Monitoring compressed air in food processing
Industry: | Food & Beverage |
Customer/Location/Year: | Nölke, Versmold (Germany), 2016 |
Use of compressed air: | Control air, process air |
Installed products: | METPOINT OCV |
According to ISO 8573-1, compressed air of class 1 must not contain more than 0.01 mg/m³ of oil (liquid, aerosol or vapor). This is as little as 4% of the concentration found in normal ambient air! There are however processes, where even 0.01 mg is still too much. This is especially the case in food processing where certain applications demand that oil content in the compressed air is less than 0.003 mg/m³. There are however only a few companies that are able to monitor such low concentrations. One of them is Heinrich Nölke GmbH & Co. KG, a well-known producer of sausages.
Established in 1924, the company based in Versmold in Westphalia is steeped in tradition. It now forms part of the Zur-Mühlen-Group and is the leading supplier of poultry sausages in Germany. The popular sausage brands Gutfried, Menzefricke and Müritzer are all produced in Versmold. Other specialties from the group are the Böklunder, Redlefsen, Könecke and Schulte sausage.
At Heinrich Nölke GmbH, it's all about sausages. And its production capacities are impressive. The company employs around 400 people and produces about 2,500 tons of quality poultry sausages per month.
Commitment to food safety
Being fully aware of their responsibilities as a food producer, the safety of their products are always the most important issue. That is why quality control begins well before the raw ingredients arrive at their production plant. The first cornerstone of the Nölke quality management system is the selection of safe, top-quality ingredients. Their suppliers have been carefully selected according to extremely strict quality, hygiene and safety criteria and are regularly audited. Nölke´s standards go way beyond the statutory safety requirements.
The commitment to quality by Heinrich Nölke GmbH is also reflected in the list of national and international standards for which the company has been certified, unmatched in the industry:
|
|
|
|
|
|
|
|
|
To meet these standards, Heinrich Nölke GmbH uses an impressive range of process-focused and cross-process monitoring and control mechanisms. In addition, the finished products are constantly tested by independent external experts. Process safety is thus at the core of all activities at Heinrich Nölke GmbH.
Compressed air as a crucial process medium
One of their most important process media is compressed air. While it is mainly used as control air for their production plants, it comes into direct contact with their products at a few points along the production chain. This means that the compressed air must be free of oil in all its forms – liquid, aerosol and vapor. This standard must be maintained across the entire system and at all times. Nölke needs to monitor and document the quality of compressed air in real time.
These requirements pose a huge challenge for most businesses, as the monitoring of the residual oil concentration in compressed air systems is a very difficult task. Most conventional solutions are only able to determine the oil content after it is produced, rather than offering a measuring strategy that detects problems before the damage is done.
Most companies that use oil-free compressed air are well able to determine the residual oil content in lab tests. The results of these tests are however only available days or even weeks after the samples have been taken. Due to this delay, they are not able to respond quickly and effectively to problems caused by contaminated compressed air. In a worst-case scenario – which is also the most common case – problems with the product or the production process have already become obvious before the lab results are back. The consequences are product stops, high reject rates or even claims for damages, which are all extremely costly.
Worldwide, the damage caused by contaminated compressed air in production and processing plants amounts to millions of Euro. Most of these incidents are due to undetected ingress of oil into the compressed air system and its subsequent distribution across the system to the points of consumption.
Such problems are mainly caused by oil aerosols and vapors. The oil contained in the compressed air sometimes escapes at tools and machines where it might form a film on surfaces and come into contact with the product, contaminating it.
Clean is good – pure is better
The quality of compressed air is commonly classified according to ISO 8573-1. There are however many applications where compressed air of class 1, which is deemed to be technically oil-free, is not clean enough.
According to the above standard, compressed air of class 1 must not contain more than 0.01 mg/m³ of oil (liquid, aerosol or vapor), which is only about 4% of the concentration found in normal ambient air. These concentrations are already so small that they are virtually undetectable.
However, many compressed air applications – for instance in the field of medical technology, pharmaceutical production, measuring technology and food processing – require even lower oil concentrations to ensure process safety. Nölke is among the processors who need compressed air with a residual oil content of less than 0.003 mg/m³.
At such low concentrations, it is more difficult to monitor the quality of the compressed air than to produce it. Continuous, real-time residual oil concentration monitoring of the compressed air with proper documentation is something most operators have not achieved yet.
Instead, they opt for frequent lab tests, which is very time-consuming. As the test results are only available days or even weeks later, corrective action can only be taken after the damage has been done. Far too often, companies need to stop production and remove potentially contaminated products from their shelves, which is very costly.
Even less satisfactory than the lab testing method is keeping one's fingers crossed, trusting that, as long as there are no obvious problems in the production process, everything will be OK. While everybody would agree that simply hoping for the best is not really an adequate strategy, it is still widely practiced.
Strategy of continuous improvement
Nölke in Versmold has chosen a different approach: a strategy of continuous improvement. They use advanced technology to assess and ensure the quality of their processes as close to real time as possible. For compressed air, they have invested in an innovative measuring system that allows them to continuously monitor the residual oil content. A real milestone in process safety.
We are talking about the METPOINT OCV, a hydrocarbon monitoring system that measures the concentration of hydrocarbon vapors. It has been designed for the stationary inline measurement and monitoring of residual oil vapors in compressed air based on the ISO 8753-5 standard.
Online monitoring of compressed air quality
Developed and produced by the German compressed air system specialist BEKO TECHNOLOGIES, the METPOINT OCV continuously monitors the residual oil content in compressed air and can detect concentrations down to 0.001 mg/m³ – inline, during production. METPOINT OCV continuously samples the compressed air and feeds it through a riser pipe to the sensor unit inside the device. There, the oil vapor concentration is measured by a PID or photoionization detector. Here, UV radiation is used to break molecules into ions. This results in an electric current. In the METPOINT OCV, which measures only 23 x 20 cm, this current is measured and the output signal is amplified and analyzed. The results are displayed on the large touch screen of the METPOINT OCV. At the same time, the measurement date is stored in the 2 GB memory of the device. Thanks to this large memory capacity, Nölke will be able to record all measurements for the next ten years.
Complete documentation of the compressed air quality
If the measured oil vapor concentration in the compressed air is outside the tolerance range, the METPOINT OCV generates an alarm signal. Excessively high residual oil contents are thus detected instantly and the operator is alerted to take action before any costly damage is done.
The alarm limits can of course be set by the operator, as they differ from plant to plant. They are password-protected in order to prevent inadvertent or unauthorised changes to the limits. With the METPOINT OCV from BEKO TECHNOLOGIES, it is now possible to constantly monitor the oil vapor concentration in compressed air systems that need to meet stringent standards.
Thanks to its data logging functions, the system offers new possibilities as regards quality assurance and process safety – two very important issues for Nölke. On the one hand, all measurements and therefore the compressed air quality are fully documented. On the other, the data enables the operator to identify the source of the contamination. This is a huge additional advantage of the system over lab tests. What is more: The METPOINT OCV is designed for network integration, and Nölke has of course integrated the unit into its IT infrastructure.
Data safety during calibration and maintenance
Nölke´s maintenance team is particularly impressed with the service concept of the METPOINT OCV. The data is safe, even during maintenance and calibration, and all steps are logged. When the device needs to be returned to BEKO TECHNOLOGIES for OCV calibration, Nölke is provided with a replacement unit that continues recording all the relevant data, which can then be transferred back to the original device. The data format is tamper-proof and cannot be manipulated or lost during importing and exporting. Another great advantage is the fact that there is no need to reduce the pressure in the system or to shut down the plant when the METPOINT OCV needs to be temporarily replaced. As it takes only a few minutes to remove and install the device, the air is fed through a bypass until the METPOINT OCV is again ready for operation. When it comes to process safety, Nölke is leading the way.
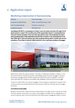