRY HOC 65000 C is that the plant does not have two, rather three adsorption tanks, from which two are always operating in parallel switching for the compressed air main flow. The respective third container is conversely removed from the main flow, regenerated and then made "sharp" again for the next drying process. The ongoing switching is executed as performance-controlled.
The “Three-Container-Concept” guarantees an equal operation without a high-pressure dew point and fluctuations in pressure differences. The result is a “soft” operation process which is what the owner/operator requested. The plant uses the existing energy from the compression processes for desorption i.e. for removing the moisture absorbed in the desiccant. This method is called heat of compression, abbreviated as HOC.
Planning, manufacturing, assembly
The project planning, designing, construction and commissioning for a plant with these dimensions created a real challenge. BEKO TECHNOLOGIES however has a specialist team for such projects which has a very good reputation in the compressed air branch. Utilizing our considerable experience, expertise and know-how enabled us to master this task to the customer´s complete satisfaction.
Planning was executed with state of the art 3D CAD design tools. This made the customer´s site supervision easier to evaluate the plant connections and/or plant positioning and even suggest adjustments during the development stage.
The plant manufacturing was implemented in modular units which were pre-assembled at the manufacturing factory for assembly by the operator. Delivery was then executed from the manufacturing factory to the installation location in Krefeld-Uerdingen overnight with seven special transporters in December 2007.
After two weeks of assembly work at the installation location, the EVERDRY HOC 65000 C largescale plant was then completed. With a total weight of almost 100 tons, the complete plant then had stately dimensions of 14 x 7 meters and a height of almost 6 meters, including an operator and service platform in the upper section of the adsorption dryer which is accessible via a staircase.
Trial operation and commissioning
The 72-hour long trial operation for the EVERDRY “XXL” adsorption dryer on the company premises at the CHEMPARK Krefeld-Uerdingen went successfully. The project team from BEKO TECHNOLOGIES and the operator CURRENTA were completely satisfied with the performance of the adsorption dryer.
The plant was then handed over to CURRENTA after successfully completing the trial operation. The plant then assumed the compressed air supply for numerous production locations on the CHEMPARK company premises. The operating locations from Bayer Material Science, LANXESS and Tronox will also be supplied with compressed air from the EVERDRY adsorption dryer. The scope of services also includes transferring the process parameters to the superordinate control system, which thereby monitors the generation, processing, treatment and supply for the compressed air.
The operator confirmed that all the parameters were immediately complied with from the initial moment after the handover.
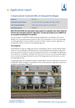