Quality assurance at an automotive supplier
Industry: | Automotive |
Customer/Location/Year: | HELLA, Hamm (Germany), 2013 |
Use of compressed air: | Process air |
Installed products: | BEKOKAT, DRYPOINT RA, CLEARPOINT, BEKOMAT, BEKOSPLIT |
Blowing of high-performance electronics via pulsating rotary jets, and tracing of plastic housings with cleaning plasma jets: At the German automotive supplier Hella, compressed air takes over the central tasks in the surface cleaning of safety-relevant components. The most important requirement in this respect: the reliable, complete absence of oil.
Without Hella, vehicle safety would be on the dark side. And this is in the truest sense – because Hella KGaA Hueck & Co., with its headquarters in Lippstadt, Germany, develops and manufactures lighting technology and electronic products for the global automotive industry and has one of the largest trading organizations for automotive parts and accessories in Europe. From the technical and economic point of view, the enterprise is a true shining light in the automotive world.
With a turnover of EUR 4.8 billion, the family company which, still today, is independent, ranks amongst the world's top 50 automotive suppliers, and is one of Germany's one hundred largest industrial enterprises. Since 1990, the turnover annually increased by seven per cent on average. 23 per cent of the turnover is generated in Asia, mainly in China, and 19 per cent in North and South America. Worldwide, Hella employs approximately 27,000 people at around 70 locations, in more than 30 countries – 4,800 of which in the field of research and development.
In Germany, the company has slightly fewer than 10,600 employees, with approximately 1,400 of them working in the Hella factory 4 in the Westphalian city of Hamm. There, Hella manufactures small batch series of heating controllers, and access systems for vehicles, in particular body and control electronics. In the center are steering control devices for EPS systems; in other words, electrically powered servo steering.
Highly turbulent, pulsating air flows
As the central function and safety units of a motor car, the steering system and its components receive, by nature, increased attention when it comes to product quality. A responsibility which the automobile manufacturers uncompromisingly also pass on to their suppliers. Hella faces these requirements with the maximum possible quality assurance and state-of-the-art manufacturing technology.
The non-contacting surface-cleaning systems in the production for steering control devices are a special example. They are installed at the transition point between the assembly hall and clean room, in which the sensitive electronics is implemented into the module racks. Here, every dust particle that is introduced from outside represents a quality risk – an introduction into the system must be prevented correspondingly. The solution: dry and, above all, absolutely oil-free compressed air – because humidity and oil application are more dangerous for the sensitive high-performance electronics than any dust particle.
The non-contacting cleaning of the module racks is implemented via special surface-cleaning devices in the load locks of the clean rooms. They have numerous rotary jets which, through their rotary motion, generate a pulsating highly-turbulent air flow with a high cleaning effect. Arranged above and below the components which pass through on a conveyor belt, they reliably blow off every single mote under high pressure. An absolutely reliable cleaning method, provided that the compressed-air quality is suitable.
In 2010, Hello turned towards a completely new form of compressed-air processing for this application purpose, namely the catalytic method. The catalysis was capable of fully eliminating the residual insecurity that prevailed until now regarding the actual oil content of the compressed air.
Catalytic compressed-air processing
With the BEKOKAT catalytic method which was developed by the German compressed-air system provider BEKO TECHNOLOGIES GmbH, Hella achieves compressed-air purity with a residual oil content of a barely measurable 0.003 milligram per cubic meter of compressed air. With this, the result exceeds the requirements of ISO 8573-1 for oil-free compressed air of class 1 with 0.01 milligram per cubic meter by far. Catalysis with the BEKOKAT devices achieves total oxidation of hydrocarbons and this in a concentrated, comprehensive process step subsequent to compression. In this manner, the full oil removal from the compressed air is implemented in only one plant component. This component functions independently of the ambient conditions, even at oil inlet concentrations of more than 20 milligrams per cubic meter and a relative humidity of the compressed air of up to 100 per cent.
The BEKOKAT method addresses all the contaminations that are based on hydrocarbons in the compressed air that is supplied by the compressor, e.g. lubricants or oils. These exist downstream of the stage of compression in the form of gas, vapor, or aerosol. The BEKOKAT fully converts such air components into carbon dioxide and water. Through the employment of a refrigeration dryer, the water can be separated and discharged. The condensate is then pure to such an extent that it underruns the limit value for hydrocarbons significantly. Therefore, it can be introduced directly into the public sewerage system. Currently, no other device realizes such total oxidation and the absolutely residue-free performance of the BEKOKAT catalysis. The catalyzing material of the BEKOKAT only needs to be replaced after 20,000 operating hours. At a three-shift operation, this corresponds to a maintenance-free runtime of more than two years. More than two years without sterilization cycles, production stoppages, and quality risks – this is also an enormous plus for the process reliability and profitability of compressed-air supply. Another decisive advantage for Hella: the technical catalysis equipment from BEKO TECHNOLOGIES could smoothly be integrated into the existing compressed-air system – and this in due consideration of all standard specifications
Plasmajet with a share of compressed air
High technology at Hella has long ceased to be used only for the manufacturing of steering control devices. Another BEKOKAT field of application at Hella is the so-called plasma cleaning. Here, a plasma jet traces and cleans the surfaces of plastic housings in order to prepare them for the gluing in this manner. During this work, the plasma jet carries along a considerable share of compressed air. The absolute absence of oil in the compressed air is an imperative requirement in this respect, and is guaranteed through the BEKOKAT catalysis method. The catalytic converters, which are installed decentralized at the respective points of need, are supported by the DRYPOINT RA refrigeration dryers and CLEARPOINT filters, also from BEKO TECHNOLOGIES.
In the Hamm factory alone, in addition to the already mentioned devices, another two refrigeration dryers in the central compressed-air processing as well as eight membrane dryers, approximately 30 filters of different designs, more than 40 BEKOMAT condensate drains, an ÖWAMAT oil-water separator, a METPOINT leakage test system, and a BEKOSPLIT splitting plant for the purification of emulsified condensates are employed. A similarly comprehensive equipment with regard to compressed-air processing systems from BEKO TECHNOLOGIES can also be found in the Hella works in Recklinghausen and at the headquarters.
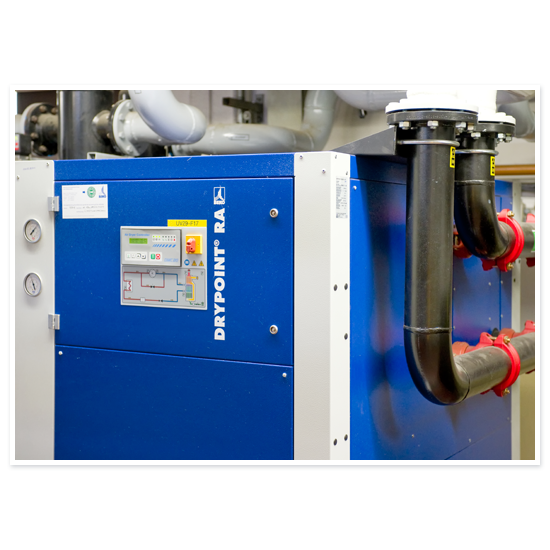
Hella: a shining example, even when it comes to environmental protection
BEKOSPLIT splitting plants purify emulsified condensates which developed because of unfavorable initial conditions, or due to certain lubricant-compressor combinations. In addition to compressed air condensate, other oil-containing industrial effluents can also be processed. Water-insoluble organic substances and a multitude of solid contaminations are removed from the water, and existing heavy metals, dirt, and paint particles are reliably adsorbed. The split-off oil and dirt particles are encapsulated by the release agent and form macro flakes which are filtered out in bags. The uncontaminated water that is flowing off can now be discharged into the sewerage system, just like it is in the case of the BEKOKAT catalytic converters.
Hella, therefore, is not only a shining light of German quality engineering when it comes to automotive electronics and lighting systems but also in terms of quality assurance and environmental protection, by means of state-of-the-art compressed-air processing
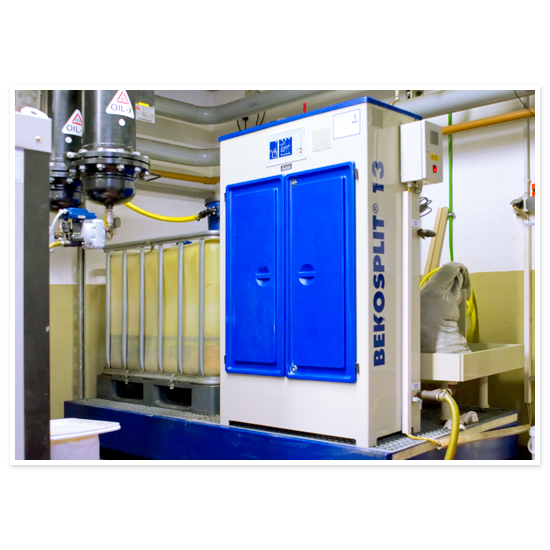
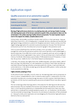