Compressed-air processing in the food industry
Industry: | Food & beverages |
Customer/Location/Year: | Nukameel,Weert (Netherlands), 2014 |
Use of compressed air: | Conveyor air, process air |
Installed products: | DRYPOINT RA, BEKOMAT |
Approximately 150 tons of powdery raw materials for milk replacers need to be conveyed daily from road tankers into silos in the Dutch company Nukamel. Lowly compressed air serves as the transport medium. In the event that it contains too much humidity, the system is threatened by an obstruction: through clogging of the feed hoses with encrusting powder. Exceptional local conditions do not make things any easier.
The address "Industriekade" does not suggest it – but we are in the purest idyllic Dutch scene: directly on the doorstep flows the South-Willem's Canal. On the opposite shore, a windmill slowly turns its wings in the light summer breeze and casts a cooling shadow over the campsite directly at its feet. And, in the neighborhood, you can hear children playing in the gardens of their parents'houses. The idyllic world of Weert near Roermond is perfect – and that's what it should also be in the future. Bright, sunny, and pleasantly peaceful.
This is exactly the challenge that industrial enterprises, which perform their daily work in the midst of this Dutch idyll, have to face. They live with strict noise-protection regulations - despite the location being pro-business. And also with the natural high air humidity of the environs rich in water. Just like Nukamel, the first producer worldwide of milk replacers for animal rearing, which was founded in 1954. Based in the traditional milk-producing countries Netherlands and Belgium, Nukamel today is represented in more than 40 nations throughout the world.
Milk replacers represent, worldwide, an indispensable food product in animal rearing during the first weeks. They serve, for example, as a substitute for mother's milk or when raw milk for the feeding is not sufficiently available. In addition, businesses which exclusively specialize in rearing often do not have the possibility to feed the raw milk that has been produced internally. These companies are also dependent on milk replacers from Nukamel that can be stored over a long period of time.
The extremely different nutritional demands of the various animal species in the individual life phases require a high level of knowledge regarding the right formula. With more than 20 brands that orient on special nutritional demands, Nukamel promotes the healthy growth of calves, piglets, lambs, chicks, and other young animals. All the formulas are exclusively composed of natural raw materials.
What these basic raw materials have in common is their powdery consistency – and their delivery by road tankers to the Dutch Nukamel works directly at the South-Willem's Canal, and virtually in the middle of a residential area.
Approximately 150 tons of powdery raw ingredients daily
Approximately 150 tons of raw ingredients daily reach their destination in Weert in up to five road tankers. No destination like any other – this is ensured by the local noise-protection regulations. These do not allow the transport of the powdery freight – as is normally the case – with lorry-internal compressors from the tank into the Nukamel silos by means of compressed air. "Too loud" is what the local limit values say.
Therefore, the generation of compressed air at Nukamel is implemented with a compressed-air system which was specifically installed for the discharge of the raw material road tankers. It consists of an extensively noise-encapsulated, lowly compressing compressor deep inside the complex of buildings. Low compression is applied because the tanks of the road tankers may only be loaded with a maximum of two bars.
The compressed air flows its long way from the compressor via a tube system in a C-pipe dimension to the lorry and from there, together with the powder, to the silo. On this route, the typical problem of compressed air becomes apparent: its water content. On a beautiful summer day with an air temperature of 25°C and a relative humidity of 60 per cent, the intake air of the compressor contains approximately 13 grams of water per cubic meter. At a conveying-air demand of 1,000 m³/h, this corresponds to a considerable 13 liters per hour!
Through the cooling of the compressed and humid air, condensate precipitates: at the inner walls of the hoses on the way to the road tanker, in the tank itself, and in the hoses from the road tanker to the silo.
Generally, the combination of humidity with the powdery goods to be conveyed is precarious, and may involve manifold problems, stretching from losses in quality as a result of caking to the growth of bacteria in the product. Fortunately, at Nukamel, they remained untroubled by such drastic consequences, but they had to grapple with a considerable "logistic" problem: the humidity in the hoses affected the efficiency of the powder transport, namely by the progressing deposition of the raw material powder on the humid insides of the hoses, involving a threatening obstruction of the transport system through "arteriosclerosis".
In order to avoid this obstruction, an emergency operation needed to be carried out after two or three emptied road tankers, respectively: the mechanical cleaning of the dismantled hoses through scraping out, brushing out, and blowing out – with a time expenditure of two to three hours at each time.
In mid-2013, the situation became precarious with the increased delivery frequency of a particularly hygroscopic powder raw material. The frequency of the arriving road tankers and the cleaning efforts involved were not justifiable, neither from the organizational nor from the economical point of view. Projections indicated ten to twelve hours not worked per week, meaning four days in a month. This, in turn, corresponded to an approximate calculative amount of 3,000 euros per month for Nukamel, not to mention the additional cleaning efforts regarding the lorry tanks themselves, even though these efforts were in-cumbent on the shipper.
Therefore, there was an exceedingly urgent need for action, and the task was clear: the provision of dry transport air! But there was one problem: the low compression of the conveying air of merely 1.8 bar. Commercial compressed-air dryers are designed for significantly higher compression rates and - however paradoxical it may sound – are totally overstrained when not challenged enough.
The responsible Nukamel staff became quickly aware of the fact that conventional dryer designs would not lead to success. The solution was brought by a look at the Belgian Nukamel partner factory, which had already mastered similar challenges with the dryer technology from the German compressed-air system provider BEKO TECHNOLOGIES.
The design engineers and system planners from BEKO TECHNOLOGIES only needed three months from the first planning session to the realization in order to provide for total relief also at Nukamel in the Netherlands, meaning for absolutely dry compressed air.
Refrigeration dryers for lowly-compressed air
A refrigeration dryer of the DRYPOINT RA series from BEKO TECHNOLOGIES was installed, which was specifically dimensioned for the requirements of lowly-compressed air.
In the DRYPOINT RA, compressed-air drying is effectuated via an optimum heat exchange through a counter-flow process over the entire section. Here, the air flows in a downward-directed movement without any disadvantageous diversions. This generously-dimensioned counter-flow heat exchanger which is composed, amongst others, of an air-air and an air-refrigerant heat exchanger, cools the compressed air down to a temperature of +3°C. In this respect, the size of the heat exchanger not only promotes particularly effective cooling but it also reduces the flow resistance to an absolute minimum. This aspect is the unconditional requirement for successful utilization at the lowest compression, which is the case at Nukamel.
The hot compressed air that is saturated with humidity is pre-cooled in the air-air heat exchanger when entering the refrigeration dryer. Through this, the cooling performance of the refrigerant, which is required in the following air-refrigerant heat exchanger, is reduced and the system is particularly energy-efficient.
Gravity supports a specifically high droplet separation of almost 99 per cent. In the very large condensate collecting space with subsequent recirculation, the flow rate is strongly reduced. Therefore, the entrainment of already separated condensate is reliably avoided.
Condensate discharge serially included
Like most of the DRYPOINT RA refrigeration dryers, the model that is installed at Nukamel is also serially equipped with a level-controlled BEKOMAT condensate drain. It functions many times more effectively and reliably than, for example, time-based or even float drains, which are used in most cases. The BEKOMAT is able, for example, to discharge the condensate without any loss of compressed air – cost savings which sometimes exceed the costs for the entire power consumption of the refrigeration dryer.
Prior to leaving the DRYPOINT RA, the dried, cold compressed air is re-heated in the air/air heat exchanger. This significantly reduces the relative air humidity, and up to 60 per cent of the employed cooling performance is recovered.
As regards the Nukamel example, this means: the air with a temperature of 180°C that is supplied from the compressor reaches the intermediate cooler with approximately 60°C, and is cooled down to approximately 3°C during the drying process. At the outlet of the DRYPOINT RA and subsequent to re-heating, 22°C are measured again: the ideal transport-air temperature. And the air humidity? When entering the dryer, it was at 100 per cent, and after the process, it only amounted to 30 per cent, meaning ideal conditions also when it comes to this point.
Perfect values which, by the way, did not need to slowly level off after the installation at Nukamel. Supplied as a "plug-and-play" system which is completely accommodated in just one housing, the DRYPOINT RA could immediately unfold its full power.
Compressed air "cut and dried"
The monitoring of the functioning and efficiency of compressed-air drying is also "a breeze" for Nukamel. This is implemented by the user-friendly control of the system via an operating unit at the instrument housing.
In addition to the functional check of the dryer, the control also takes over the monitoring of the serially integrated level-controlled condensate drain – including the indication of any trouble indications. An Advanced Draining System (ADS) records the status indications of the condensate drain and releases a corresponding warning message, if required. Even the test function of the drain can be centrally triggered via the control.
Well, everything is "cut and dried" at Industriekade 32 in the idyllic Weert near Roermond. And it is even quieter there – since not only the air hoses remain absolutely dry now but also the inside of the lorry tanks. And this means less cleaning effort needed on location. Both the neighbors and the shippers are happy about that.
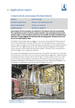