Kühlung von Laser-Schneidemaschinen mit Druckluft
Branche: | Lasertechnologie |
Kunde/Ort/Jahr: | Horstmann, Verl, 2008 |
Anwendung der Druckluft: | Prozessluft |
Installierte Produkte: | BEKOKAT |
Das Laserschneiden gehört zu den thermischen Trennverfahren. Das ist nicht erst am Fokuspunkt spürbar, dort wo der Laserstrahl auf das zu schneidende Material auftrifft. Bereits im davorliegenden Strahlengang geht es heiß her. Hier ist Abkühlung gefragt. Am besten und wirtschaftlichsten durch Druckluft. Die muss allerdings absolut ölfrei sein.
Bei der Horstmann GmbH & Co. KG mit Sitz in Verl bei Gütersloh widmet man sich hier der hochqualitativen und anspruchsvollen Metallbearbeitung für namhafte Kunden zahlreicher Wirtschaftszweige, darunter die Automobil- und Schiffsbau-Industrie sowie der Maschinen-, Anlagen- und Werkzeugbau.
Die bei Horstmann unermüdlich arbeitenden Laser-Schneidemaschinen würden höchst allergisch auf selbst einen minimalen Öleintrag durch Druckluft reagieren. Und zwar mit einer deutlichen Leistungs- und Qualitätsminderung. Weil ihr messerscharfer Laserstrahl wortwörtlich zur lasch flackernden „Ölfunzel“ degradiert würde. Anders als man vielleicht vermutet, wird die Druckluft an den Laser-Schneidemaschinen bei Horstmann nämlich nicht für die Pneumatik verwendet, sondern ausschließlich zur Kühlung des Laserstrahlengangs.
Prinzipiell besteht eine Schneideanlage mit CO2-Laser aus einer Laserstrahlquelle und einer beweglichen Fokussieroptik, meist ein Hohlspiegel oder eine Sammellinse. Von der Quelle aus wird der Laserstrahl über Umlenkspiegel zur Bearbeitungsoptik geführt. Dort wird der Laserstrahl fokussiert und so die zum Schneiden erforderliche Leistungsdichte erzeugt. Bei Horstmann, wo vorrangig Edelstahlbleche geschnitten werden, sind das bis zu sechs kW Strahlleistung. Genug übrigens, um einen menschlichen Körper mühelos komplett zu durchdringen.
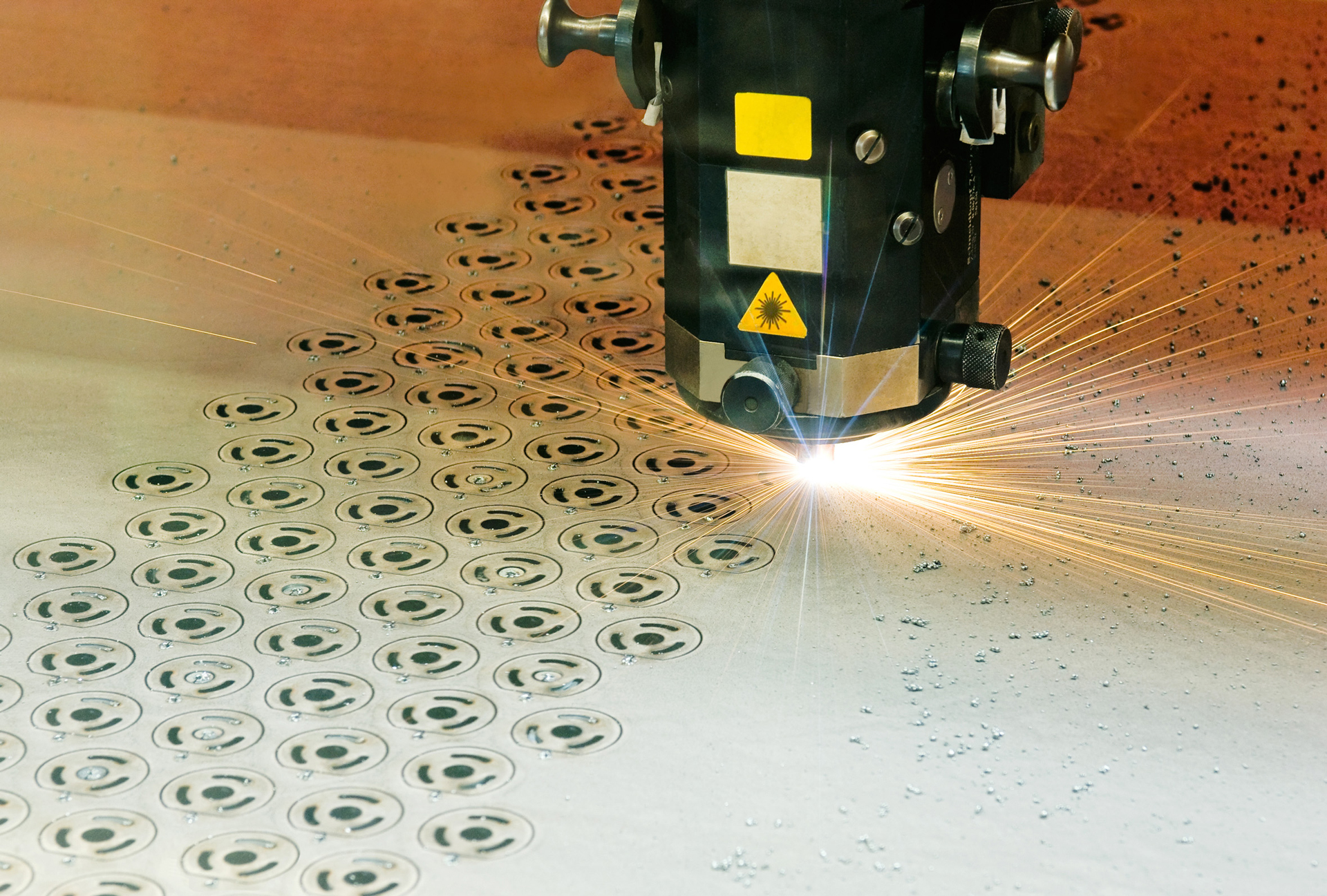
Dadurch, dass sich die verfahrbare, „fliegende“ Optik über die zu bearbeitenden Bleche bewegt, verändert sich ständig ihre Entfernung zur feststehenden Laserquelle. Allerdings hat der erzeugte Laserstrahl nicht die erforderliche Parallelität, um ihn über die teils großen und veränderlichen Distanzen zu übertragen. Deshalb und auch, um die thermische Belastung der Umlenkspiegel zu verringern, wird er zum Teil mit einem Spiegelteleskop ausgeweitet.
Die eigentliche Strahlenführung zwischen der Laserquelle und der Fokussieroptik erfolgt über gold- oder molybdänbeschichtete Spiegel, die meist entweder aus reinem Kupfer oder aus monokristallinem Silizium gefertigt sind. Und zudem höchst empfindlich auf Öl beziehungsweise Aerosole regieren, die sich auf ihnen ablagern und einen frühzeitigen, äußerst kostspieligen Austausch erforderlich machen.
Im gesamten Strahlengang des Lasers entwickeln sich naturgemäß erhebliche Temperaturen. Ohne Kühlung würden die hier eingesetzten Materialien, zum Beispiel die Umlenkspiegel und noch schneller der Faltenbalg der beweglichen Optikeinheit, erheblichen Schaden nehmen.
Diese lebenswichtige Kühlfunktion übernimmt in den Strahlengang eingeblasene Druckluft. Sie muss absolut partikel- und ölfrei sowie trocken sein, um weder den Laserstrahl durch schwebende Partikel zu „zerstreuen“ noch die Umlenkspiegel durch Ablagerungen zu verschmutzen. Schon geringste Öl- oder Aerosolanteile in der Druckluft hätten schnell fatale Folgen für die Prozesssicherheit und Wirtschaftlichkeit der Schneideanlage.
Beide Faktoren sind jedoch – zusammen mit absoluter Produktqualität – für die Heinrich Horstmann GmbH & Co. KG wesentliche Bestandteile des anhaltenden Geschäftserfolgs. Daher widmet man dem Thema Druckluftaufbereitung dort auch enorme Aufmerksamkeit.
Bislang versuchte man bei Horstmann – wie übrigens bei nahezu allen Druckluftanwender mit ähnlichen Ansprüchen – ölfreie Druckluft durch relativ aufwändige, oftmals sogar miteinander gekoppelte verdichter-, filter- und trocknerbasierte Techniken zu produzieren. Oft gelingt das jedoch nur mit mehr oder weniger großer Zuverlässigkeit.
Auch bei Horstmann fand man nie eine wirklich zufriedenstellende Lösung, vor allem nicht nach der Anschaffung neuer, noch leistungsfähigerer Schneideanlagen. Anfang 2008 stieß man auf ein vom deutschen Druckluftspezialisten BEKO TECHNOLOGIES GmbH entwickeltes Katalyseverfahren zur Herstellung absolut ölfreier Druckluft. Das BEKOKAT genannte Verfahren erschließt den Weg zur absolut ölfreien Druckluft mit einem komplett anderen technologischen Ansatz als alle bisherigen Lösungen: mit der Katalyse.
Totaloxidation von Kohlenwasserstoffen
Grundsätzlich realisiert das BEKOKAT-System eine Totaloxidation von Kohlenwasserstoffen und damit eine absolut ölfreie Druckluft. Und zwar in einem konzentrierten, umfassenden Prozessschritt nach der Verdichtung. Somit erfolgt die komplette Druckluftentölung in nur noch einer einzigen Anlagenkomponente. Diese arbeitet unabhängig von den Umgebungsbedingungen, der ÖlEingangskonzentration und der relativen Feuchte der Druckluft.
BEKOKAT widmet sich sämtlichen Verunreinigungen in der vom Verdichter zugeführten Druckluft. Das sind gemeinhin Schmierstoffe, Öle, Schwefeldioxid, Kohlenmonoxid, nitrogene Gase etc. Sie liegen sowohl in Gas- als auch in Dampf- und Aerosolform vor. Durch das BEKOKAT-Verfahren werden solche Luftinhaltsstoffe vollständig in Kohlendioxid und Wasser umgewandelt.
Letzteres kann bedenkenlos direkt und ohne weitere Umweltschutzmaßnahmen in das Abwassernetz geleitet werden. Sogar das bei der Abkühlung der Druckluft anfallende Kondensat ist dank des Katalyseverfahrens absolut ölfrei und kann ohne Aufbereitung ebenfalls in die Kanalisation fließen. Diese Totaloxidation und absolut rückstandsfreie Arbeitsweise realisiert derzeit kein anderes Verfahren.
Als Katalysator dient ein Granulat im BEKOKAT, das über Heizelemente auf eine Betriebstemperatur von etwa 150 Grad Celsius aufgewärmt wird. Im Katalysator werden die Ölmoleküle so lange gebrochen, bis nur noch ein Kohlenstoffatom verbleibt. In der Endphase der Katalyse sind die Ölmoleküle bis zu H2O und CO2 oxidiert.
Wesentlich ist, dass die Kohlenwasserstoffketten, also die Ölmoleküle, an jeder beliebigen Stelle „geknackt“ werden können. Sie werden stets so lange aufgebrochen, bis nur noch Kohlendioxid und Wasserstoff übrigbleiben. Die unterschiedlich langen Kohlenwasserstoffketten aus ölfreien und ölgeschmierten Kompressoren stellen also für BEKOKAT keinerlei Problem dar.
Nicht immer bekannt ist auch, dass die sonst häufig eingesetzten Aktivkohlefilter keine polaren Verbindungen, wie Olefine, Alkohole, Glycole oder Ketone adsorbieren können. Das BEKOKAT-System entfernt dagegen auch diese Stoffe vollständig aus der Druckluft. Im weiteren BEKOKAT-Prozessverlauf wird die gereinigte Druckluft in einem Wärmetauscher auf zirka 10 bis 15 Grad Celsius über Eintritt abgekühlt und steht für die jeweilige Anwendung zur Verfügung.
Mit dem BEKOKAT-Verfahren ist es erstmals möglich, konstant absolut ölfreie Druckluft mit einem maximalen Restölgehalt von kaum mehr messbaren 0,003 Milligramm pro Kubikmeter verdichteter Luft zu erzielen. Eine Qualität also, wie sie in den höchst anspruchsvollen Bereichen der Medizin und Pharmazie sowie der Lebensmittelverarbeitung und -verpackung benötigt wird.
Wirtschaftlich äußerst vorteilhaft ist schließlich auch die enorme Standzeit des speziellen BEKOKAT-Granulats, das erst nach gut 20 000 Betriebsstunden ausgetauscht werden muss. Im Vergleich dazu ist die Lebenskraft eines Aktivkohlefilters selbst unter perfekten Arbeitsbedingungen bereits nach etwa 500 Betriebsstunden erschöpft.
Seit Frühsommer 2008 ist das BEKOKAT-System beim Metallverarbeiter Horstmann rund um die Uhr störungslos im Einsatz. Und ein gutes Umweltgewissen hat die Horstmann GmbH & Co. KG dazu, denn seit Einsatz des BEKOKAT kann das Kondenswasser aus der Druckluftanlage problemlos und ohne teure Aufbereitung direkt in den Abwasserkanal eingeleitet werden.
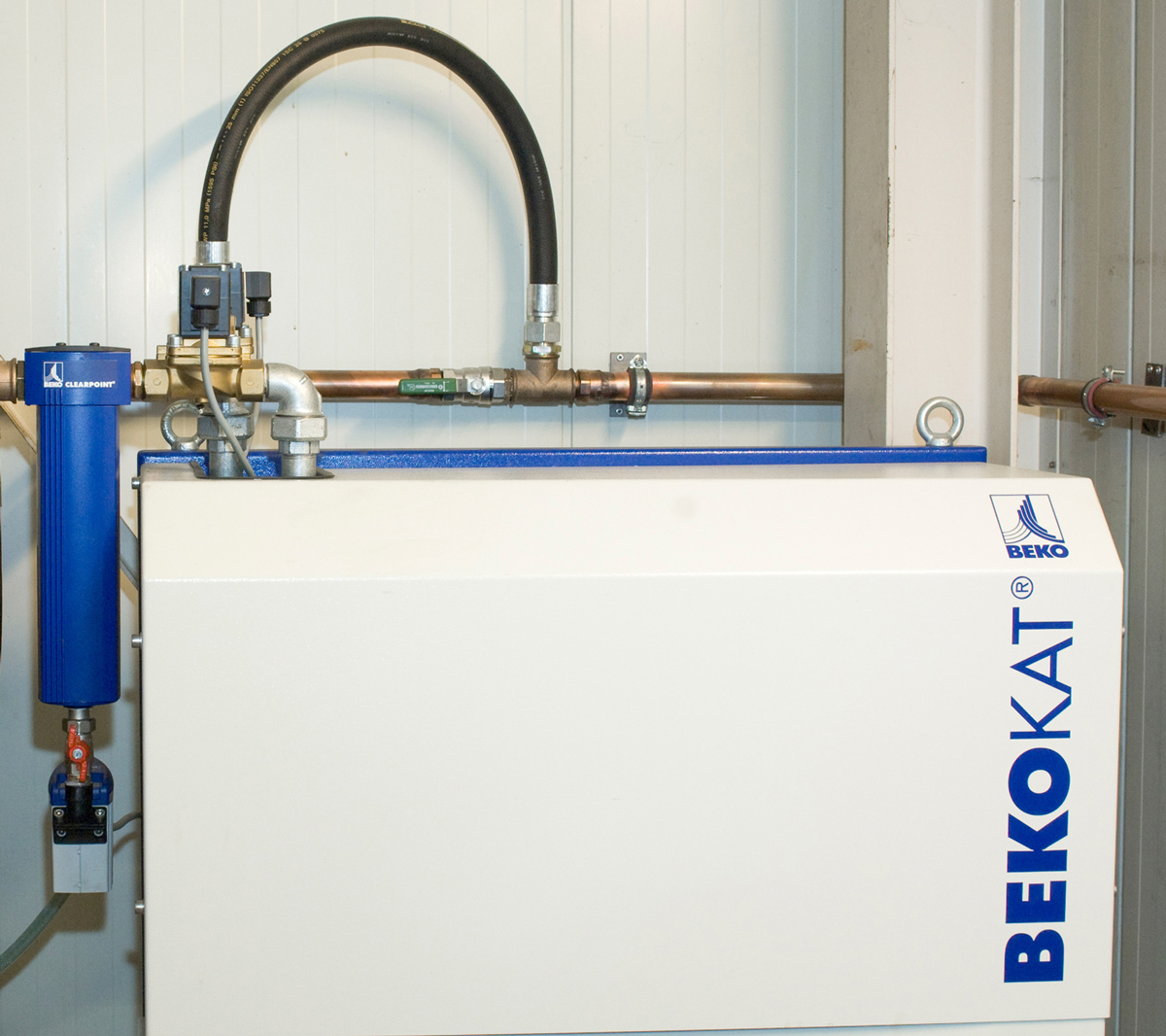
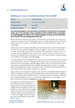