Compressed-air drying in the lime production
Industry: | Building materials |
Customer/Location/Year: | Oetelshofen, Wuppertal (Germany), 2010 |
Use of compressed air: | Conveyor air |
Installed products: | EVERDRY |
Just imagine a kind of pneumatic tube in XXL size. In the H. Oetelshofen GmbH & Co. KG lime works, limestone powder is transported on the plug-conveying principle from the production sites to the storage silos. Compressed air serves as the transport medium and in this respect one thing is of utmost importance: it must be absolutely dry.
With its Osterholz stone quarry in Wuppertal-Hahnenfurth, Germany, and the adjacent works, the medium-sized enterprise ranks among the pioneers and pacemakers of industrial lime production. Situated in the heart of the most important European limestone deposits, in the Bergisch Dornap district, Oetelshofen calcines more than 220,000 tons of lime per annum from the excavated rock.
The most important purchaser is the iron and steel industry, where lime is required as a neutralizer and to bind contaminations in slags. Lime also assists in environmental protection in eliminating unwanted secondary constituents, for example in drinking water and wastewater treatment, in the flue-gas or sewage-sludge treatment. In addition, the construction industry uses lime in road construction and in the production of construction material.
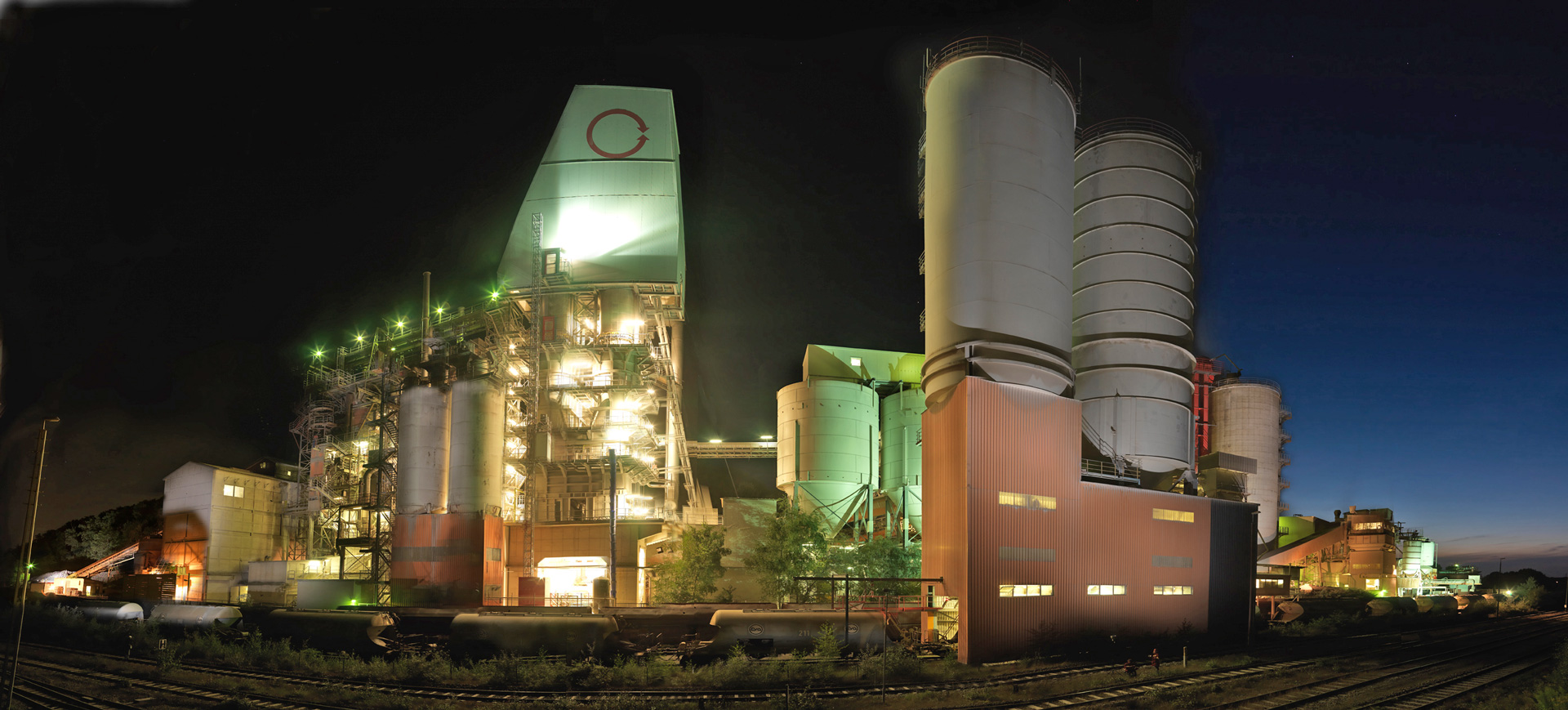
Internal material flow as the major challenge
This means a broad range of users which need to be served - with both silo tanker lorries and silo wagons. But already before the valuable cargo leaves the works, a great transportation challenge needs to be mastered: the material flow within the production site, for example between the individual production units and the storage silos.
While coarser-grained products, such as mineral aggregates, lump lime or limestone gravel can be moved relatively easily, this is not the case for limestone powder.
This finely-ground material is wind-sensitive and hydrophilic in equal measure. Open transport, or even transport in the open air, is therefore not advisable. The alternative for the limestone powder at Oetelshofen: conveyance via compressed air through a closed pipe system.
The pipe network of the gigantic "pneumatic tube system" for limestone powder on the Oetelshofen factory premises, which is subdivided into three lines and branched by means of guides, is just under 1.2 kilometers long. Via this system, "powder packages" are sent by compressed air on the pneumatic plug-conveying transport principle.
For this purpose, pneumatic capsules are available at the respective starting points of the pipe system, filled with the transport material and charged with compressed air. Via a valve that opens at regular intervals, the limestone powder is sent in gushes from this point into the 125-millimeter pipework. This transport mode is so efficient and powerful that even vertical tubing sections can be mastered over long distances without problems, for example up to the inlet piece of the storage silos for the limestone powder with a height of 45 meters.
A technically delicate matter
However, this method is also a technically delicate matter, because many parameters determine the functioning or the non-functioning of the system. Above all, reliably dry compressed air.
Limestone powder is sensitive to humidity. Even the slightest humidity introduction can lead to agglutination, and thus to a narrowing of the pipe cross-sections. Or the plugs become so tight that they stop gliding and clog the pipe. This would involve extensive maintenance and repair efforts, not to mention the losses caused by production stoppages. A reliably constant supply of absolutely dry compressed air is therefore vital for process assurance.
A central station substitutes stand-alone solutions
Up to that moment, several small "stand-alone" solutions existed, with compressors at different places, spread over the factory premises. The maintenance involved considerable time efforts and costs, so that the economic effectiveness and efficiency of the entire system was void.
A central compressed-air station was finally configured and installed by a local partner of BEKO TECHNOLOGIES, in which all main networks of the site are consolidated. The existing compressedair pipework systems were re-arranged and reasonably restructured. And in the end, an exceptional complete maintenance package was offered to Oetelshofen, which included full warranty for all components of compressed-air processing and supply.
A compressed-air dryer as the basis of the concept
The compressed-air expert assesses the heat-regenerated adsorption dryer of the EVERDRY FRA-V series, installed at Oetelshofen at the end of 2009, to be an important pillar of the entire plan, as far as technology and costs are concerned.
The device, developed and distributed by the German compressed-air system specialist BEKO TECHNOLOGIES GmbH fully replaces the two cold-regenerated adsorption dryers, employed until then, during the winter season.
With the exchange of the two cold-regenerated models for the powerful heat-regenerated adsorption dryer, Oetelshofen saves enormous energy costs, This results from the different operating principles of coldand heat-regenerated adsorption dryers.
Cold-regenerated adsorption dryers consume approx. 15% of the compressed air provided by the compressor as purge air – meaning for their "own needs". This amount of air is completely lost for the actual intended use of the compressed air in the respective plant. It nevertheless needs to be produced by the compressors, with the corresponding energy and cost requirements.
These "unnecessary" costs through purge air losses quickly add up to unacceptable amounts. This neutralizes the low to medium investment costs for cold-regenerated devices. When exactly analyzing the user's application and consumption situation, a heat-regenerated device turns out to be significantly more cost-effective, as is the case with Oetelshofen. According to the prognosis, the investment costs for the EVERDRY FRAV will have fully paid off within only one and a half years
Heat-regenerated adsorption dryers
The heat-regenerated EVERDRY FRA-V from BEKO TECHNOLOGIES, which was chosen for Oetelshofen, is a so-called "zero purge" adsorption dryer, which does not require compressed air either for the desorption process or for the subsequent cooling of the heated desiccant.
During the desorption phase, the regeneration blower works under pressure conditions. While the drying of the compressed air takes place in one of the adsorption containers, the second adsorption container - which has been saturated with moisture beforehand - is regenerated. Prior to the start of regeneration, a gentle pressure relief to atmospheric pressure is implemented. The regeneration blower conveys ambient air to the downstream heater. There, heating to the required desorption temperature takes place.
The pressure operation of the regeneration blower results in a temperature increase which has a positive effect on the power consumption of the heater. The heater air flow from the blower vaporizes the moisture taken up by the desiccant. Subsequently, this moisture is discharged into the atmosphere along with the air flow from the blower. Desorption takes place in an energetically-optimized way using a reverse-current process, meaning the opposite to the adsorption direction.
The cooling phase takes place under vacuum conditions. Temperature and dew point peaks subsequent to the switch-over are prevented by removing the heat accumulated in the desiccant after the desorption phase, along with the cool air flow from the blower. In the cooling phase, the blower switches to suction operation, whereby the ambient air flows directly into the adsorption container to be cooled. The negative pressure, produced during the suction operation, causes a change of the "physical balance" in the desiccant. The desorption temperature decreases because of the negative pressure, thus effecting after-desorption during the cooling phase. Due to the after-desorption, there is a lower residual load in the desiccant after the regeneration phase (heating and cooling). The residual load in the desiccant decisively influences the quality of the drying phase.
The EVERDRY FRA product line from BEKO TECHNOLOGIES offers numerous variation possibilities. The standardized series is available for volume flows up to 20,000 m³/h. The portfolio also includes special solutions for over 20,000 m³/h. With a volume flow of approximately 2,700 m³/h, which is currently required at Oetelshofen, all expansion options are available for the future with the EVERDRY FRA-V.
And another decisive point made this heat-regenerated adsorption dryer first choice: the EVERDRY FRA-V can be fully remote-monitored, online, via Internet access.
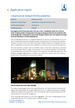